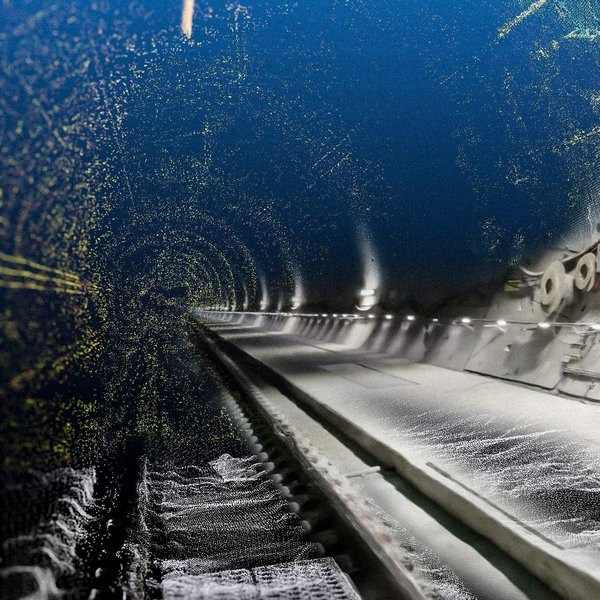
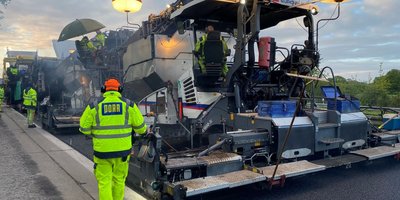
Digitalisation: How we set records
To lay as much asphalt as possible in the shortest possible time, first of all you need the innovative compact asphalt construction method. Secondly, you need LEAN-synchronised processes and quality assurance. Third is real-time support from digital tools for logistics planning. Fourthly, extensive compaction control and surface temperature measurement. And fifthly, an experienced team of experts. Everything has to run like clockwork – from the paving processes, material scheduling, and timing of the removal of the milled material with subsequent recycling to the transport of the mixed material and handover to the next shifts. You need a plan B for every eventuality in order to be able to immediately compensate for shortages of staff, machinery, or transport lorries. This is the short version. Now here comes the longer one.
Fast
From April 2024, we have been working in a consortium with our subsidiary G-S Straßenbau, Bunte, and Eurovia to renew a total of 39 kilometres of the carriageway on the A3 motorway between the Hünxe and Emmerich junctions in the direction of Arnhem. It has been done in five construction phases and mostly with full road closures. Because to minimise the impact on the diversion routes and the budget, everything had to happen quickly. So we and our client, the Rhineland branch of Autobahn GmbH des Bundes, set ourselves the goal of achieving new record times. In 2022, we refurbished 10 kilometres of road surface on the A3 motorway in seven days. We thought that was the maximum possible. But we were wrong. In April, we completed the third and longest construction section between the Hamminkeln and Rees junctions, measuring 13.6 kilometres, in the same amount of time. According to our client, this was the largest area of road surface renewal in Germany this year, but still not the maximum. For us, it was the warm-up before the main event.
The material from milling off the old 12-centimetre-thick surface course was processed in the asphalt mixing plants and reused on the construction site.
Faster
After a long break over the summer and the postponement of one construction phase until September, the last three construction phases of the project in the direction of the Netherlands were merged. Our coordination efforts were enormous. The material from milling off the old 12-centimetre-thick surface course was processed in the asphalt mixing plants and reused on the construction site. We laid the asphalt binder course and surface course in a single pass using the InLine Pave method. This innovative hot-on-hot process is almost twice as fast because the route is not travelled several times and there is no need for cooling between the application of the layers. We were able to apply the markings after just 24 hours of cooling the surface course, and also significantly reduced the material usage. Our meticulous planning of production quantities and construction site logistics were crucial for laying the large quantities of mix at the same time. We used the Smart Site One (SSO) software to do this. It also served as a central platform for collecting and networking data from other digital tools – such as the extensive compaction control system that we used to support the roller operators. This not only enabled us to minimise sources of error during paving in real time, but also to document for our client that compaction was consistently good along the entire paved section. In SSO, we also recorded the surface temperatures measured right after asphalt paving.
PORR
By applying our commitment and expertise, we demonstrated on the A3 project that digitalisation allows us to go beyond simply increasing efficiency and push the boundaries of what is possible. Asphalt paving is a highperformance sport that requires extreme concentration in challenging conditions. Live electronic measurements of compaction quality and surface temperature reduce the workload for our teams on the construction site, especially in the cockpit. And we give our client the necessary security.