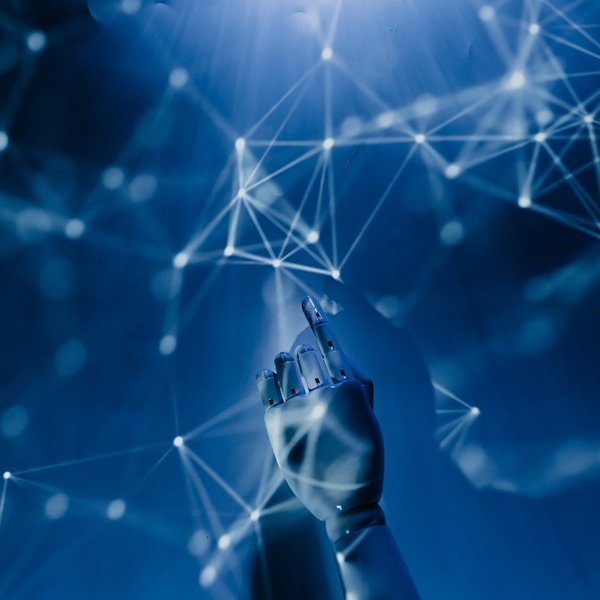
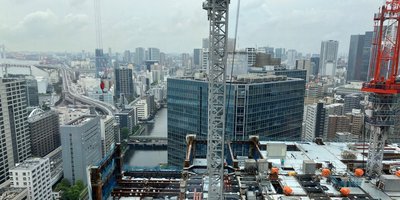
LEAN in Japan
We love optimisation. We question established structures. We are aways on the lookout for ways to create better conditions – for every service provider at PORR. For us PORRians from the Lean Construction Management Master's programme, organising an excursion is mandatory for graduation. So why not travel to the country where this way of thinking actually originated? Namely, Japan. With 36 participants from the construction industry – including ten PORRians from Austria, Germany and Poland – the week-long event started in Tokyo on 15 May.
A look beyond the borders
We were able to gain our first insight into Japan’s construction culture at the site of some 43-storey twin towers. We looked down at the construction site from a skyscraper built in 1984. This will be demolished and replaced by the North Tower as soon as the first tower is finished. What we realised in that very moment: Japanese buildings have a shorter lifespan. And space is scarce. Just how scarce is something we were about to learn.
In Japan, we were able to see how an old building is replaced by a new one when we observed a hospital being built right next to the existing hospital. And right next to it in this case means only a few centimetres away. There is no such thing as space for construction equipment here. As a European, it is almost impossible to imagine. But in Japan they make do with a steel platform on which space is created for excavators and materials. So we learned that our big challenges – a lack of space or delivery logistics – are even more a part of everyday construction here. And we marvelled at the kind of equipment in use – tiny cable excavators, small-scale telescopic booms.
There is also a different approach to what clean and tidy means. White gloves are part of the standard equipment and are worn permanently on the construction site. You almost get the impression that the colleagues have these gloves so that they don’t get anything dirty on the construction site. That’s how clean it is. The demands on safety at work are also high, but they are a matter of course for the construction site team: They meticulously cordon off, protect, enclose, cover with tarpaulin, or surround with cones as much as possible. One thing above all applies here: Personal responsibility. When asked how everyone can be motivated to keep such strict order, the answer was: “You learn that in kindergarten”. And children in Japan really do clean the school together at least once a week. “Here, things are the way we were taught they should be”, said one participant. Very apt.
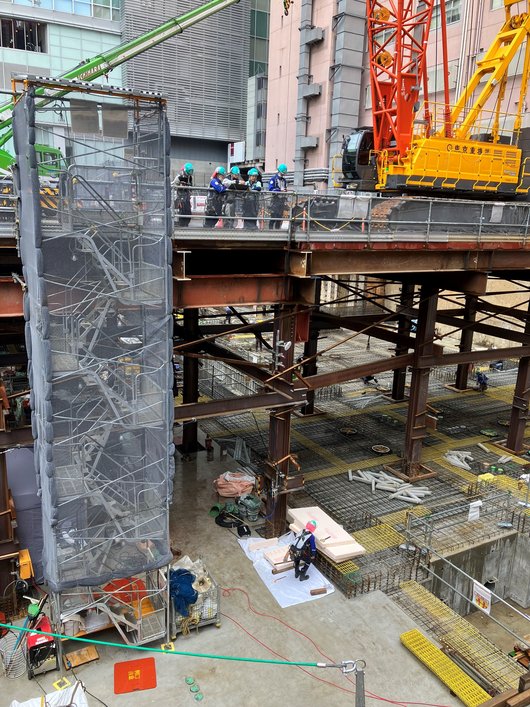
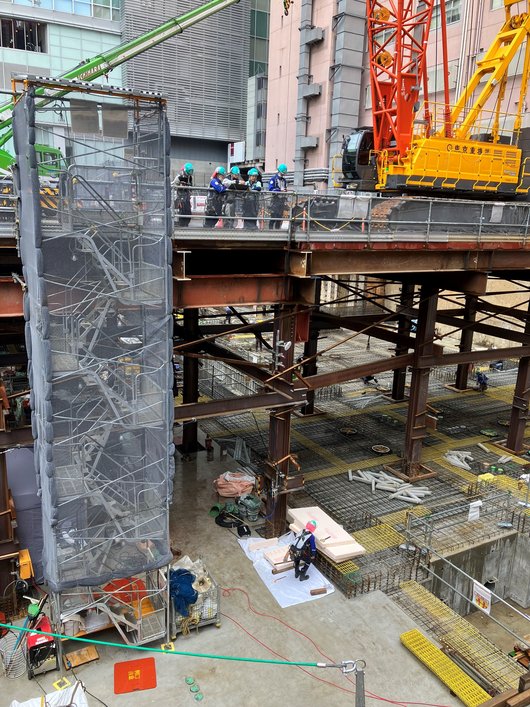
Different countries, different methods
We were also able to visit a TV and radio station under construction for the Japanese broadcaster NHK. It was striking that there is no classical reinforced concrete construction. Instead, trapezoidal sheet metal is installed between load-bearing steel structures, which also serves as lost formwork because concrete is poured directly onto the aluminium sheet. For this purpose, the edge elements as semi-prefabricated parts are partly produced directly on site, on multi-storey platforms and conveyor belts. All girders are provided with appropriate safety precautions even before they are moved, in order to ensure the protection of personnel, especially in critical areas. For example, the girders are already equipped with lifting points and eyelets for attaching cables, lines and lighting.
On the other hand, we could only smile politely at other things they tried to pass off as innovations. Multi-layer glazing, for example, is a novelty in Japan. On the other hand, we learned something about completely new challenges: In the course of a visit to the Tokyo University of Science, we met a professor who develops construction elements for earthquake stability and we inspected a building on which these oversized shock absorbers were even retrofitted on the outside. Such exoskeletons are likely to enjoy a substantial demand in earthquake-prone Japan, especially for existing buildings.
The cradle of LEAN
On the evening of the second day of the excursion, the group set off by Shinkansen bullet train for Osaka – the place where the World Expo will be held in 2025. For this purpose, an island is being built, a so-called land reclamation project covering 390 ha. It will be handed over to the respective countries for development during the EXPO. Under the motto Designing Future Society for Our Lives, Austria is also participating with a national pavilion. We got to take a look at the enormous earthworks in the sea.
In a building construction project with a floor area of 1,600m2 and a final height of 150m, we gained insights into sophisticated building technology using gravity ventilation, daylight sensors and efficient combined heat and power generation. And we were once again able to admire the structured construction site management. The following morning was spent at Takenaka, one of Japan’s largest construction companies, which has realised some of the most prestigious buildings in the country as a design-build provider. And it has been doing so for more than 400 years. The roots of the company go back to 1609. We were also amazed by the projects. For example, Takenaka realised the Tokyo Tower as one of the city’s landmarks from planning to construction. We talked about the principle of integrated project management and the experience gained with it in Japan. In terms of implementation, we feel they are a bit ahead of us here, but we could certainly see parallels and similar challenges.
The last item on the agenda was a visit to the Mitsubishi Building in Osaka, which is still under construction. Although the steel construction work is still in full swing on the top of 32 floors, the lower floors are almost ready for use with functioning building services. Our tour ended with a fantastic view over the city. At the end of the excursion, part of the group went to Toyota; to call this the cradle of LEAN creation would only be a slight exaggeration. For it is here in the Japanese automotive industry that the quest for optimisation and focus on people actually originated. With two former foremen from Toyota car production, we spent a day working on improvements and methods on how to identify the need for improvements. We realised how small, seemingly banal changes can make people’s everyday lives easier and increase production at the same time. Win-win all the way.
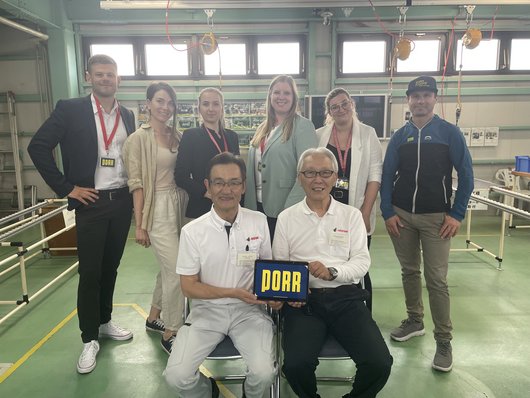
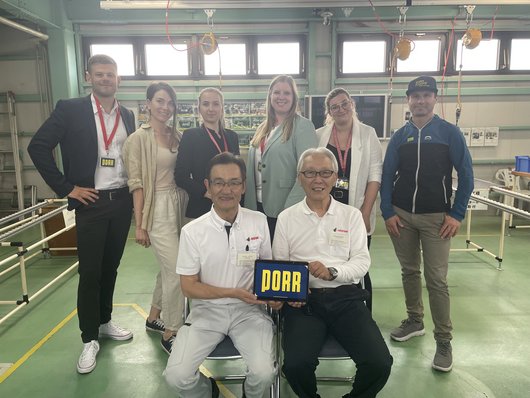
A passion for detail
Workers napping in the break room. Green tea at the construction site reception. Manga-style noticeboard. And lots of bowing. Some clichés hold true. But we also saw on the construction sites the attitude, the passion and the pride of the people who work here. Even if efficiency suffers somewhat under the perfect order – because of course that takes time and resources – we can certainly learn something from it. What takes longer here or needs more manpower seems to pay off in economic terms, it is passed on from project to project. Attention to detail as a business model, that appears to work in Japan. But of course it is not the promised land. There is a lot to question. But we are happy to see what is possible.