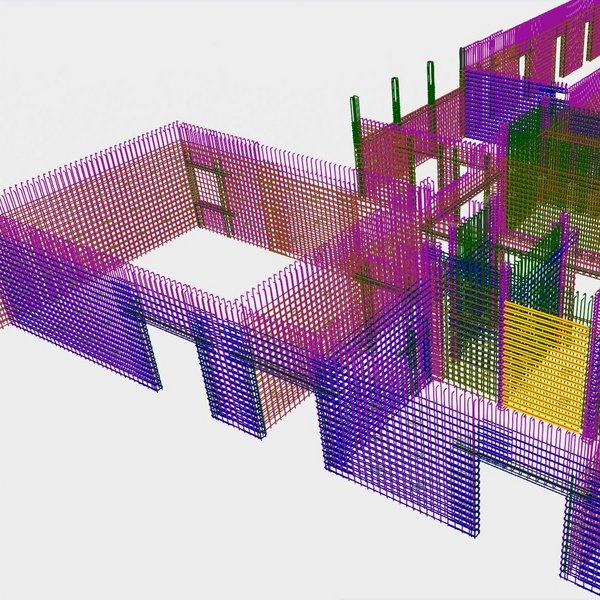
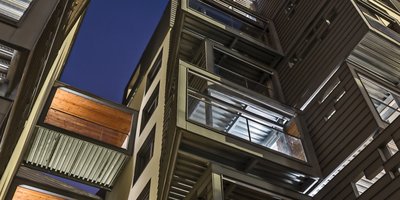
Modular construction: Hype with limits
Modular construction is seen as a beacon of hope for fast, efficient and cost-effective construction in the future. At the imm cologne trade fair, the topic was more present than it has been for a long time. "There is hardly a construction method that captures the spirit of the times as much as modular construction. Costs and quality can be planned precisely, scaled more easily and controlled. (...) Whether it's the private construction of a detached house or buildings for public spaces: modular construction has immense potential that will continue to unfold in the industry in the future," is the consensus of the organisers. Modular construction is characterised by a high degree of prefabrication. This is nothing new. As early as 1914, the famous architect Le Corbusier was granted a patent for the Domino construction system for the industrial series production of houses in reinforced concrete skeleton construction from prefabricated parts. Prefabricated houses for small families as well as large-volume prefabricated buildings made from modules have been established since the 1970s at the latest.
The advantages
According to VdW Südwest, the Association of the Southwest German Housing Industry, the current market share of modular buildings in Germany is still only around 4%. The quickly constructed modular buildings of the past are often perceived as cheap buildings and do not enjoy the best image. And yet there is currently a hype surrounding modular construction, which is easy to explain: There is a huge demand for quick, easy to realise, affordable and sustainable solutions. Modules with a high degree of prefabrication offer many advantages on the construction site. The production of components - walls, stairs or entire room modules - in series and the subsequent assembly on site are efficient, resource-saving, easy to plan, economical in terms of transport and logistics, time-saving and cost-effective. In addition, well-planned modules can be easily dismantled and reused in the interests of the circular economy. In times of scarce living space and redensification, for example, an office building can be quickly and easily converted into a residential building or school in the future.
The limits
Modern projects such as the twelve-story residential tower Stories by Olaf Gipser Architects or the roots show that modular buildings today do not have much in common with the typical prefabricated building from the 1970s. Both are timber hybrid buildings in Hamburg's harbour district. Architects and planners are also increasingly turning to modules for some individual projects: from aluminium façade panels and prefabricated concrete staircases to reusable room modules - for maximum flexibility and easy conversion of buildings in the future. However, as long as there is no valid material bank, i.e. a well-maintained database of available components and modules, the efficient reuse of existing components will remain a mammoth task and will hardly get beyond dedicated amateur projects. Although the European Commission is planning such a material bank, concrete progress in its realisation is still a long way off. And of course, many construction projects will still require individual planning and construction in the future, despite the material bank. Especially projects that have to fulfil special safety requirements. Infrastructure - from tunnels to hydroelectric power stations - often cannot be built with off-the-shelf modules for technical reasons. In building construction, there will also always be projects that cannot be realised with modules due to certain architectural requirements or difficult site conditions. Modular construction is therefore a good solution for many modern requirements. But - as is so often the case - not for all.