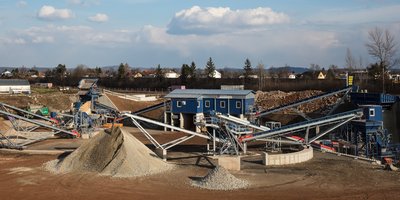
Pirka recycling plant
PORR Umwelttechnik has set up a stationary building material recycling plant in Pirka to promote recycling management and sustainability.
By establishing this plant, PORR Umwelttechnik GmbH is taking a future-oriented step towards achieving sustainability. A wide range of recycling materials in product quality can be produced at the plant.
-
ContractorPORR Umwelttechnik GmbH
-
Project typeEnvironmental engineering
-
Project scopeConstruction of a permanent recycling plant and the renovation and integration of an existing gravel and crushed stone processing plant
-
Construction start06/2017
-
Construction end12/2017
Background
The use of recycled building materials within a sustainable construction process is becoming increasingly important in the construction industry, and quality requirements are constantly growing. PORR Umwelttechnik is keeping up with this trend and, after six months of work, has completed the construction of a modern recycling plant in the municipality of Seiersberg-Pirka, south of Graz, Austria. The new plant will enable the production of a wide range of product-quality recycled materials.
Renovation and extension of an existing plant
An existing gravel and crushed stone processing facility formed the basis for the project. The existing plant was completely overhauled and integrated into the newly constructed recycling plant in the course of two stages of development. The two extensions (first and second plant sections) can be operated either separately or in succession. PORR Umwelttechnik commissioned BAG Klöch Aufbereitungstechnik GmbH to construct the plant. The necessary renovation work to the existing plant was undertaken by the company itself together with PORR Equipment Services GmbH, and all master building work, such as structural engineering, foundations, conduits and power connections, was completed by PORR Bau GmbH. The total costs for the facility amounted to 1.6 million euros.
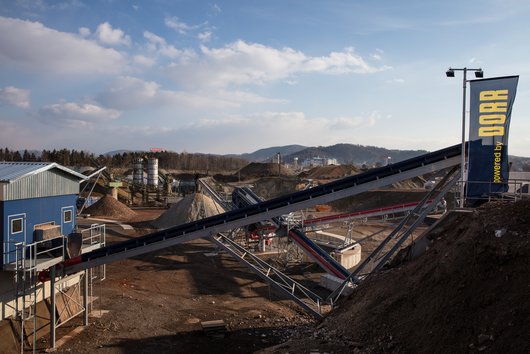
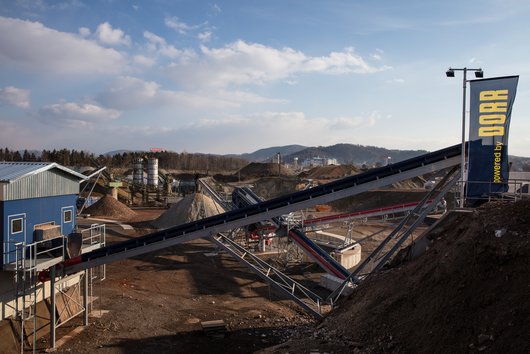
We are making a significant contribution to improving sustainability and conserving natural resources.
Work to convert the old gravel and crushed stone processing plant began in June 2017. The first extension to the plant includes the feed hopper, jaw crusher, screening unit, impact crusher and various conveyor and stockpile conveyors. As part of the overhaul of the existing plant, new plant components were added, including the magnetic separator, feeder and operating station. The screening unit, impact crusher and jaw crusher were refurbished in collaboration with PORR Equipment Services. As part of the second extension, a further feed hopper, a pre-screening unit, a light material separator, a dewatering screen, a manual sorting system and various stockpile conveyors were installed. The recycling plant is designed for a capacity of up to 150 t/h. Due to the tight construction schedule, all construction work on the plant was completed within six months by December 2017. This enabled PORR Umwelttechnik to establish a treatment process to produce high-quality recycled construction materials as an alternative to primary raw materials. The treatment process consists of two stages, which can also be operated individually.
The recycling process
The construction waste, such as building rubble, delivered to the plant is tipped onto an asphalted temporary storage area. Following a rough pre-sorting or pre-crushing process, a wheel loader is used to transfer the material to be processed either into the feed hopper of the first extension to the plant (first processing stage) or directly into the feed hopper of the second extension (second processing stage) – depending on whether it needs to pass through the entire plant or only sections of the plant.
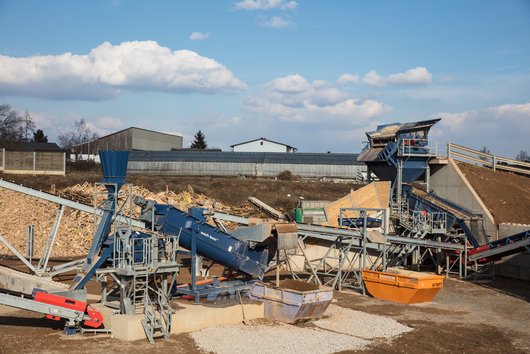
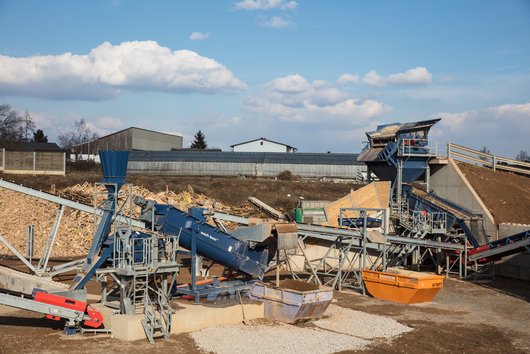
First processing stage
From the feed hopper, the mineral construction waste is transported to the pre-screening unit via the feeder. The initial separation of the construction waste takes place here – into fine, medium and coarse fractions. The fine fraction is stockpiled via a collector conveyor and a slewing conveyor. The medium fraction is transferred to the light material separator via a feeder belt with overbelt magnetic separator. The lightweight materials are collected in skips and disposed of externally if necessary. The fraction cleaned of lightweight materials is dewatered using a dewatering screen and delivered via a further slewing belt, where the fine fraction can be added. The excess water from the light material separator and the dewatering screen is fed into the sand trap area of an infiltration basin at the site, which is operated as a sedimentation tank. The settled solids are regularly pumped out and disposed of using a pump truck. The purified water is recycled and supplied to the light material separator. This minimises the need for fresh water.
The coarse fraction then reaches the picking belt. Contaminants and recyclable materials are removed manually at the manual sorting station. The materials that are removed in this process are stored in containers via disposal chutes and recycled. Iron and pure brick fractions are recycled. Non-recyclable materials are disposed of. A feeder transports the now contaminant-free coarse fraction to the feed hopper of the second extension or, in the case of dual operation, it can also be transported from the sorting cabin to a stockpile.
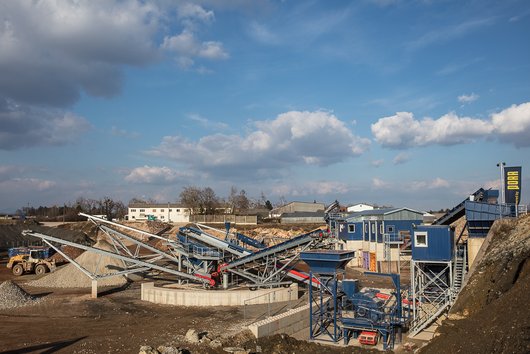
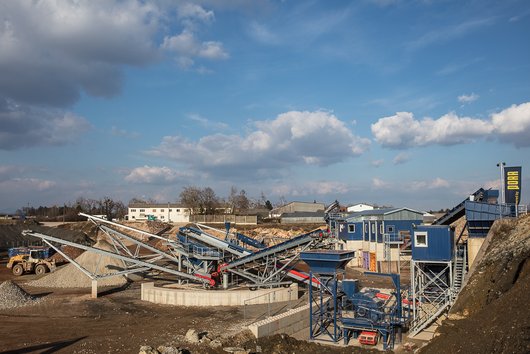
This recycling plant will separate approximately 180,000 tonnes of construction waste each year.
Second processing stage
Following manual sorting, a feeder conveys the material into the hopper. If the second extension is being operated separately, the material is instead delivered via a wheel loader or lorry. The hopper has a capacity of 40 m3 and acts as buffer storage if the material is delivered via wheel loader or lorry. The material is broken down to the desired grain size in the jaw crusher. The crushed material is transferred to a screening unit via an ascending conveyor with a belt scale and overbelt magnetic separator. Product classification takes place here, with the oversize particles fed via an ascending conveyor to a further impact crusher with pre-silo, and broken down to the required size. The screened fractions are held in stockpiles and quality assurance checks are performed. Different fractions can be produced at the new recycling plant and used in construction, contributing to the conservation of natural resources. The plant processes approximately 180,000 t of construction waste each year.
About the completed project
A modern permanent recycling plant was constructed in just a short period of time. Following sorting, wet processing and a crushing and classification process during the two processing stages, high-quality recycled construction materials are created, which are then reused.
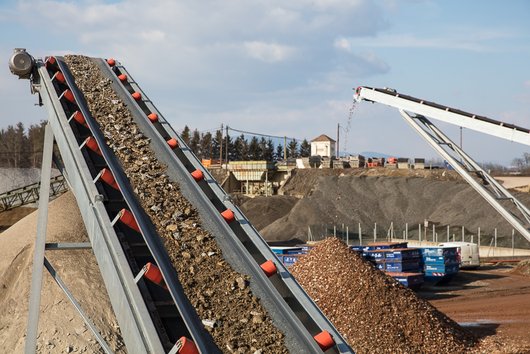
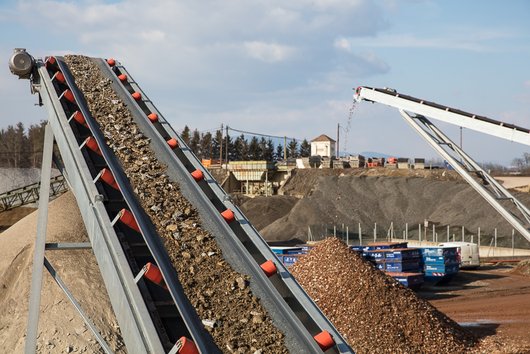