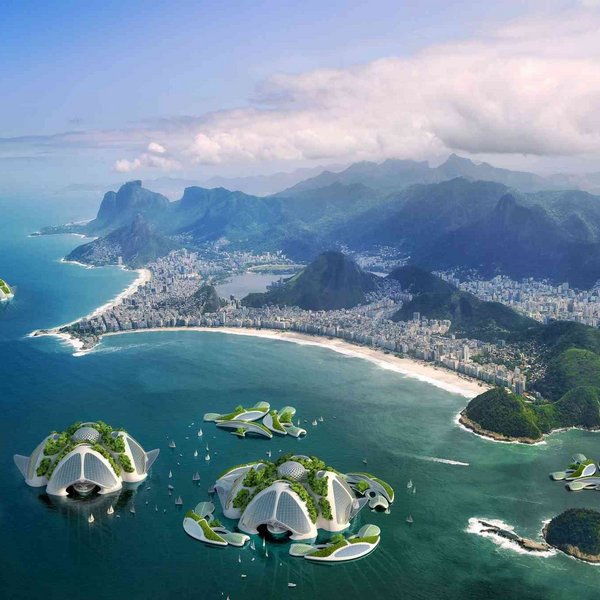
Sustainable solution: Roads made of plastic
We wear it on our bodies as a T-shirt, on our nose as sunglasses and in our ears as headphones. We smear it on our face and wash our clothes with it. We drink from it and even eat it. And 86 to 150 million tonnes of it are floating in our oceans. Plastic is simply everywhere. There are even micro and nano plastic particles in our bodies, MNP for short. And quite a lot of them as shown by a recent study: Researchers found 1.6 micrograms of plastic particles per millilitre of blood. That is equivalent to one teaspoon in 1,000 litres of water. And scientists from MedUni Vienna have found that, on average, 5 grams of plastic end up in the human gastrointestinal tract. That is practically like eating a credit card. Once a week.
Plastic as a construction material
Plastic is a barely manageable problem for our environment and one that is growing ever bigger. Some of the waste is recycled, of course, but much of it also ends up in the oceans or is burned, producing harmful CO2. But plastic can be used as a construction material. As shown by PlasticRoad. Nomen est omen. Because the Dutch start-up uses 100% recycled plastic as a base material for road construction. The idea is not entirely new: plastic is used to repair roads in parts of England, and in India it has even been mandatory since 2015. However, the recycled plastic replaces only a small fraction of the bitumen. What is new is that entire roads are now being built from plastic. This solves two problems at a single stroke: plastic waste is recycled, and road construction becomes more sustainable. The maximum CO2 reduction is estimated at 72%. And there are even more advantages besides.
The prefabricated modules from PlasticRoad are easy to assemble, making roadworks faster and less complicated. There’s no need for heavy foundations, no extensive excavation work. And the lightweight modules – one square metre weighs a mere 43 kilograms - are hollow on the inside. Pipes and cabling can be laid here and can also be repaired more easily when required. The hollow space can also store up to 300 litres of rainwater per square metre – a clear benefit in view of the increasingly frequent heavy rainfall events. After all, the sewers have not been built for this and so flooding occurs. With this system, however, the hollow space in the roads absorbs the water and gradually releases it into the soil.
New paths to sustainability
New paths can come from yoghurt pots, bottles, straws and the myriad other plastic products. PlasticRoad has been researching and developing the modules for years. The pilot project involves two 30-metre-long cycle lanes in the Netherlands. One tonne of recycled plastic was used per lane. That's 218,000 plastic cups. The data provided by sensors in the cycle lane make it possible to keep improving the product. After all, even a road made of plastic has to withstand the high stresses of traffic. But because the plastic content improves the flexibility of the surface, the road should be even more durable. A coating also prevents micro and nano plastic particles from being released into the air through abrasion. What’s more, it protects against UV radiation and any resulting damage. However, only years of practical tests will be able to prove how resilient the PlasticRoad actually is. So far, however, the results seem very promising.
Ecological concepts in road construction
Asphalting roads today is already potentially far more sustainable than a few years ago. “Here so-called warm asphalt is a genuine innovation”, says Hermann Lammen, Head of the Construction Materials Lab of Oevermann, a PORR Group subsidiary. And it’s the temperature that makes the difference. “With conventional asphalt, also called hot asphalt, it reaches more than 150°C. In Germany, warm asphalt may only be heated to 150°C and processed at 120°C. This is already a huge leap towards colder”, explains Lammen. And what makes warm asphalt more sustainable? “Among other things, it leads to a significant reduction in vapours and aerosols released during asphalt paving. At the same time, the energy consumed and CO2 emissions produced during its manufacture at the asphalt mix plant are reduced. They account for almost two thirds of total emissions in road construction – that alone makes an enormous difference. The lower mixing temperature also means that the bitumen is less stressed. Despite more difficult paving conditions, the asphalt layers are expected to last longer”, says Lammen. And that is not only better for the environment. The workers and neighbours of the asphalt mix plants also benefit.


PORR is also making road construction more sustainable by applying digitalisation. After all, efficient processes also mean less waste and fewer emissions. From project preparation through to execution and follow-up – digital BuildingProcessOptimisation, BPO for short, guarantees an end-to-end digital process in road construction. This makes the work much easier. After all, the successful asphalting or concreting of a road begins with the planning of the logistics processes. All data is available to everyone involved during the build phase. “Thanks to the optimum communication between the mix plant and the paving team, we can react quickly to different paving situations. And optimise processes using standardised evaluations. Since launching BPO, we have successfully realised more than 500 projects”, explains BPO project manager David Bachinger from PORR. And of course Building Information Modeling, or BIM for short, is also becoming more and more standard in civil engineering. In short, there are already very clever concepts available for making road construction more sustainable. And more R&D is underway every day. For a better future.
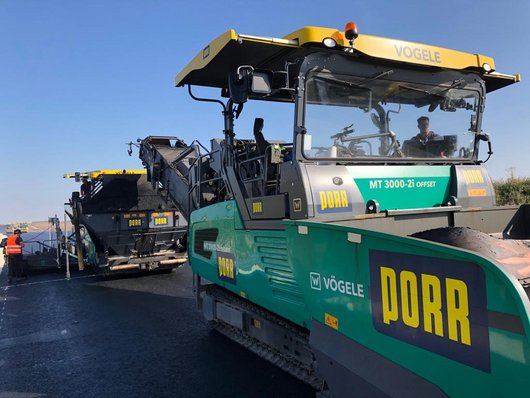
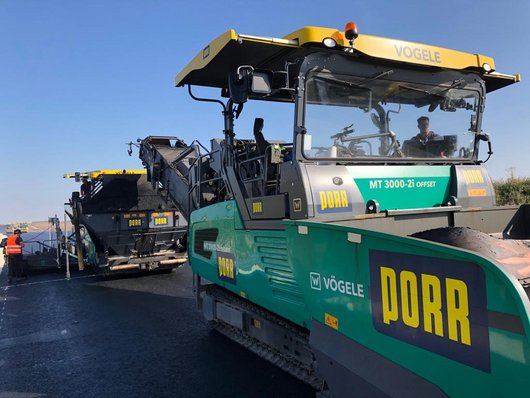