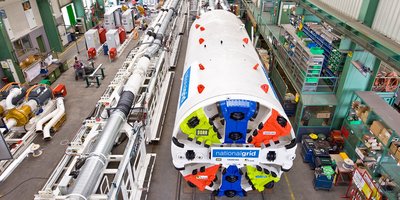
Humber Crossing – Feeder 9 Replacement
Die bestehende Gas-Pipeline Feeder 9 muss ersetzt werden. Sie soll durch einen neuen Tunnel unter der Mündung des Humber im Nordosten Englands geführt werden.
4,9 km werden im Hydroschild-Verfahren aufgefahren. Nach Abschluss der Arbeiten darf sich das Humber Pipeline Tunnel Joint Venture und National Grid über einen Weltrekord freuen: die längste in einem Stück verlegte Gas-Pipeline in einem Tunnel.
-
AuftraggeberNational Grid plc
-
AuftragnehmerJoint Venture bestehend aus PORR (40%), SKANSKA (40%), A.HAK (20%)
-
AuftragsartDesign & Build
-
ProjektartTiefbau, Tunnelbau
-
LeistungsumfangBau eines 4,862 km langen Tunnels für die Verlegung einer Gas-Pipeline
-
AuftragsvolumenGBP 91,3 Mio. (rd. EUR 108 Mio.)
-
Baubeginn09/2016
-
BauendeEnde 2020
Hintergrund
Zwischen Paull am Nordufer des Humbers und Goxhill am Südufer verläuft eine 5 km lange bestehende Pipeline in einem Graben entlang des Flussbetts. Durch den Einfluss der Gezeiten ist das Flussbett im Laufe der Jahre erodiert, was zur Freilegung der Pipeline führte. National Grid erkannte das Problem und entwickelte eine technische Lösung zum Schutz der Pipeline, indem potentiell exponierte Bereiche mit Kies-Säcken und darüber angeordneten Betongründungsplatten abgedeckt wurden. Die Platten enthielten Plastikwedel, um Seegras nachzuahmen und die Ansiedlung von Sand und Schlamm zu fördern.
Diese Lösung gewährleistete, dass die Pipeline kurzfristig weiterhin normal funktionierte und auch Inspektionen haben gezeigt, dass sie vorerst effektiv und erfolgreich war – aber nicht von Dauer. Im April 2016 hat National Grid einem Joint Venture aus PORR, SKANSKA und A.HAK den Design-Build-Auftrag erteilt, die bestehende Feeder 9 Gas-Pipeline durch eine neue Gashochdruckleitung DN 1.050 mm zu ersetzen.
Enge Platzverhältnisse und die Tunnellänge von knapp 4,9 km ohne Zwischenschächte zählen zu den größten Herausforderungen.
Projekt
Als langfristige Lösung wird nun ein 4,862 km langer Tunnel gebaut. Dieser wird im Hydroschild-Verfahren mit einem Durchmesser von 4,38 m (Ø Innen = 3,65 m) aufgefahren. Der Tübbingausbau erfolgt mit sechs Tübbingsegmenten mit einer Dicke von 22,5 cm und einer Breite von 1,20 m. Die Tübbinge werden in allen Bereichen mit Bewehrungsstahl verstärkt, in den Bereichen mit einer Mindestüberdeckung werden sie zusätzlich mit einer Stahlfaserbewehrung versehen. Der Vortrieb startete im April 2018 und ist voraussichtlich nach 12 Monaten abgeschlossen.
Die Tunnelvortriebsarbeiten beginnen von einer Startgrube am Südufer der Mündung in der Nähe der Stadt Goxhill in Lincolnshire und schließen am Nordufer der Mündung in der Nähe von Paull in Yorkshire ab. Nach Abschluss der Tunnelbauarbeiten wird die Gas-Pipeline installiert, was eine Herausforderung darstellt. Aus Sicherheitsgründen sind keine Rohrschweißarbeiten im Tunnel erlaubt. Daher werden die 12 m langen Rohrabschnitte vorher auf der Baustelle zu Rohrsträngen verschweißt, bevor sie in die Pipeline eingeschoben werden. Anschließend werden die Rohrstränge von der Rampe mit Hilfe von zwei Einpresseinheiten in den Tunnel eingeschoben. Eine Besonderheit dieses Projekts ist, dass der Tunnel geflutet wird und die Pipeline unter Nutzung des Auftriebs mit erheblich geringerem Aufwand eingeschoben werden kann.
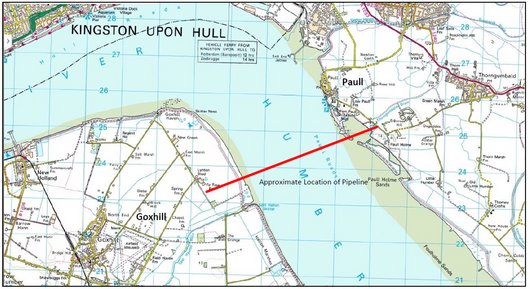
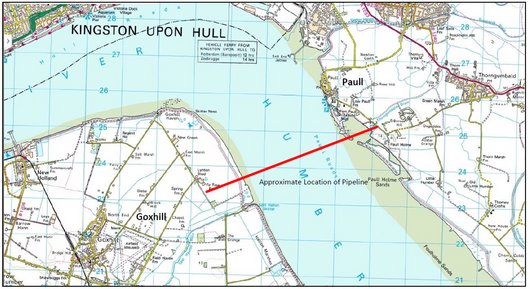
Bautechnische Details
Geologie
Der Vortrieb erfolgt bei minimalen Überdeckungen von 5 m und maximalen Überdeckungen von 33 m. Geologisch betrachtet werden zunächst über eine Länge von ca. 4.000 m Kreideformationen (Burnham-Kreide und Flamborough-Kreide) durchfahren. Zum Ende des Vortriebs wird man über eine Länge von ca. 800 m auf eiszeitliche Ablagerung (Mischböden aus Sand, Kies, Schluff und Ton), im Zielschachtbereich auf junge Schwemmböden, sogenannte Alluvialböden, treffen. Bei der Planung der Arbeiten sind Gezeitenwechsel von bis zu 6,5 m zu berücksichtigen. Die geplante vertikale Ausrichtung folgt einem Gefälleabfall von ca. 4% für eine Länge von 450 m. Unterhalb der Mündung verläuft der Tunnelvortrieb fast horizontal und ändert sich für die letzten 600 m zu einer Neigung von ca. 4% am Nordufer der Mündung. Die maximale Tiefenlage des Tunnels wurde optimiert, um die geltenden Vorschriften für anfallende Druckluftarbeiten in der Abbaukammer einzuhalten. Gleichzeitig werden auch die Anforderungen an eine ausreichende Felsüberdeckung erfüllt.
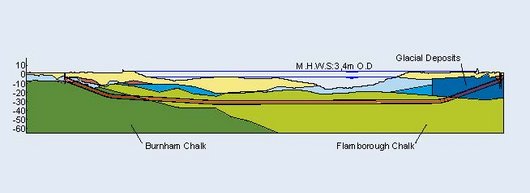
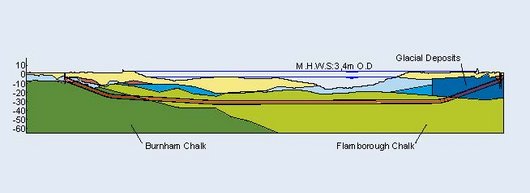
Herausforderungen
Für die Ausführung der Arbeiten waren zahlreiche projektspezifische Besonderheiten zu berücksichtigen. So erforderte etwa die Baufelderschließung auf sehr schlechtem Untergrund eine großflächige Bodenstabilisierung durch den Einbau einer bis zu 1 m dicken Schottertragschicht. Erschwerend hinzu kam, dass die LKW-Transportzeiten zur und von der Baustelle auf 5h/Tag begrenzt waren. Bedingt durch die küstennahe Lage der Baustelle kommt es häufig zu Starkwind, der zur Einstellung des Kranbetriebs führen kann. Dies wurde schon bei der Planung der Tunnelandienung berücksichtigt, um Ausfallzeiten zu minimieren. Bei Hochwasser wiederum kann es zu einer Überflutung der Baustelle kommen, weshalb sämtliche Installationen hochwassersicher ausgeführt werden mussten. Erhöhte Anforderungen an das Sicherheitskonzept und die Tunnellogistik stellten auch der geringe Tunnelinnendurchmesser und die Gesamtlänge des Tunnels. Überdies ist bei einem Hydroschild-Vortrieb in Kreideformationen davon auszugehen, dass große Anteile des Bodens im Flüssigkeitskreislauf dispergieren werden, was bei der Planung der Separieranlage ebenso berücksichtigt werden musste. Und schließlich sind in England die Health & Safety Anforderungen in Planung und Ausführung weitaus höher als in Zentraleuropa.
Positiv auf die gesamte Baustellenplanung wirkten sich die Erfahrungen aus, die die PORR beim Projekt Abwasserkanal Emscher BA 40 gesammelt hat, das unter vergleichbaren Bedingungen erfolgreich ausgeführt wurde.
Start- und Zielschacht
In Goxhill befindet sich die Baustelleneinrichtungsfläche für sämtliche Tunnelbauarbeiten. Der Startschacht für den Tunnelvortrieb hat eine Länge von 60 m, eine Breite von 7 m und am Portal eine Tiefe von 8 m. Eine ca. 140 m lange Rampe mit einer Neigung von 4% verbindet den Schacht mit der Geländeoberfläche.
Über die Rampe erfolgte die radgebundene Andienung der Tunnelbohrmaschine (TBM) für die Vortriebsarbeiten. Windbedingte Arbeitsunterbrechungen der Kranarbeiten am küstennahen Standort der Baustelle können hierdurch weitgehend vermieden werden. Zudem war es dadurch möglich, die TBM mit einer Gesamtlänge von 160 m vor Vortriebsbeginn komplett zu montieren.
Der Startschacht wurde im Schutz einer ausgesteiften Bohrpfahl- und Spundwandbaugrube hergestellt, welche in die Kreideschichten einbindet. Während der Aushubarbeiten wurde der Wasserspiegel in der Baugrube durch eine offene Wasserhaltung abgesenkt. Nach Einbau der mit der Verbauwand verankerten Ortbetonsohle konnte die Wasserhaltung abgeschaltet werden.
Der Zielschacht in Paull wird im Schutze einer kreisrunden Bohrpfahlbaugrube mit einem Durchmesser von 15 m und einer Tiefe von 12 m hergestellt. Auch hier wird der Aushub in offener Wasserhaltung erfolgen.
Vortriebsverfahren
Die Vereinbarung mit National Grid sieht zwingend den Einsatz einer TBM mit Tübbingausbau vor, wobei es dem Joint Venture überlassen war, das geeignete Verfahren auszusuchen. Die Wahl fiel trotz höherer direkter Kosten, aber aufgrund der günstigeren Risikoeinschätzung auf das Hydroschild-Verfahren. Die TBM-Anfahrt im Startschacht Goxhill erfolgt durch eine Glasfaser bewehrte Bohrpfahlwand und einen vorgelagerten
Dichtblock. Dabei werden die Anfahrkräfte über eine Rücksteifkonstruktion in die Schachtsohle eingeleitet. Die Ausfahrt erfolgt durch eine Glasfaser bewehrte Bohrpfahlwand in den mit Wasser gefluteten Zielschacht. Der Einbau einer gesonderten Dichtungs-Konstruktion ist daher nicht erforderlich.
Separation
Für die Separation kommt eine mehrstufige Separieranlage bestehend aus Filter, Zyklonen und Filterkammerpressen zum Einsatz. Insbesondere wird die Restfeuchte des Ausbruchmaterials aus dem Bereich der Kreideschichten auf ein für Transport und Deponierung verträgliches Maß reduziert.
Tunnellogistik
Da auf der gesamten Tunnellänge keine Zwischenschächte vorgesehen sind, müssen die Tunnellogistik und Notfallversorgung über den Startschacht erfolgen. Neben der Tunnellänge stellte der geringe Innendurchmesser des Tunnels von 3,65 m eine große Herausforderung dar.
Für die Tunnellogistik fiel die Entscheidung auf sogenannte Multi Service Vehicles (MSV). Gegenüber einer schienengebundenen Logistik haben diese viele Vorteile wie ein besseres Bremsverhalten auf rutschigem Untergrund, kleinere Dieselmotoren oder die direkte Sicht durch Fahrerkabinen auf beiden Seiten. Zudem ist so die Optimierung der Startschachtlogistik durch Rampen möglich, über die die MSV an die Geländeoberfläche fahren können, um dort direkt beladen zu werden. Zusätzliche Vertikaltransporte sind dadurch nicht nötig.
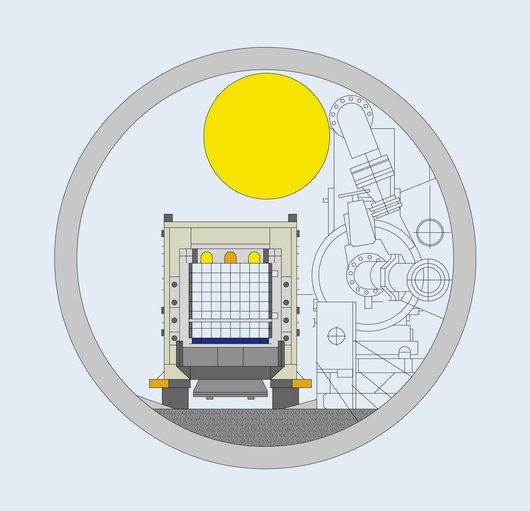
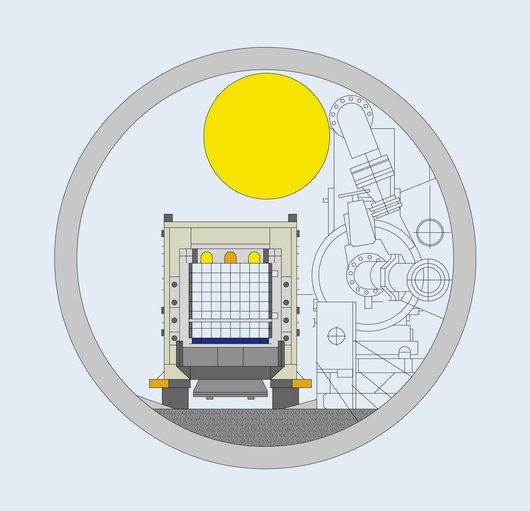
Die MSV können pro Ladung alle Tübbingsegmente, die für einen Vortrieb benötigt werden, transportieren. Permanent ist eine Kabine für bis zu vier Personen installiert, für den Schichtwechsel kann eine zusätzliche Kabine für bis zu zwölf Personen auf der Ladefläche befestigt werden. Eine zusätzliche Ladefläche ist über den Rädern des Fahrzeugs vorgesehen. Die MSV sind 17,15 m lang, 1,26 m breit und (inkl. Beladung) 1,90 m hoch. Beladen kann eine Geschwindigkeit von 15 km/h gefahren werden.
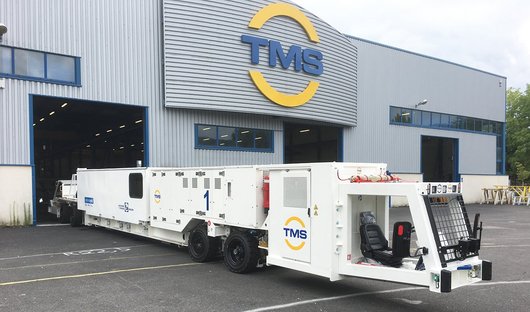
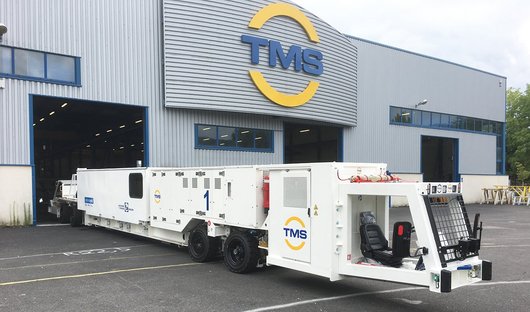
Arbeitssicherheit & Gesundheit
Aufgrund der nicht vorhandenen Zwischenschächte war die Planung eines Sicherheitskonzeptes für die Ausführung der Arbeiten besonders wichtig. Neben den üblichen Gesundheitsprüfungen und Schulungen für das eingesetzte Personal kommt u.a. auch Folgendes zum Einsatz:
- Ein an der Oberfläche installiertes
- Notfall-Kontrollzentrum, das wichtige Parameter auf der TBM, wie z.B. Branderkennung, Luftqualität und Gasauftreten überwacht. Darüber hinaus entsteht hier das Kontrollzentrum für die Kommunikation zwischen Maschine und Oberfläche.
- Eine Schutzkammer auf der Maschine, die den im Tunnel befindlichen Personen im Falle einer nicht möglichen Evakuierung Schutz für 24 Stunden bietet.
- Selbstretter, die im Falle eines Rauch-, Feuer- oder Gasereignisses die Personen im Tunnel mit Sauerstoff versorgen sind auf der Maschine im Tunnel und auf dem MSV installiert.
- Feuermelde- und Feuerunterdrückungssysteme sind in Bereichen mit erhöhtem Brandrisiko montiert.
- Ein Wasserschott am Ende des Tunnels sowie Rauchschotts, die den Tunnel in fünf Abschnitte unterteilen.
Des Weiteren wurde zur besseren Ausbildung der Tunnelmannschaft für Drucklufteinstiege ins Schneidrad, Werkzeugwechsel oder Ringbau eine Trainingseinheit, der sogenannte Tunnel Mock-up, direkt auf der Baustelle aufgebaut. Der Tunnel Mock-Up besteht aus einer Tunnelröhre mit 21 Ringen und einer TBM-Einheit, die sich u. a. aus einer Arbeitskammer, einer Druckluftschleuse und Schneidwerkzeugen zusammensetzt.
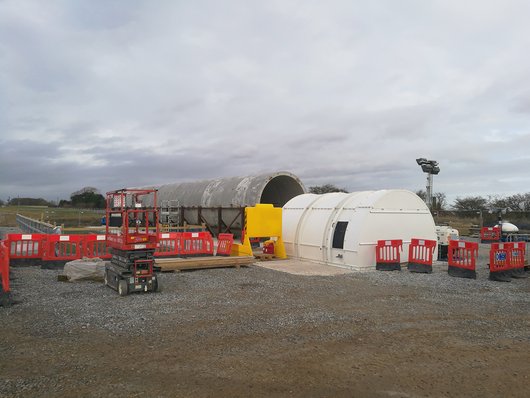
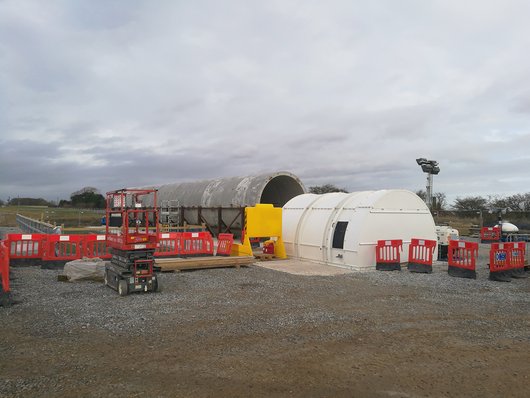
Pipeline-Arbeiten
Die 1,05 m (42 inch) starke Pipeline wird vom Auftraggeber National Grid beigestellt und in 12 m Einheiten zur Baustelle transportiert. Um die Pipeline vor Korrosionen zu schützen, ist sie beschichtet und zusätzlich betonummantelt.
Die 12 m-Rohre werden per LKW an die Baustelle geliefert. Es kommen zwei verschiedene Rohr-Typen zum Einsatz: CWC-Rohre (Concrete Weight Coated) mit einem Rohrgewicht von 16 t für die Installation innerhalb des Tunnels und mit Schmelzkleber beschichtete Rohre (FBE) mit einem Gewicht von 5,9 t für Installationen außerhalb des Tunnels. Auf der Baustelle werden die Einheiten an der Oberfläche zu zwei 624 m und sechs 612 m langen Rohrsträngen verschweißt. Die Rohre werden halbautomatisch geschweißt, was eine Toleranz von 0,5° ermöglicht. Alle Schweißnähte werden durch eine automatische Ultraschallprüfung unterzogen. Für den Einbau des Rohrstrangs in den Tunnel, wird der Tunnel komplett mit Wasser gefüllt.
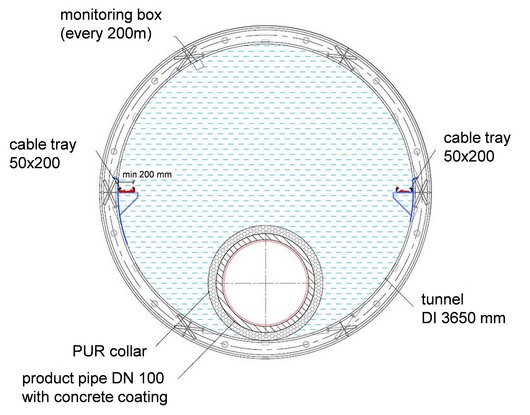
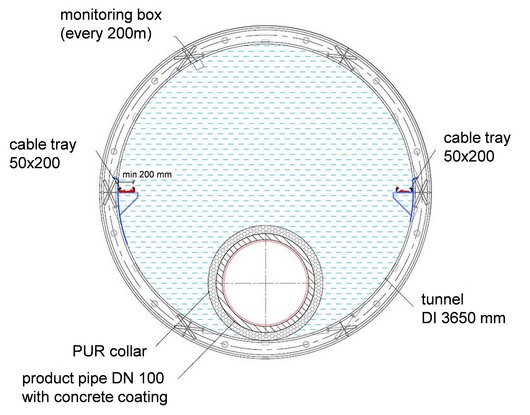
Die gesamte benötigte Wassermenge beträgt ca. 51.000 m³. Das Wasser wird aus dem Fluss Humber entnommen, vorbehandelt und anschließend in den Tunnel gepumpt. An der Startrampe werden zwei Pipe Thruster mit einer Kapazität von jeweils 500 t installiert, von denen jedoch nur einer erforderlich ist, um das Rohr in den Tunnel zu schieben. Der Zweite steht bereit, um mögliche Verzögerungen während der Installation zu minimieren. Sobald der erste Rohrstrang in den Tunnel eingeschoben ist, wird dieser mit dem zweiten Strang verschweißt. Insgesamt sind sieben dieser Verbindungsschweißungen erforderlich, bevor die Pipeline fertiggestellt ist.
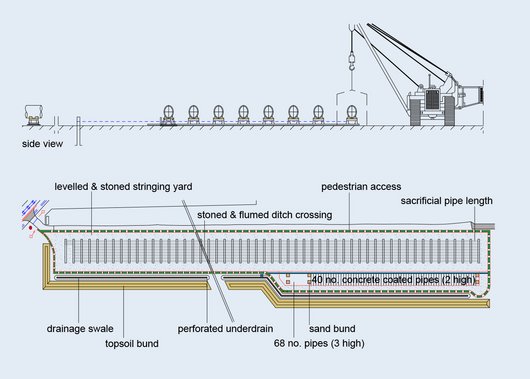
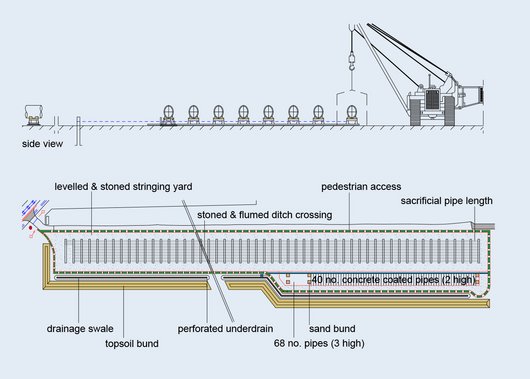
Nachdem die gesamte Pipeline eingezogen ist, erfolgen eine Druckprobe und der Test des installierten Korrosions-Schutzsystems. Nach der Abnahme werden die Zugangsschächte aufgegeben.
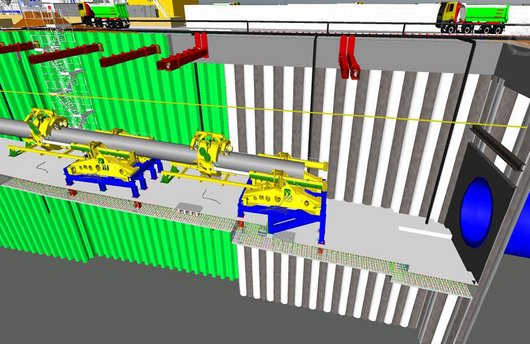
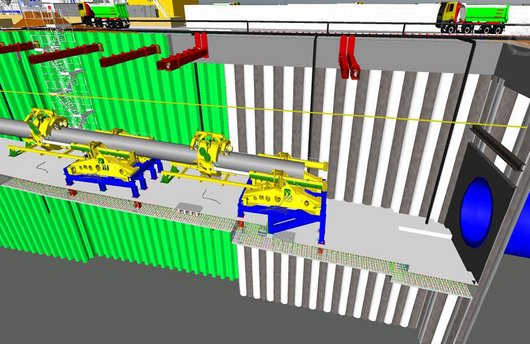
Technische Daten
-
MaschinentypHydroschild-TBM
-
AuftragserteilungApril 2016
-
VortriebsbeginnApril 2018
-
VortriebsendeSommer 2019
Fazit
Das Humber Crossing – Feeder 9 Replacement Projekt ist das erste Projekt der PORR im Vereinigten Königreich. Die erhöhten Anforderungen an die Projektausführung, bedingt durch Arbeiten in direkter Nachbarschaft zu gasführenden Einrichtungen, Arbeiten in hochwassergefährdetem Küstengebiet, ausgewiesenen Naturschutzgebieten und die hohen britischen Arbeitssicherheitsstandards stellen das Team vor besondere und spannende Herausforderungen. Nach erfolgreichem Abschluss aller Arbeiten wird die PORR in Zusammenarbeit mit dem gesamten Joint Venture und National Grid einen neuen Weltrekord erreicht haben. Die neu verlegte Pipeline wird die längste, in einem Stück in einen Tunnel eingeschobene Gas-Pipeline der Welt sein.