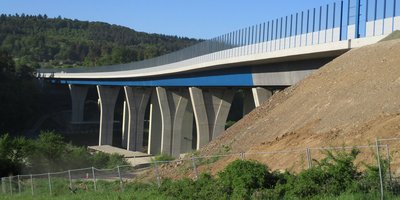
motorway bridge
and its new construction
Marbach valley bridge
At the edge of Dillenburg, PORR Deutschland GmbH is constructing a 388m long bridge over the valley which will completely replace the existing bridge.
The bridge leads above the Marbach, passing country and service roads. Challenges are the dismantling of the existing structure, the geometry of the composite steel superstructure and the logistics of the construction site in a restricted construction area.
-
EmployerHessen Mobil Straßen- und Verkehrsmanagement
-
ContractorPORR Deutschland GmbH
-
Project typeInfrastructure, Bridge building
-
Project scopeDemolition and new construction of the Marbach valley bridge, BAB A 45
-
Order volumeEUR 36.4 million
-
Construction start09/2014
-
Construction end06/2020
General
The A45 national motorway is an important north-south link, connecting the Greater Dortmund and Greater Frankfurt areas. Following the sharp increase in traffic volume over recent years, the entire four-lane section is being widened into six lanes. Calculations made back in 2008 on the two partial structures that make up the old bridge indicated that the structure – built in 1967 – was already exhibiting significant deficiencies in terms of load-bearing capacity and was no longer suited to the current traffic loads – and thus certainly not for future requirements. Due to the poor state of the structure, immediate measures were taken with an emergency overhaul of the Frankfurt-bound side in 2011. In 2014, PORR began demolition work and
construction of the new bridge. Once all traffic had been transferred to the existing Frankfurt-bound partial structure, the Dortmound-bound bridge was demolished and replaced by the new partial structure. On completion of the new structure, traffic was transferred over to it, so that the old bridge could be demolished and the second new structure created. Once this is complete and a temporary carriageway alteration on the northern side of the bridge has been reverted, traffic can begin circulating using the planned lanes. The contract also includes manufacture of a rainwater retention basin, the corresponding drainage channels, noise barriers, the access roads and the A45 road construction.
A challenging and complex bridge construction on a cramped construction site - we have the know-how and the experience.
The project
The new valley bridge is being constructed as a 7-span structure comprising two parallel partial structures. Load transfer along five of the eight axes in the substructure takes place via large bored piles with lengths up to 16m, which form deep foundations. The other three axes have reinforced concrete surface foundations manufactured directly on the rock face. Each superstructure is supported by six columns and two abutments. The individual supporting widths of the composite steel cross-sections range from 45.7m to 68m. The superstructure cross-section consists of two single-celled steel box girders for each direction and loosely reinforced roadway slabs.
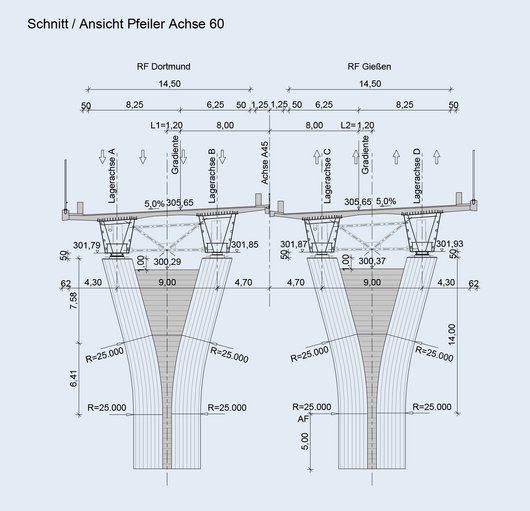
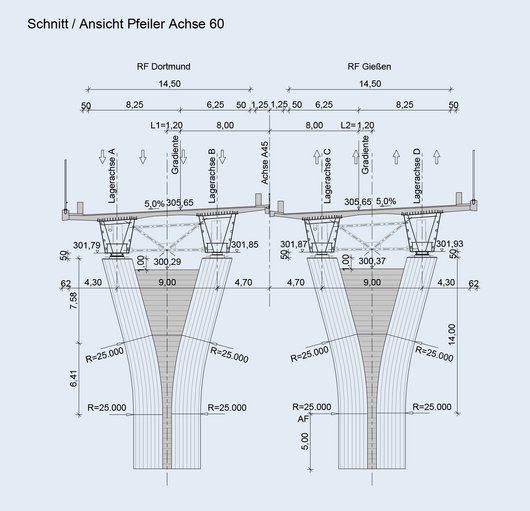
Demolition of the existing structure
A detailed demolition plan for the existing structure was specified by the Hessen Mobil higher regional authority. Among other things, it involved demolishing the superstructure on a section by section basis using a demolition scaffold. The individual demolition sections were 45m long and were detached from the remaining superstructure with a separating cut. In order to ensure that the particular section scheduled for demolition had an even load distribution on the scaffold, a costly hydraulic system with 38 jacks with adjustable collars and three hydraulic pumps was installed in the scaffold below the demolition area.
The system had to be adjusted several times a day to the current demolition circumstances. Demolition was carried out using excavators, starting from the roadway slabs. Lateral formwork around the demolition prevented demolition debris from falling below the bridge. The demolition scaffold was divided at the centre after demolition of each section, and repositioned longitudinally in the next span. This allowed the old prestressed concrete superstructure to be demolished precisely opposite the ongoing new construction.
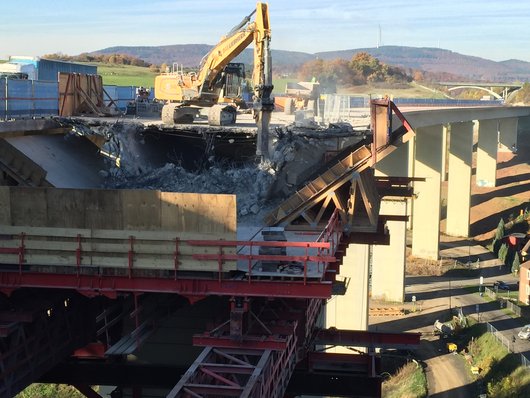
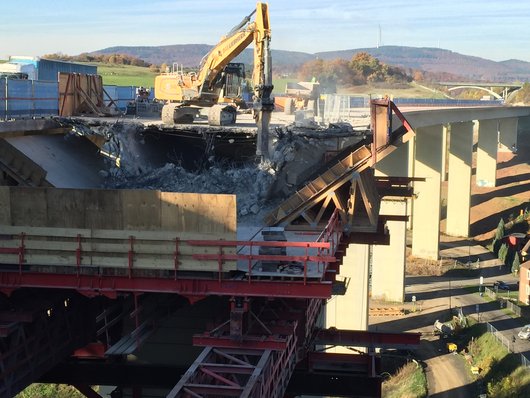
Foundation and substructure
The foundation for the new structure was laid on the rock face – partly as surface foundation and partly as deep foundations using large drilled piles with a diameter of 150cm. Due to varying local underground conditions, the solid rock was reached at different elevations; it furthermore consists of different types of rock, and in some places there are large fissures or hollow areas. These conditions made manufacture of the pile foundation correspondingly challenging. The new bridge columns have a complete cross-section of around 14.5m², with heights ranging from 15.5m to 25m including the column heads. They were concreted in individual sections 5m high. The column heads become significantly wider over their 14m height, with upper edges around 11.5m wide: almost twice as wide as the column shafts – making manufacture of the column heads accordingly expensive. The abutments have a volume of up to 600m³ and the casting level for the first section up to the bridge seat varies up to 9.50m.
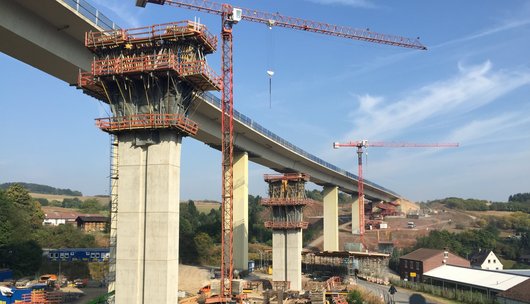
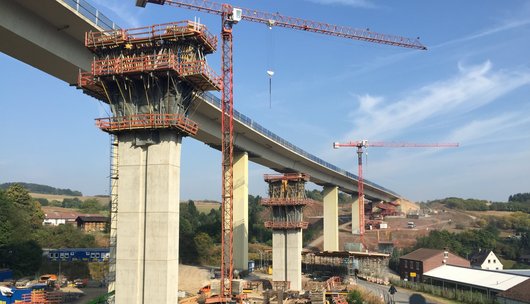
Composite steel superstructure
Behind each abutment, the steel construction was assembled from individual components of some 30m in length and up to 100t, welded and shunted in individual sections. This took place in production facilities around 90m long and 5m deep. The components were then transported the 400km from the facility to the construction site during night-times.
The adjoining steel box girders were linked in the production facility using transverse bracing, installed at distances of 20m as per the plans. Assembly and shifting took place consecutively for both the southbound and northbound routes. The resulting central section was then aligned and connected directly in its final position. The geometry of the superstructure itself posed a significant challenge: it has a gradient of around 2.5% in the northern longitudinal direction, and consists of a curve with a 700m radius, followed by a gentle curve in the other direction, while the steel construction has a straight portion in this second section. As a result, the composite panel ceases to be parallel to the steel construction from the centre of the bridge, which meant the cantilever arm lengths had to be altered, as well as representing a significant challenge when manufacturing the roadway slabs. As a consequence, the formwork construction for the cantilevers on the formwork carriage had to be rebuilt several times – particularly since the carriageway was manufactured using a back-and-forth process, meaning it was necessary to keep travelling backwards as well as forwards.
A related issue was the restricted space conditions for the adjacent partial structure – special solutions had to be found for the continuity reinforcement on the bridge caps, while the formwork carriage required skilled handling. Finding a solution for the central part of the formwork carriage was equally challenging. Due to the restricted space conditions between the upper edge of the transverse bracing and the lower edge of the roadway – the distance is only 60cm to 80cm – the formwork scaffold had to be reconstructed for each run of the carriage. Despite all these issues, three 29m sections of the roadway were already complete by the time the gap was closed on the steel construction at the beginning of June 2017.
A further particularity of the structure is that there is a change in the gradient on the bridge, so that the lateral gradient begins at 5% in the eastern direction and becomes 3.7% in the western direction. The structural solution to this was to modify the steel structure, adapting the heights of the box girders. The initially high box girders on one side of the bridge become lower girders by the end of the bridge, and what is initially the lowest box girder is the highest by the end. The heights of the steel construction thus vary from around 2.90m to 3.60m.
Completion of partial structure 1
The remaining corrosion protection measures that had to be implemented in November 2017 due to the weather were carried out from April 2018. The bridge sealing was then manufactured and the structure completed with protective facilities including a noise protection wall, thereby reaching the next project milestone. Following completion of the first partial structure
and the associated construction of the A45 in May 2018, traffic was redirected, so that PORR will be able to begin demolition of the second partial structure in July 2018, alongside construction of the new bridge structure. The demolition scaffold for the second partial structure is already in position and just needs to be finalised.
Technical data
-
Project length1.450m
-
Bridge deck area14.160m²
-
Construction steel4.600t
-
Concrete incorporated22.500m³
-
Reinforcement steel4.040t
-
Large drilled piles 150cm950m
-
Sheet piling construction1.400m²
-
Shotcrete surfaces1.300m²
-
Concrete demolition12.400m³
Summary
Despite the challenging, costly construction process and restricted construction space, the first partial structure has been manufactured by PORR to meet the contract. The disruptions, largely caused by changes and additions to the project scope, were compensated for by continual operation
since April 2017. This achievement was made possible by the hard work and expertise contributed by all project participants. Building on the experiences from the first section, PORR will be able to construct the second partial structure rapidly and professionally when work begins in July 2018.