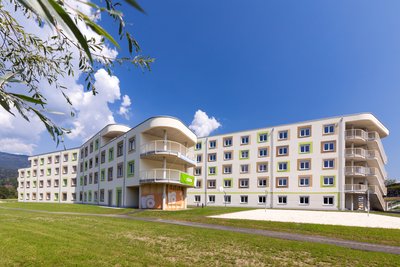
in former mining city
Living Campus Leoben
In a construction period of only 17 months, PORR built a multi-storey dormitory with student and lecturer apartments, guest rooms, start-up offices and a café.
Engaging PORR Design & Engineering GmbH at an early stage enabled efficient use of prefabricated components, while intensive planning turned the Living Campus in Leoben, Austria, into a showcase project for sustainability in practice.
-
EmployerRottenmanner Bau- und Siedlungsgenossenschaft
-
ContractorPORR Bau GmbH
-
Order typeGeneralunternehmer
-
Project scopeConstruction of a 4-5 storey residential building
-
Order volume10.13 million euros
-
Construction start03/2017
-
Construction end07/2018
Background
As recently as just two years ago, Leoben’s Brandlwiese – famous for its Autumn festival – was neighboured by a yawning expanse of emptiness. Today, that expanse is the site of a modern building providing accommodation for 280 people; not only does the structure boast a DGNB Gold Certificate, it is also an architectural highlight of this former mining city. The structure is divided into two curved axes. The shorter of the two, which stands at a height of four storeys, faces the Mur River to the west.The main, eastern section of the building is five storeys tall. The two sections are joined by a spacious glazed atrium. Recesses in the western section have created attractive terrace areas on the flat roofs. The concept for this residential building dates back to 2015. Following two years of intensive planning and the sale of the project to the Rottenmanner Bau- und Siedlungsgenossenschaft when it was ready for construction, building work began in earnest in March 2017. PORR Bau GmbH, Styria branch acted as the main contractor on the project. The order value was 10.13 million euros.
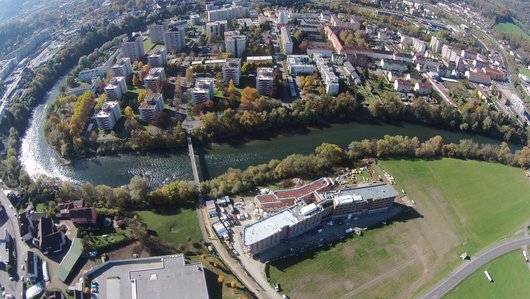
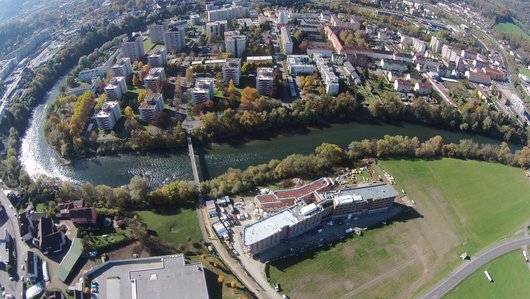
Technical quality and process optimisations go hand-in-hand with sustainability considerations.
Close collaboration with PDE
PORR Design & Engineering GmbH (PDE) was involved in the project from the outset and applied their expertise to optimise the plans significantly. The structural engineering and construction management teams were decisive factors in the successful erection of the structure in its final shape using prefabricated components, brick construction and semi-finished concrete elements. This close collaboration from an early stage made it possible to maximise the use of prefabricated components, thereby minimising the need for time-consuming cast-in-situ concrete. Intensive, in-depth planning was required to achieve the highest international building certificates as demanded by the client. These considerations ranged from energy performance, resource efficiency and the origins of the building components, consumables and laying materials used through to indoor air quality, safety and comfort, as well as the ability to convert the building for alternative uses. The end result of these efforts is DGNB Gold Certification, which was officially awarded as part of the building’s opening ceremony.
Challenging soil conditions
No sooner had construction work begun than soil conditions and uncovered aircraft bombs delayed work to construct the foundations. To ensure that the underlying soil had sufficient load-bearing capacity, dynamic impulse compaction was carried out on the existing subsoil. A total of 320 compaction poles were used in this work, distributed across a grid beneath the flat foundations according to the Structural Engineering department’s calculations. Once the soil had been stabilised, work to construct standard flat foundations could begin. No extensive excavation work was required given the relatively flat terrain; in addition, the building’s single basement floor only extends beneath around one-third of the building.
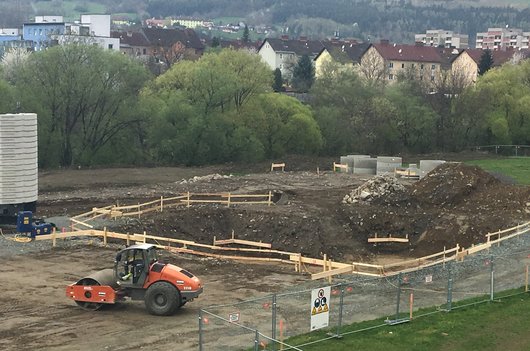
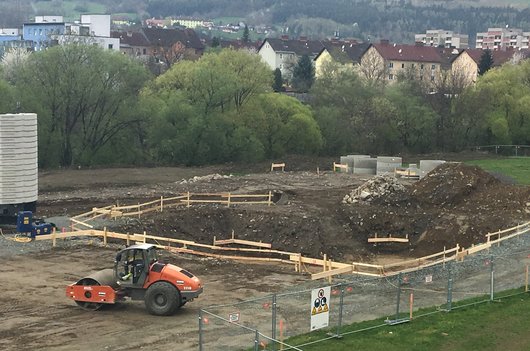
From good to better
In Leoben, PORR based its plans on a structural system that had proven successful in the past and been further optimised by the construction management and planning team for this project. The external walls and the load-bearing walls in the vicinity of the staircases are composed of 25cm vertical coring bricks. As the plans were agreed at an early stage, only a small number of round reinforced concrete columns were required as load-bearing elements in the large, wing-shaped sections of the building. As a result, all structural slabs were realised joist-free using special punching shear reinforcements. .
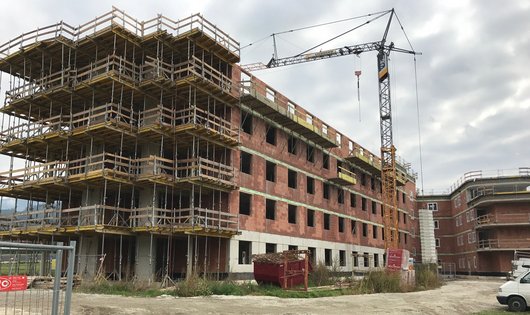
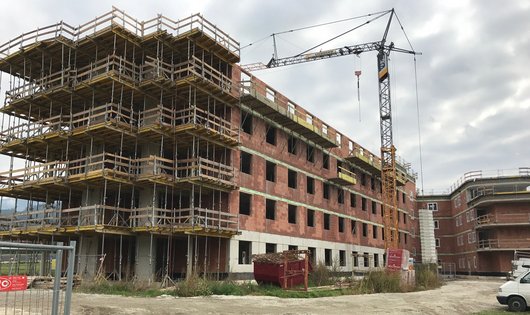
The structural slabs are made up of loosely reinforced part-prefabricated concrete elements, which were secured to the load-bearing external walls and inset reinforced concrete columns using cast-in-situ concrete reinforcements for the full slab thickness in the punching shear area. The reinforced concrete columns were integrated in drywalls during completion work, thereby hiding them from view. These design variants had a thoroughly positive impact on both the construction period and the final project costs. To ensure that the high proportion of prefabricated parts could be handled properly on the construction site, PORR had to be integrated in planning for the building at an early stage to adapt its shape and structure to meet these requirements. In addition, construction management had to ensure smooth coordination of planning, approval, supply and delivery of concrete components.
Effective organisation
At its longest point, the building is 115m in length. To compensate for this length, three structural expansion joints were integrated in the building’s structure, dividing the overall building into four construction stages. Both the construction schedule and the site facilities – and therefore, in effect, the entire construction process – proceeded according to these building sections. Construction work was first completed in the western section, before the focus shifted from the southern section to the central area and, finally, to the northern section. All subsections followed the same sequence, meaning that the northern section was the final construction stage to be completed. As the building site was organised in such a well-considered manner, only one rail-mounted fast-erecting crane was required during the entire construction period – despite the building’s considerable size.
Eye-catching design
The five-storey section of the building was finished with a traditional flat roof; the four-storey section, meanwhile, features an extensive green roof, ensuring that the ideal of sustainability is even reflected on the roof. The building envelope comprises an external wall insulation system. The architect included colourful accents and window surroundings in the design for the building’s façade. This lively interplay of colours is another aspect that separates the development from other buildings in Leoben and certainly catches the eye, even from a distance.
As the living spaces follow a consistent layout in terms of their dimensions and measurements, work on the building’s interior was carried out both quickly and continuously in individual stages. All other subsections coordinated with drywall installation seamlessly and without significant delays.
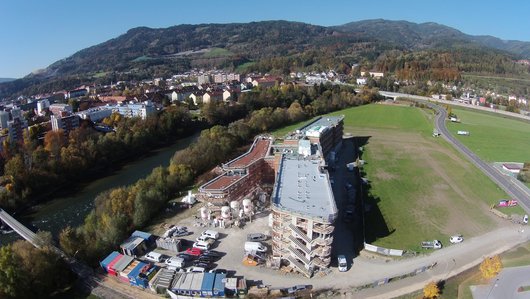
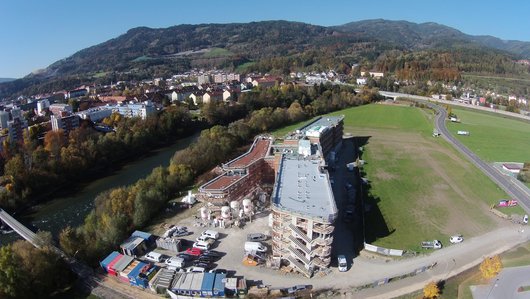
PORR – Putting sustainability into practice
This project showed once again the importance of the topic of sustainability for the construction industry. The support from the PDE Sustainability department – from the start of the project through to handover of the finished building – ensured a high degree not only of resource efficiency and energy performance but also of comfort for the building’s occupants and economic viability throughout the building’s life cycle.
As the general contractor, PORR was required to place particular importance on technical quality and process quality in the execution of the project. In particular in collaborations with subcontractors, it was necessary both to specify the use of appropriate materials and products and to carefully examine and approve the materials and products used to execute the project. PORR’s ability to rely on support from PDE throughout the entire construction period greatly facilitated this work. PDE served as a consultant in the project’s infancy, in the planning stages and throughout the project as a whole. Furthermore, PDE conducted a life cycle assessment of the construction and usage phase and carried out all building physics examinations, tests and measurements required for the Austrian Sustainable Building Council (ÖGNI) to issue certification. This work included, for instance, daylight simulations, pollutant measurements and an on-site blower door test. This work all had to be scheduled and the technical aspects planned during work to construct the building.
Gold Certificate
Obtaining DGNB Gold Certification not only called for clear thinking in the planning phase but also required all parties to consciously work to ensure sustainable construction work throughout the project. Intensive collaboration between the planning office and specialists from all fields involved in the project – as well as the engagement of one or two expert committees – made this sustainable vision a reality with a minimum of fuss. All PORRians involved in the building’s construction can now look back on an exciting and ultimately wholly successful project.
Technical data
-
Gross floor area9.473m²
-
Built-up area1.993m²
-
Foundation typeFlat foundations
-
Concrete used3.969m³
-
Vertical coring brickwork4.950m²
-
Number of apartments164 single rooms, 58 double rooms
-
Number of offices14
-
Car parking spaces58
-
Bicycle parking spaces150
-
CertificationDGNB-Zertifizierungsstufe Gold