![[Translate to Englisch:] Das Tragwerk des Schmiedtobelviadukts wurde im Rahmen der Sanierung von der PORR verstärkt und verbreitert. Quelle: PORR Das Tragwerk des Schmiedtobelviadukts wurde im Rahmen der Sanierung von der PORR verstärkt und verbreitert.](/fileadmin/_processed_/b/9/csm_San_Schmiedtobelviadukt_Foto_01_0770f6047c.jpg)
Schmiedtobel viaduct
PORR rehabilitated the Arlberg railway’s 130-year-old Schmiedtobel viaduct under extreme time pressure and highly cramped conditions.
In addition to reinforcing and widening the load-bearing frame, the rehabilitation of the viaduct also comprised the restoration of 4,000m² of masonry and the construction of a 450m-long access road. The frame had to be rehabilitated within just two weeks.
-
EmployerÖBB Infrastruktur AG
-
ContractorPORR Bau GmbH . Niederlassung Tirol
-
Order typeBaumeisterleistungen
-
Project typeCivil engineering/infrastructure . Bridge construction
-
Project scopeStructural reinforcement and widening of a 130m-long railway viaduct, rehabilitation of 4,000m² of natural stone masonry and construction of a 450m-long access road
-
Order volume2,6 million euros
-
Construction start03/2018
-
Construction end10/2018
Background
Built between 1880 and 1884 as an intrepid mountain railway line, the Arlberg railway connects Tyrol with Vorarlberg. The 19 viaducts in particular are impressive examples of engineering structures of the time. The highest and, on the Vorarlberg side, longest viaduct is the Schmiedtobel viaduct between the Dalaas and Hintergasse railway stations. This bridge structure is 130m long and spans the rocky Schmiedtobel ravine. The tallest pier has a height of approximately 50m. Due to the increase in rail traffic, ÖBB Infrastruktur AG decided to carry out a general rehabilitation of the 130-year-old structure to improve drainage and overall structural stability.
The Tyrol branch of PORR Bau GmbH secured the contract for resurfacing the railway tracks and rehabilitating the Schmiedtobel viaduct. The works all had to be carried out between March and October 2018. Since the Arlberg railway is critical for rail traffic within Austria and throughout Europe, the actual frame had to rehabilitated within a strict two-week track closure period.
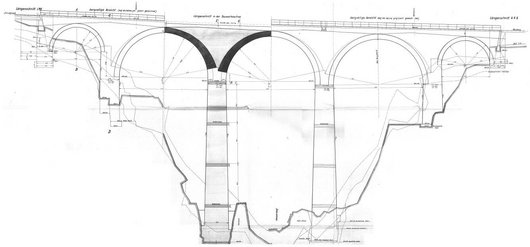
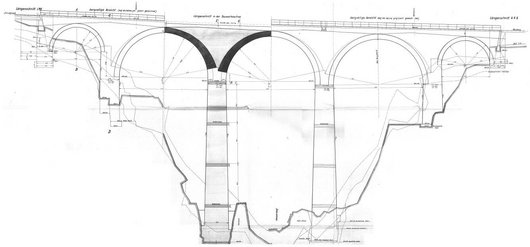
TO REACH THE CONSTRUCTION SITE, WE HAD TO CLEAR, RESURFACE AND EXTEND AN APPROXIMATELY 550M-LONG FORESTRY TRAIL.
Extensive preparatory works in difficult terrain
Since the building site was only accessible by rail or on foot, the first step was to build a construction site access road. An approximately 550m long forestry trail had to be cleared, resurfaced and extended up to a plateau south of the railway on the east side of the viaduct. A storage compound and turning area was built at the end of the access road. Both the forestry trail and the compound will be made available for conservation measures after the rehabilitation of the ÖBB Schmiedtobel viaduct.
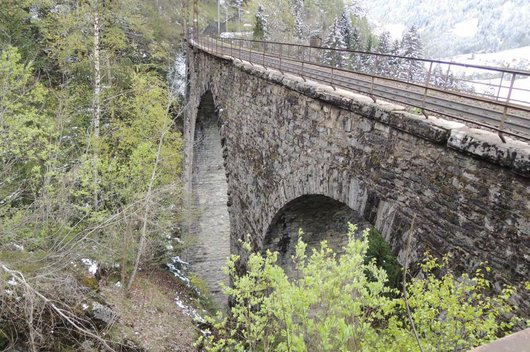
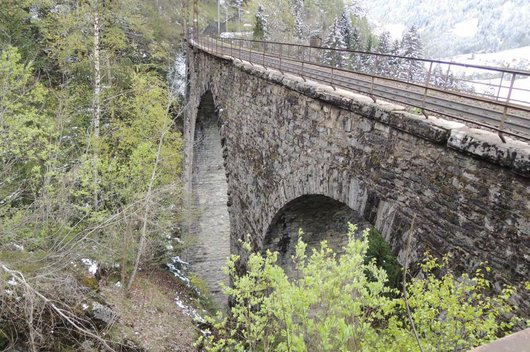
For reasons of construction logistics, the prefabricated edge-beam parts were produced as early as March 2018, transported by rail during a short interim track closure period, and stored on the west side of the viaduct prior to installation. As the renovation work on the vault and viaduct masonry could not be carried out within the track closure period, scaffolding was erected around the entire bridge structure from June to July 2018. The extremely steep terrain leading up to the pier bases presented a major challenge for the scaffolders. A supply ropeway was slung across the ravine to transport the scaffolding material, which weighed 320t. A bracket scaffold with a railing was also attached to the existing wall at track level that would subsequently serve as a demolition, work and protection platform.
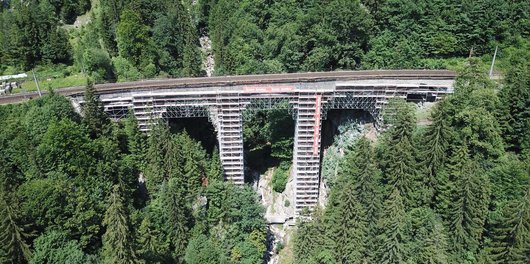
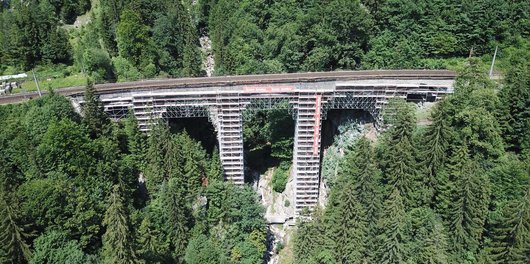
A tight time slot for rehabilitating the frame
The viaduct consists of three larger arches with a 26.6m span in the middle and two smaller arches on either side, in front of the abutments. The approximately 4.5-metre-wide vaulted arches have been bricked up with roughly 80cm-thick side walls. Previously, the gap had been filled with bulk material and, in some places, tamped concrete. A drainage level runs through the roof profiles along the viaduct. The water is drained from the lowest point at the centre of each arch.
WE COMPLETED THE STRUCTURAL RESTORATION WITHIN ONLY TWO WEEKS.
After ÖBB had completed preliminary works, including removing the overhead line and dismantling the track grid, PORR was able to begin renovating the supporting frame. The first step involved cutting the vault walls horizontally to align with the bottom level of the new frame. This was followed by removing the railing including the cable duct, clearing the track ballast, and dismantling the side walls and the vault filling.
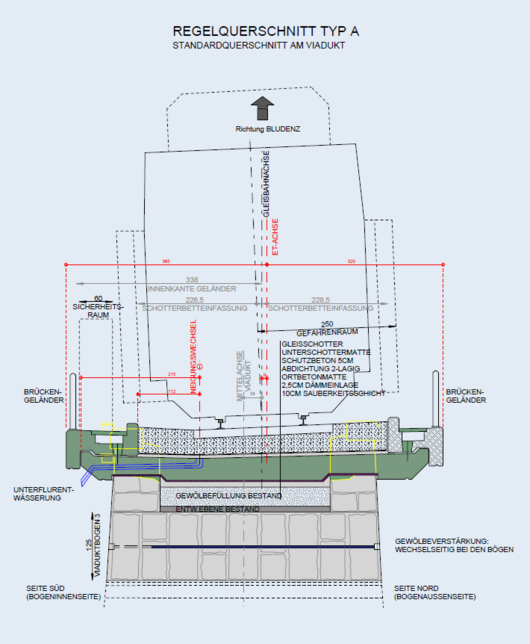
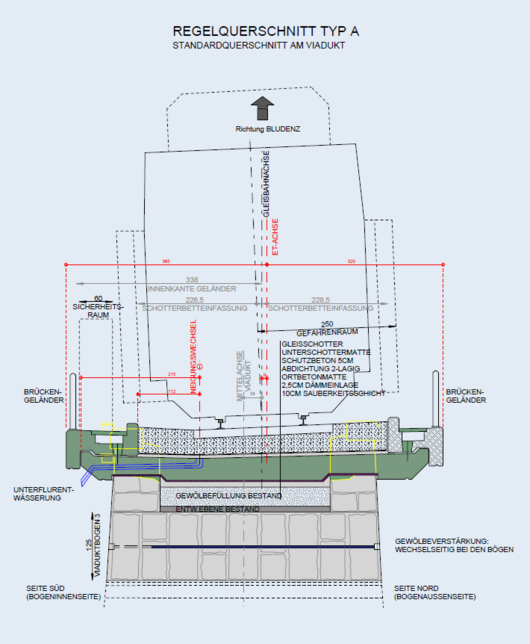
After creating the blinding layer on the vault filling and laying the 2.5cm-thick elastomeric bearings, the team was able to begin work on the frame. For this purpose, the viaduct was reinforced with a 45cm-thick in-situ concrete slab widened to 6.3m in five construction stages. The necessary formwork, reinforcement works and concreting were carried out at staggered three-day intervals. After that, a new two-layer seal was applied for bridge drainage and the prefabricated edge beams with integrated cable ducts were installed. After the protective concrete layer had been applied, the sub-ballast mats laid and other finishing works completed, the ballast was laid on the track ballast bed to finalise the resurfacing works. Finally, the tracks were laid and the overhead line restored.
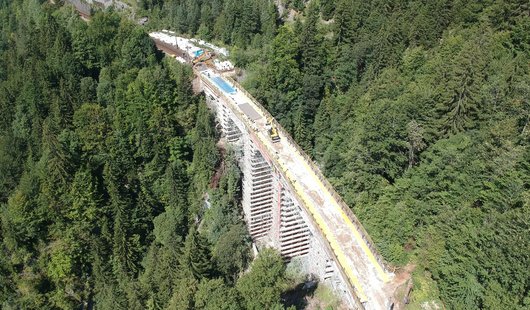
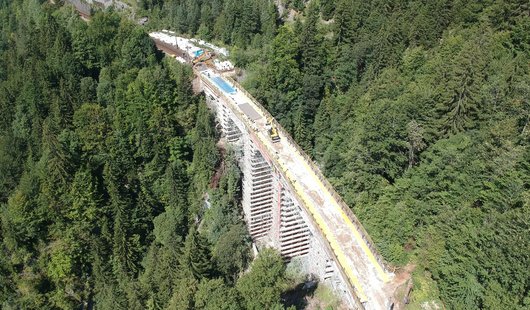
The entire frame had to be rehabilitated within a two-week track closure period in August. The extremely tight construction schedule was planned down to the hour and presented enormous logistical and technical challenges for PORR’s site employees. Nevertheless, the Arlberg railway was reopened to traffic on 3 September 2018 as planned.
Technical data
-
Bridge lengths130m
-
Bridge deck area890m²
-
Natural stone masonry removed170m³
-
Sealing890m²
-
Elastomeric bearings680m²
-
Protective concrete layer580m²
-
Reinforced concrete50t
-
Prefabricated edge beam113 pcs.
-
Bridge railing255m
-
High-pressure water jetting/sand blasting natural stone masonry4.000m²
-
Rehab. natural stone masonry3.000m²
-
Niro anchors dm 20mm520m
-
New access road450m
-
Aggregate base course1.700m³
Rehabilitating the masonry
Before the track could be resurfaced, the PORR specialists had to reinforce the arch vaulting with 126 transverse prestressing elements. To this end, 20mm-diameter stainless steel rods with rolled threads were pushed into 4m long horizontal drill holes which were then filled with cement mortar. Then, all the masonry surfaces were cleaned with high-pressure water jets. Any damaged joint mortars were scraped out by hand and replaced with dry jetcrete for friction-locked closure. To finish off the rehabilitation, the masonry was treated with a sandblasting machine to create a uniform surface.
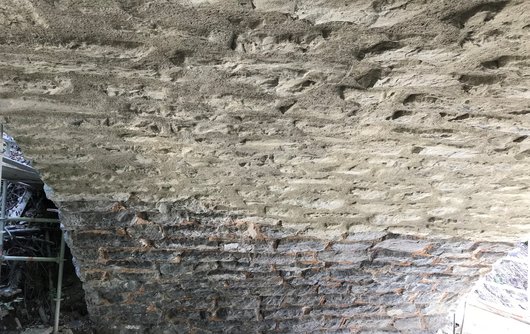
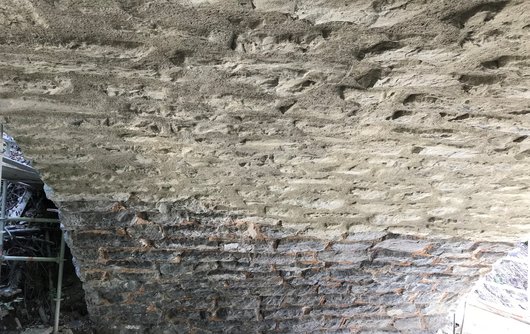
Conclusions
In this project, PORR was able to impressively demonstrate its experience and competence in infrastructure and bridge construction. The greatest challenges to rehabilitating the Schmiedtobel viaduct were the very cramped conditions, the topographical location of the construction site in a ravine and the extremely brief construction period allowed for rehabilitating the frame. Thanks to the excellent cooperation between everyone involved in the project, the works were all completed on schedule in October 2018.