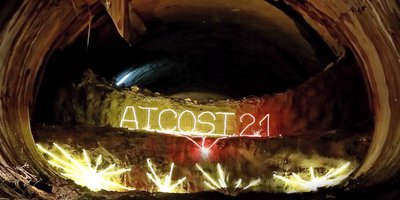
ATCOST21 – Austrian Tunnel Consortium Stuttgart 21
PORR is constructing more than 30km of tunnels and 32 connecting structures for the Stuttgart–Ulm railway project.
Over 530 individuals are working on the project; these include 80 executives at four office locations and more than 450 labourers on site. The demanding conditions sometimes required creative and innovative solutions, some of which have been the subject of patient applications.
-
EmployerDB Netz AG
-
ContractorARGE ATCOST21 PORR Bau GmbH, PORR GmbH & Co. KGaA, G. Hinteregger & Söhne Bauges.m.b.H, Östu-Stettin Hoch- u. Tiefbau GmbH, Swietelsky Tunnelbau GmbH & Co KG
-
Project typeTunnel construction and civil engineering
-
Project scopeConstruction of a 9.4km and 6km twin-tube railway tunnel
-
Order volume720 million euros
-
Construction start08/2011
-
Construction end12/2022
Overview
The Stuttgart-Ulm railway project is currently the largest infrastructure construction site in Germany. The heart of the project is the reorganisation of the Stuttgart railway junction with an underground through station and several access tunnels.
The railway and urban development project known as “Stuttgart 21” dates back to an idea of a Stuttgart based professor of traffic engineering from 1988. The implementation of this idea began in 2011. The contract was awarded to the “Austrian Tunnel Consortium Stuttgart 21” (ATCOST21) under the leadership of PORR. However, the road to placing the order was a rocky one. After successful pre-qualification in spring 2010, three main and 29 secondary offers were worked out within only 11 weeks on the basis of 11 forwarded messages and almost 600 bidder questions and answers. The offer was followed by an eleven-month negotiation process.
On 31 July, Deutsche Bahn awarded ATCOST21 the contract for the first two construction lots of the major project, the 9.4km long twin-tube Filder Tunnel and the nearly 6km long tunnels to Ober- and Untertürkheim. The more than 30km of tunnels and 32 connecting structures have an order volume of more than 720 million euros.
Complex logistics and tunnelling works
In addition to the structural details, a look at the personnel involved reveals the enormous dimensions of the project. In construction and project management alone, around 80 people are working at four office locations. There are also more than 450 labourers, including subcontractors, spread over the project length of more than 30km. For the effective coordination of personnel and for the short information and communication paths required especially in tunnel construction, PORR uses modern communication equipment with Wi-Fi and internal radio links.
In addition to logistics and communication, the actual tunnelling work for the more than 30km of tunnels, half of which are constructed by a tunnelling machine and half by conventional excavator and blast tunnelling, is also challenging. Originally seven starting points were planned. However, an intermediate starting point for the Filder tunnel as well as three access possibilities for the tunnel work were omitted because of delays in the neighbouring construction lots. All work is thus carried out from the remaining three construction sites at the “Filder portal”, the “Emergency access Hauptbahnhof Süd” and the shaft of the “Ulmer Straße intermediate starting point”. This resulted in numerous changes in the construction processes.
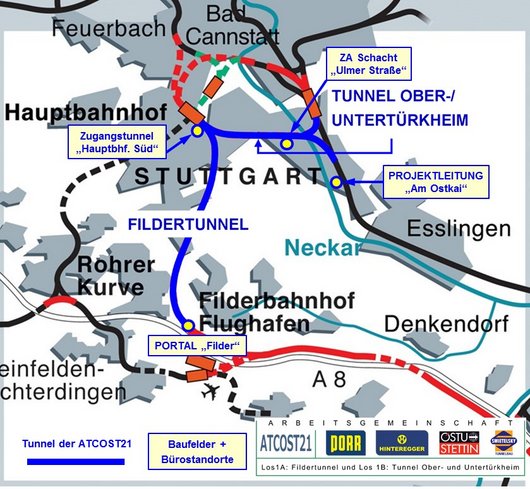
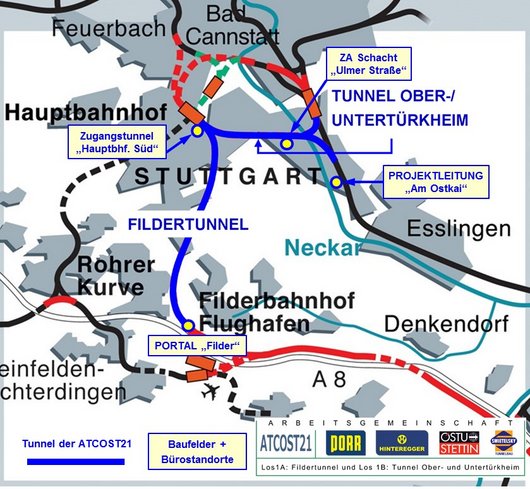
We developed an innovative concept for the annular gap mortar for the lower Filder Tunnel. We have applied for a European patent for this new development.
Filder portal partial construction site
The "Filder portal" is located directly next to the motorway BAB 8 in the immediate vicinity of Stuttgart airport and is the main starting point for the Filder tunnel. From here, two tunnel tubes with a length of over 17km will be constructed in six sections between the Filder level and the 155m underground station below.
For the first two sections in the clay and sandstone formations of the “upper Filder tunnel”, tunnelling is carried out with a tunnel boring machine (TBM) with earth pressure and compressed air components for active working face support. The working face is the place in the tunnel where the tunnelling takes place.
For the two sections in the “lower Filder tunnel”, the TBM in the mountain was converted into an open hard stone shield machine. Because of the swelling capacity of the unleached, anhydrite-bearing gipskeuper, no free water may be used in these sections. Special solutions had to be developed to protect humans and machines from dust and to clean devices and system components. On the initiative and under the leadership of PORR, an innovative concept for the annular gap mortar was developed for the “lower Filder tunnel”: The water in this cement-free mortar is chemically activated and saturated in such a way that practically no swelling processes can be triggered in connection with the anhydrite in the gipskeuper. PORR has applied for a European patent for this new development.
The 1.1km long sections of the “middle Filder tunnel” between the TBM sections are located in geological transition zones. For structural reasons, they were excavated by conventional blasting. The double-shell construction with up to 1m thick reinforced inner shells is currently being carried out here. As in the entire project, the waterproofing work with plastic waterproofing membranes is carried out by the PORR subsidiary IAT.
The ramp concept of the Filder tunnel follows a special proposal by the PORR tunnel builders. The TBM was pulled through the 1.1km long “middle Filder tunnel” and turned underground before the last driving process.
In only three months, the complete tunnelling unit was transferred to the neighbouring tube. The two most spectacular days were those on which the 1,400t, 11m high and wide shield part was rotated through the 12m wide and 13m high turning cavern. These novel shifting and turning processes for a TBM including trailer and logistics were among the project highlights for all participants.
For the middle Filder tunnel, the TBM was pulled 1.1km through the tunnel and turned before the last driving process. This meant that the entire tunnelling unit could be transferred to the neighbouring tube in just three months.
Hauptbahnhof Süd emergency access
The PORR experts found themselves confronted with completely different challenges during the “Hauptbahnhof Süd” emergency access. There, a 240m long access tunnel leads directly into a complex branching structure in which four tunnel tubes lead into two double-track large tunnels directly in front of the underground station. This section, with overlaps of between 20m and 55m, lies directly beneath a densely built-up area and was constructed with leading pier entries. Because of the narrow position of the tubes, the rock between the four tunnels was replaced by 10m high and up to 6m wide reinforced concrete piers.
The last tunnel metres to the future underground station are currently being constructed here. Because of the low tunnel coverage – in some cases, the tunnel is only 8m below the foundations of the surface development – the PORR special civil engineering will use two shafts to carry out preliminary uplift injections on more than 12,000m². A dense grid of injection boreholes between the tunnel and the surface is used to compensate for settlements in the low two-digit millimetre range caused by tunnel excavation.
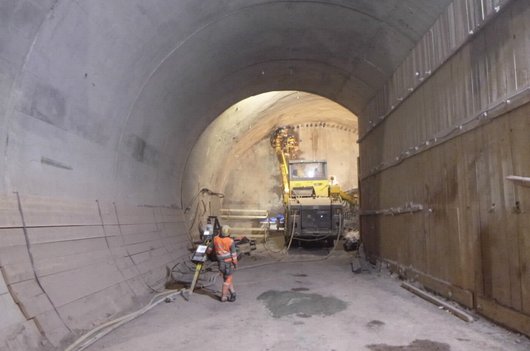
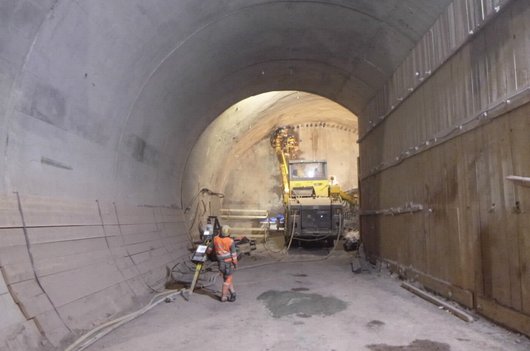
Ulmer Straße intermediate starting point
The underground station in Ober- and Untertürkheim will be connected to the current railway line in the Neckar valley with a new 6km long twin-tube tunnel. The only access to the tunnel is via the Ulmer Straße intermediate starting point A 37m deep shaft with a diameter of 22m and a 110m long access tunnel is the starting point for the six tunnel sections of the two tubes.
The feed rails to Ober- and Untertürkheim are the first four mining crossings of the River Neckar ever. The distances to the river bed in these 200m long sections were only between 8.5m and 18m; the distance between the 10m diameter individual tubes was only 1m in the minimum case. Separate emergency alarm and evacuation plans were therefore in place until the watertight inner shells were installed.
The tunnelling work in Lot 1B was mainly carried out by blasting using a newly developed ignition system, which was able to reduce the blasting vibrations on the surface by up to 35% compared with conventional methods. At present, tunnelling work is still being carried out over a few hundred metres each to the breakthrough points in Ober- and Untertürkheim. In the remaining sections of the tunnel, the construction of the inner shells has begun after extensive waterproofing injections to preserve the groundwater conditions.
Technical Data
-
Cross-cuts32 pc. and 3 technical rooms
-
Reinforcementca. 80,000t
-
Segment rings7,378 pcs.
-
Segment length2m
Conclusion
The Stuttgart-Ulm rail project is also a project of epic proportions for PORR. Around 3 million m³ of rock will be excavated and more than 1.2 million m³ of concrete will be used for the more than 30km of tunnel sections. November 2019 marks the 100th month of construction. Currently, 65% of the total project has been completed.