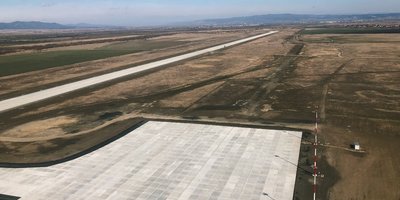
Brasov International Airport
PORR is building a runway, an apron and a comprehensive drainage network for Transylvania’s new airport in Brasov.
Brasov airport is PORR’s fourth airport project in Romania. A short construction period, further reduced by a long winter break, tested the PORR teams to the utmost.
-
EmployerRegierungsbezirk Brasov
-
ContractorPORR Construct S.R.L.
-
ArchitectSearch Corporation S.R.L.
-
Project typeInfrastructure
-
Project scopeConstruction of a taxiway, apron and rainwater drainage system
-
Order volume3.6 million euros
-
Construction start08/2018
-
Construction end04/2019
Overview
Brasov is one of the largest cities in Romania, with over 250,000 residents. The initial plans for building an airport in the Transylvanian city date back to 2012. A runway was tendered and by 2014 it had been built. However, the project then ground to a halt. It remained on hold until 2017, when the city administration launched a call for tenders to construct a taxiway, an apron and a drainage network.
After a careful analysis of the quotes and a suitability test, PORR won the contract for the 3.6 million euro order in July 2018. Work began in August, immediately after the contract was signed.
In order to ensure no further edge protection is required, the asphalt layers have a lateral gradient of 45 degrees.
Apron and taxiway
The apron assures the necessary space for minimum 3 aircrafts category C and has the length of 146m and the width 135m. The structure is rigid, made of poured concrete slabs with the thickness of 41cm where in between longitudinal and transversal joints are cut. The apron and runway are connected by a taxiway 170m long and 23m wide, with two 7.5m shoulders. The taxiway likewise has a rigid structure, consisting of 41cm thick BCR 5 special concrete with tensile strength raised to 5.5N/mm². In order to ensure that no further edge protection is required, the asphalt layers were built with a inclination of 45 degrees.
Suitable soil
The actual work began by removing the topsoil and excavating the ground to a minimum depth of 60cm, ready to create the apron, taxiway and shoulder strips. The foundation layer was stabilised with a hydraulic binder. Work began on the draining system at the same time.
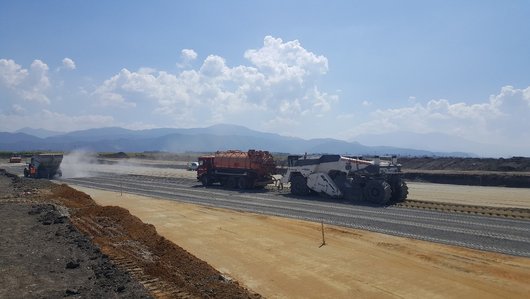
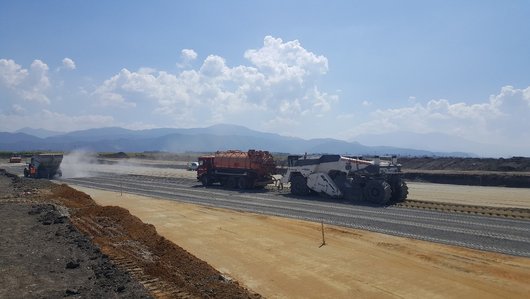
The next stage of the structural work for the apron and taxiway was to create a 40cm thick ballast base course. A further 25cm thick course of stabilised ballast was then laid on top of this. Cable ducts were incorporated into the stabilised ballast, so that the power supply cables for the taxiway lights could be laid in the ground. The shoulder was constructed from a base course consisting of 35cm thick ballast beneath a 25cm course of stabilised ballast.
Solid steel girders were used as formwork for the concrete layer. The project was particularly challenging due to the short construction period, which meant that work had to be done around the clock, including weekends.
Once the platform had been completed, asphalting began on the shoulders. The 10cm thick base course was installed on the stabilised ballast, followed by a 5cm binding layer and finally a 5cm surface layer.
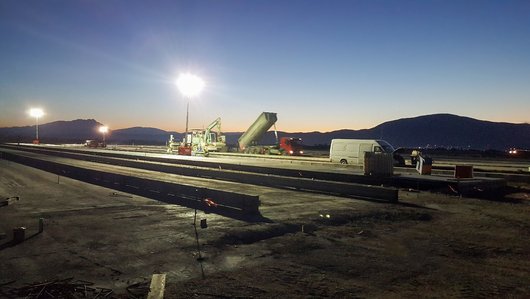
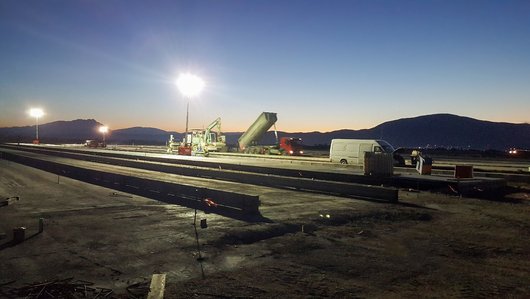
The rainwater drainage system
In just two months, 12km of GRP pipes (DN 500–DN 2000) were manufactured in Turkey and delivered to Romania for the rainwater drainage channels. They were transported to Constanta by two ships and then transferred onto a total of 223 lorries. The first transport had to include every type of pipe, so that work could begin immediately. This was made possible by the collaboration with the excellent delivery contractor APS, who was also responsible for delivering the GRP manholes and concrete manholes.
Work on the draining system began downstream, to ensure that any precipitation during construction could flow away. The platform was built with a 1% incline in both lateral and longitudinal directions so that water would run off. A precast concrete drainage channel was built into the centre of the platform, through which water from the apron could flow directly into the new installed pipes . The storm water drains on the taxiway were installed in the shoulder strips.
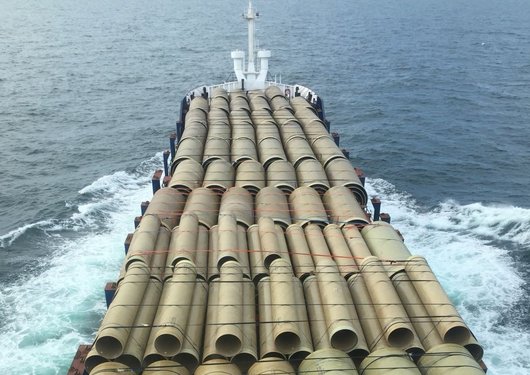
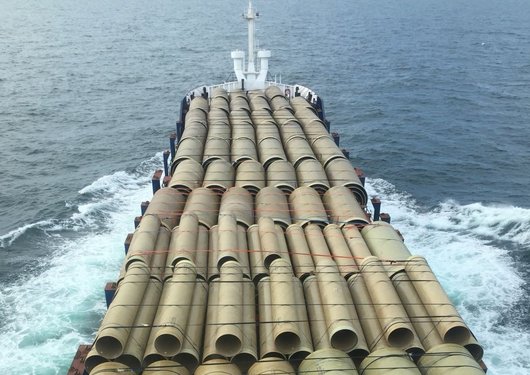
Installing the oil separators was a significant challenge due to the high groundwater level: we hit water after just a metre of excavation and had to continuously pump it away.
Challenge: the oil separators
The water collected in the drainage network is transported through the GRP pipes to two oil separators that remove impurities from the water. Each separator has a capacity of 440l/sec and there is also a bypass with a capacity of 1,200l/sec.
Installing the oil separators was a significant challenge due to the high groundwater level: we hit water after just one metre of excavation and had to pump it away continuously. A 15cm ballast layer was installed after the required depth was reached. A concrete course, also 15cm thick, followed. Once the separators were in place, the filling began with layers of 20cm thickness of soil, reaching the top sections of the separators .
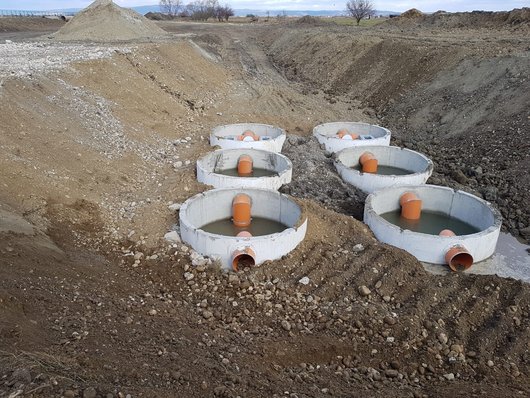
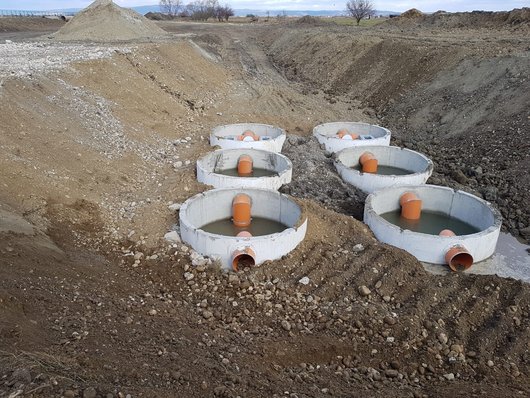
Legacy system rehabilitated
The runway constructed between 2012 and 2014 included water channels and connecting pipes in the shoulder strips. These were covered with a concrete slab with an asphalt course over the top. In order to link them to the new drainage network, the asphalt had to be broken up and the old concrete slabs removed. The new slabs had to be reinforced and the concrete poured in-situ in two stages.
The two branches of the drainage network, the one coming from Alpha and the platform and runs through the separators and the one coming from the runway, are merged together a few meters after the runway ends. The water is directed through DN 2000 GRP pipes and the direction of flow is controlled through special redirection manholes . These manholes are made of concrete and were constructed in-situ.
A discharge chamber is located at the very end of the drainage system. The water is collected here and directed into the River Barsa. To ensure the water can flow into the river, a 27m long concrete surface has been built, followed by a 30m long concrete beam. The river had to be diverted for the concrete to be poured.
Electrics
The final part of the work was to install the lighting system: three 28m light masts. Each mast has four LEDs, a control panel and a lightning conductor. The foundation is 2.4m high and includes all necessary cables and ducts. It is made of class C30/37 reinforced concrete.
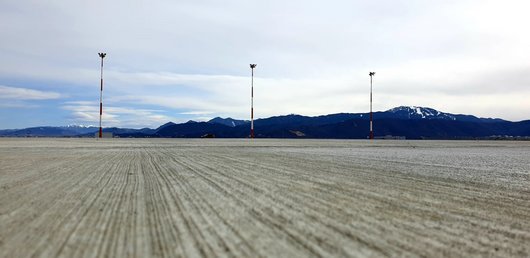
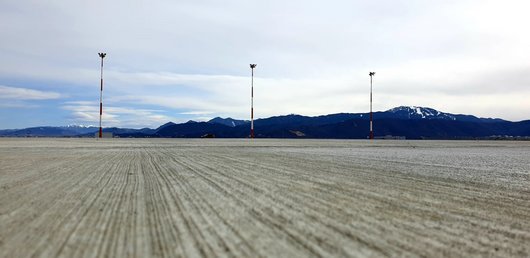
Summary
Despite a lengthy winter pause from 21 November 2018 to 15 March 2019, the work at Brasov airport was completed in just nine months. The client is extremely satisfied with the work and PORR has already been awarded follow-up contracts for the Otopeni and Baneasa airports in Bucharest. These involve constructing and renovating runways and extensive maintenance work.
Technical data
-
Length of drainage channel11,780.10m
-
Excavation for platform and taxiway22,476.00m³
-
BCR5 concrete with special characteristics10,073.70m³
-
Stabilised ballast7,028.00m³
-
Ballast12,278.00m³
-
Soil stabilisation9,223.00m³