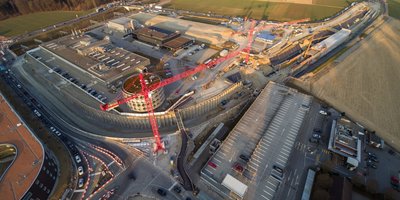
A1 feeder road in Lenzburg
At the busy Neuhof interchange in Lenzburg, PORR SUISSE AG is part of a consortium with KIBAG Bauleistungen AG working to create a new motorway feeder road.
It is hoped that the new feeder road will ensure the Neuhof interchange has sufficient capacity to handle traffic volumes for the next 15 to 20 years. The new feeder road comprises the 362m-long cut-and-cover Neuhof tunnel as well as the Horner and Hero ramps.
-
EmployerKanton Aargau, Departement Bau, Verkehr und Umwelt
-
ContractorARGE KIPO (PORR SUISSE AG, KIBAG Bauleistungen AG)
-
Project typeInfrastructure project / Civil engineering
-
Project scopeCut-and-cover tunnel construction, specialist civil engineering, earthworks, utility line construction, road construction, general civil engineering
-
Order volume26.9 million Swiss francs (25.5 million euros)
-
Construction start03/2018
-
Construction end10/2021
Overview
Lenzburg is a city in the Swiss canton of Aargau. The A1 Lenzburg feeder road north-east of the city connects traffic from the Lenzburg area and the Bünztal valley with the A1 motorway.
As the existing signal-controlled interchange had become unable to cope with traffic volumes, and this problem was forecast to worsen in future, the Department of Civil Engineering of the Canton of Aargau decided to redesign the interchange.
This new design comprises the new Neuhof tunnel, which is under construction with the cut-and-cover method and will provide a connection to the A1 for traffic to and from the Bünztal, and the Hornerfeld connecting road. This connecting road runs between the Horner roundabout to the south and Gexibrücke, an existing bridge, to the north.
A three-phase roadmap to success
The overall project to construct the new motorway feeder road can be divided into three main phases. In the first phase, various changes were made to the road layout to separate traffic for the Neuhof interchange from traffic headed to and from the Bünztal. Traffic to and from Lenzburg continued to pass through the Neuhof interchange, but was relocated to the west to facilitate construction of the tunnel. Meanwhile, traffic to and from the Bünztal was redirected to use the new Hornerfeld connecting road and Horner roundabout. The installation site, the client’s office, and team accommodations were set up during this phase.
In the second phase – the main construction phase – the tunnel and the ramps on either end were constructed. Excavation of the construction pit was completed before concrete work began. Around half of the construction pit was in the area containing anchored bored piles with shotcrete infill. The other half was excavated as an open slope. The concrete work to construct the tunnel began after the excavation of the construction pit was completed.
In the second and third phases, starting in August 2020, traffic flows will be adjusted to the new structures and sections of road. The provisional structures and installation areas will be removed by the end of October 2021.
Efficient construction method
Construction was scheduled so that the first concrete work was to construct the Horner ramp. The sloping nature of the construction pit in this area made it a good site to begin excavation. For logistical reasons, great importance was placed on carrying out excavation work well ahead of the scheduled concrete work.
The concrete work focused on creating the foundations, walls and ceiling. Each of these three elements was assigned its own working group in order to maintain a smooth working cycle in each construction stage. Three casting stages had to be completed simultaneously in places to ensure the project was able to proceed smoothly. In total, it took 65 weeks to complete the 55 casting stages. At the same time, a separate working group set up the tunnel’s three-storey operations centre.
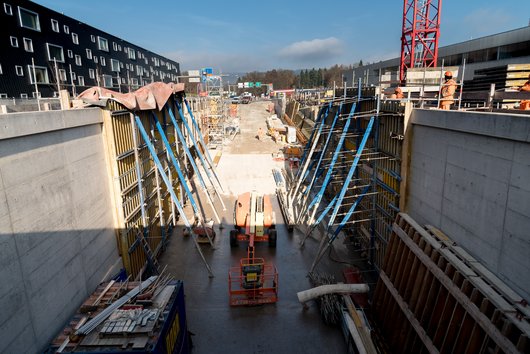
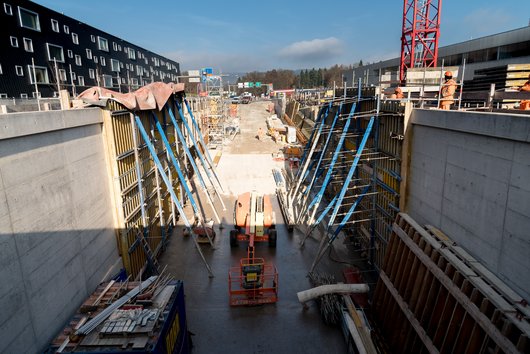
Complex ramps
The new feeder road includes the Horner and Hero ramps at either end of the tunnel. To compensate for the difference in height between the Hero ramp and the road, two separate retaining walls with shallow foundations were constructed where the walls were under 3.4m tall. The strip foundations are 2.6m wide and the walls are 50cm thick. For structural reasons, a single continuous floor slab was used to support sections with walls taller than 3.4m, with thicker walls built in some sections. On the lower side, the floor slab is 1.15m thick; at the higher side, it measures 0.85m thick.
A 10cm recess was created in the walls 1.1m above the road surface to give the option of installing noise control elements.


The formwork carriages were coupled with a secondary carriage to cure the concrete, which ensured high concrete quality.
The Horner ramp essentially uses the same design as the Hero ramp. However, the Horner ramp does not include the option of installing noise control cladding and the strip foundations are 3.05m wide.
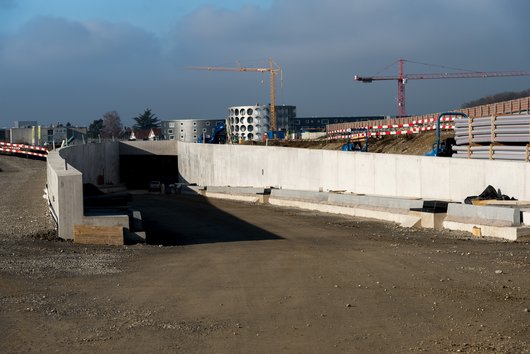
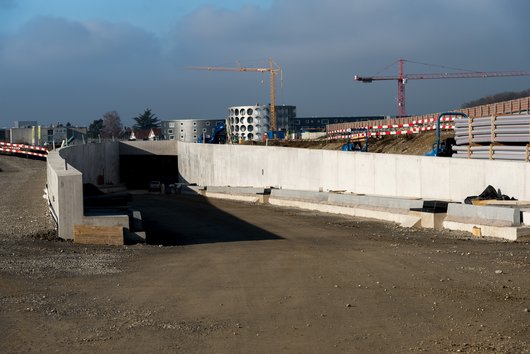
Neuhof tunnel
The Neuhof tunnel is made up of four profiles. Standard profile F makes up the straight section. In this section, the tunnel walls are 75cm thick and the ceiling is 80cm thick. The foundations in this section are 3.45m thick.
Standard profile E is used for the emergency stopping bay opposite the tunnel’s operations centre. The walls are 85cm thick and the ceiling is 90cm thick. The foundation in this section is 3.75m thick. In the area of the oil separator in the operating centre, the foundation is underpinned by the cavity below. In the area where a neighbouring car park meant space was at a premium, the construction pit foundations were streamlined and the tunnel walls were constructed using single-sided formwork for a 25m stretch.
As all ceilings and walls were sealed with a polymer-bitumen membrane, the decision was taken to apply a liquid plastic membrane in the section with single-sided formwork.
A facing concrete casing was constructed against the bored pile wall. The liquid plastic membrane could then be applied to the facing concrete before the tunnel wall was finished with pre-cast concrete. This construction method made it possible to ensure both adequate sealing and take care of the delicate aspects of joining the liquid plastic membrane to the polymer-bitumen membrane.
Standard profile D was used in the transitions to the emergency stopping bay. The walls and ceilings in these sections are 85cm and 90cm thick respectively. The only difference between this profile and standard profile E is the variable foundation width of 3.55m to 3.75m.
Standard profile C is used in curved sections of the tunnel. In these areas, the walls are 85cm thick and the ceilings are 90cm thick. The casting lengths in profiles D, E and F are 15 meters; the curve was constructed using polygonal segments approximately 8m in length.


The ramp walls, which are up to 9m high in places, were concreted in a single stage.
High quality
The client required all visible concrete surfaces to have an underlying horizontal panel structure measuring 2.5m x 0.5m. A large-area formwork system was used to construct the walls and the ceiling formwork was constructed using a hydraulic-drive formwork carriage. The formwork carriage was coupled with a secondary carriage to cure the concrete, which ensured high concrete quality.
The tunnel’s projecting foundations shored up the formwork carriage in standard profile F. For profiles D and E, the formwork carriage and secondary carriage were separated along the centre. This meant a new, additional support had to be created to shore up both carriage sections. It took one week to convert the formwork carriage and secondary carriage. Steel plates were used for the foundations; these were embedded directly onto the levelled ground in the excavated construction pit. In the curved section, the length of the formwork carriages was reduced by half to make sure that they did not damage the walls when moving on to the next casting stage. Shortening the formwork carriage also took one week. Where the ceiling widens, the ceiling formwork was supplemented using conventional techniques.
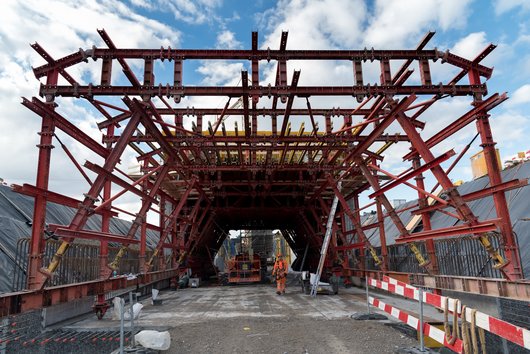
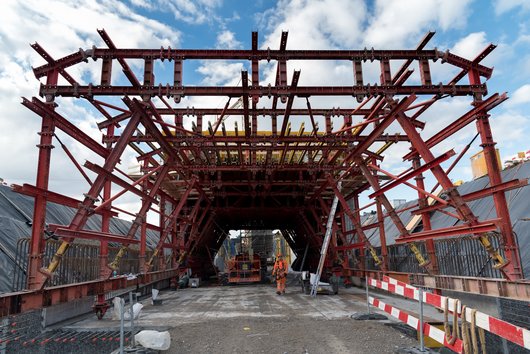
The operations centre
The Neuhof tunnel operations centre measures 7.5m by 25.8m. It is accessible via the emergency stopping bay in the tunnel or via the aboveground access ramp. The new road towards Lenzburg is directly above the operations centre. The impact of the traffic loads was taken into consideration in the design of the operations centre.
Tunnel sealing
The client required an all-over, bonded polymer-bitumen seal for the tunnel. A 35mm thick layer of mastic asphalt was used to protect the sealing in the tunnel ceiling. The wall seal is shielded by a protective mat that simultaneously facilitates drainage.
Conclusion
One particular challenge in this project was adhering to the tight schedule. Converting the formwork carriages for different tunnel sections alone took up a lot of time. However, through efficient use of resources and perfect planning, we were able to achieve the key milestones on time and ensure we delivered the required quality.
Technical data
-
Structural concrete15,100m³
-
Reinforcement2,265t
-
Sealing11,000m²