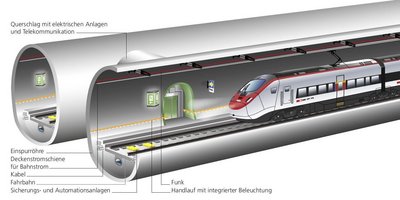
Ceneri Base Tunnel
The Ceneri Base Tunnel is Switzerland’s third largest tunnel construction project and PORR is undertaking the installation of the railway infrastructure.
The Ceneri Base Tunnel will be the first in Switzerland to feature a rigid overhead conductor rail system. This will allow speeds of up to 250km/h. To install the components, which are up to 12m long, PORR commissioned the development of a special assembly unit.
-
EmployerAlptransit Gotthard AG
-
ContractorARGE Cablex-PORR-Consorzio
-
Project typeInfrastructure
-
Project scopeInstallation of railway infrastructure and overall coordination
-
Order volume206.4 million CHF (196.3 million euros)
-
Construction start05/2015
-
Construction end08/2020
Background
The Ceneri Base Tunnel is the continuation of the 57km long Gotthard Base Tunnel, which was commissioned on 11 December 2016. The tunnel is 15.4km long, making it the third largest tunnel construction project in Switzerland. It consists of two single-track tubes that lie 40m apart. These were constructed in opposite directions for safety reasons and are connected via cross passages every 325m.
At present, all freight and passenger trains between Bellinzona and Lugano are still forced to ascend the steep Ceneri ramp. These uphill journeys will become a thing of the past in August 2020, which is when the trial operations for the flat-line rail link through the Alps at the Gotthard Pass are scheduled to begin.
Work began on installing the rail infrastructure in the summer of 2017, after the structural work in the Ceneri Base Tunnel had been completed. Although the last tracks were laid in the Ceneri Base Tunnel towards the end of May 2018, the CPC (Cablex-PORR-Consorzio) consortium had already begun installing the railway infrastructure in February 2018.
The contract covers everything from construction logistics, power supply systems and data networking, to installing the control systems and the tunnel communications system. The sections implemented by PORR independently include erecting the overhead lines in the tunnel and on the access routes, installing the control systems, and constructing the railway earthing system.
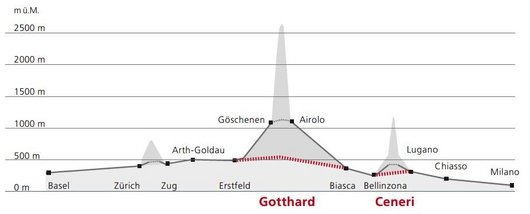
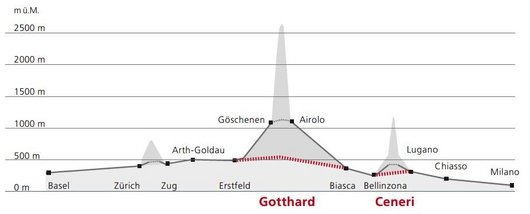
An overhead conductor rail instead of a catenary
In accordance with the revised SBB standards for overhead lines in tunnels, rigid overhead conductor rail systems (ROCS) are being installed in both tunnel tubes of the Ceneri Base Tunnel. The ROCS F+F CR4 for high speeds of up to 250km/h is being deployed here, marking a first for Switzerland.
Rigid overhead conductor rail systems offer a number of advantages compared to conventional overhead lines with catenaries. For example, there is no need for tensioning devices for the conductor wire and supporting cable. This allows for simpler and more compact structures and lower installation heights. An ROCS also has a greater current-carrying capacity than a catenary.
This wholly eliminates the need for amplification wires in some cases, depending on the current strength required. In addition, overhead rails have a greater short-circuit current capacity, are more fire-resistant and the contact wire has a longer service life.
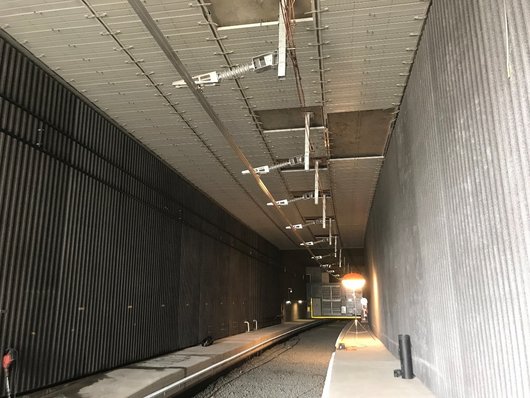
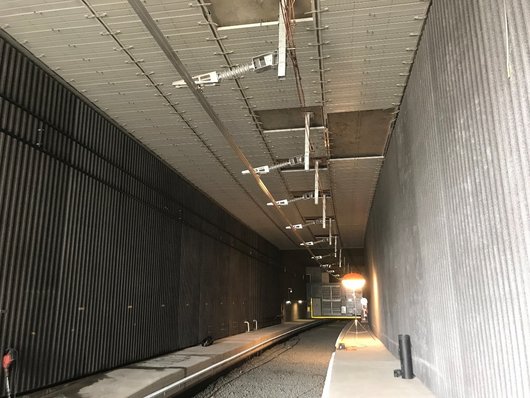
Installing the ROCS
The ROCS was installed in several stages. First of all, the suspension points for the truss posts were marked off along the tunnel vault as calculated during the planning phase. The anchoring holes were then bored using a multi-head boring machine. As soon as the boreholes had been made, a rail-mounted working platform was deployed to allow the work crew to install the anchoring dowels for the truss posts.
After bonding, the necessary tensile force had to be verified using pull-out tests, as specified in the inspection plan. If the results matched the required tensile force, the crew could start installing the truss posts.
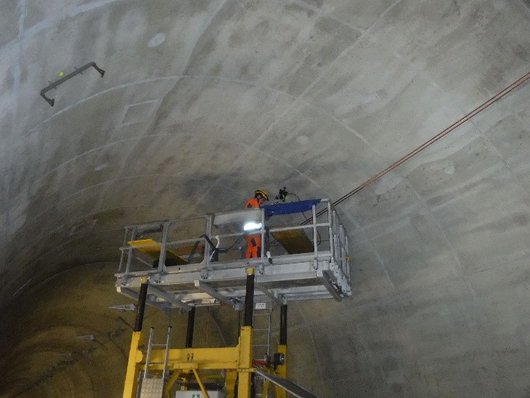
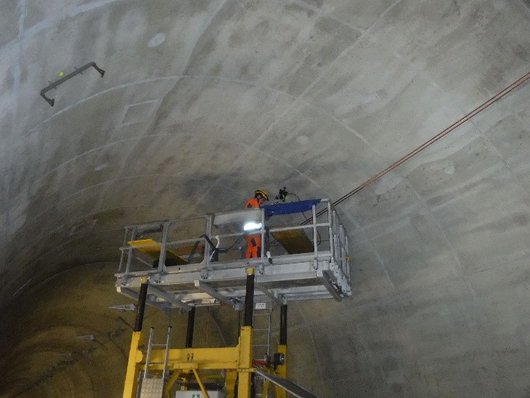
The 700mm long truss posts for the ROCS were mounted at 7m intervals using a special vehicle and a hydraulic lift. In the Sarè cavern, where the tunnel widens to allow for a future continuation of the line, truss posts with lengths of up to 2000mm were used to accommodate the high ridges. Additional guy ropes were attached to these long truss posts to ensure the necessary rigidity of the ROCS.
The anchoring dowels in the Sarè cavern failed the pull-out tests and had to be reinstalled. A detailed analysis showed that there were cavities behind the jetcrete of the tunnel vault. Once the cavities had been repaired by the client, the crew was able to install the anchoring dowels again.
The truss posts were mounted and the prefabricated tunnel supports were attached to them. The supports were aligned to the track axis, both vertically and in terms of position. This preliminary alignment facilitated the fine calibration of the ROCS during final assembly.
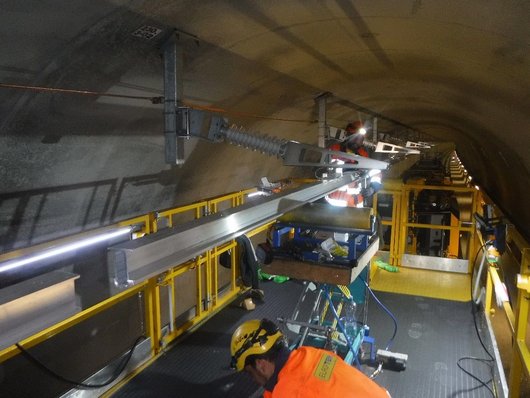
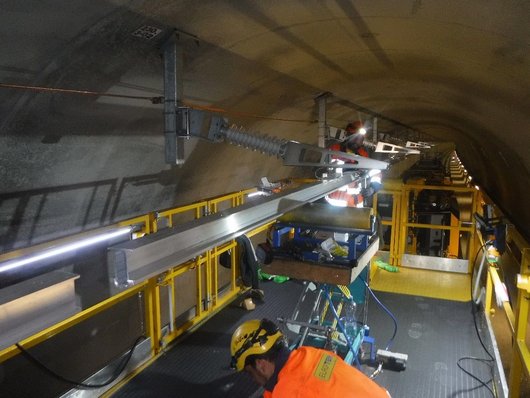
An assembly unit was developed especially for this project for the assembly of the rigid overhead contact rail components. The unit automatically transfers the components from the storage vehicle to the assembly unit and then raises them to the correct assembly height.
After the supports had been mounted, the 12m long ROCS elements were secured to the girders. An assembly unit was developed especially for this project to assemble these components. The unit automatically transfers the components from the storage vehicle to the assembly unit and then raises them to the correct assembly height. This automated process facilitated a higher degree of efficiency by increasing the speed at which the components could be installed. It also offered occupational safety benefits for the technicians, as the ROCS elements did not have to be raised manually.
After the ROCS components had been installed in the tunnel tube, the contact wire was inserted into the profile of the rigid overhead conductor rail with the aid of a cable pulling unit.
A transition bar was mounted at the portals to integrate the rigid overhead conductor rail system into the moveable conventional catenary system. As it enters the tunnel, the contact wire runs directly into the conductor rail profile via the transition bar, which absorbs the vibrations transmitted along the contact wire.
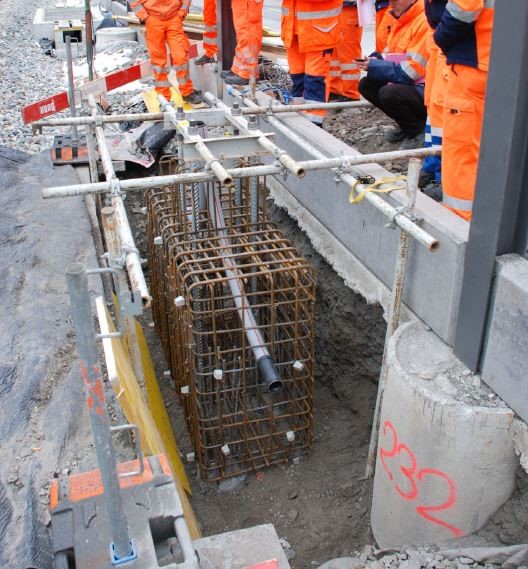
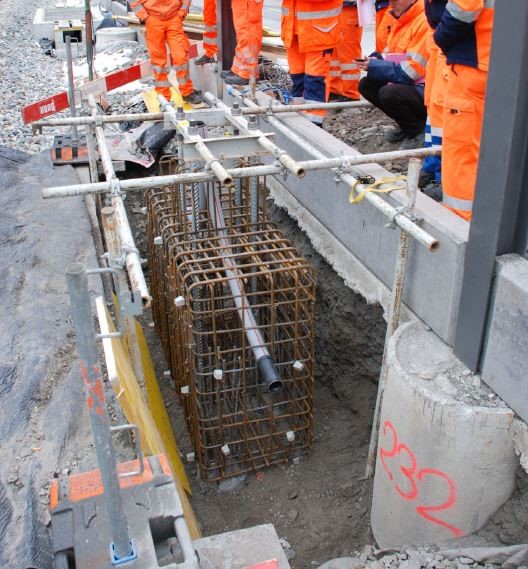
A helicopter was used to place the catenary support poles outside the tunnel on their foundations, as at the time of installation there were no tracks available for the work crew to erect the supports from rail-mounted vehicles.
The challenges
Work on the overhead lines inside the tunnel was completed at the end of August 2019. This was followed by the installation of the conventional overhead line outside the tunnel from September 2019 to February 2020.
The pole foundations and the support poles for installing the contact wire had already been constructed in summer 2017.
As the planning basis for the project did not match the actual conditions on site, constructing the foundations became a real challenge. Within the framework of a complex planning procedure, the necessary pile foundations had to be dimensioned and approved by the Swiss Federal Office of Transport (FOT).
In addition, special steel foundations were required at the portals, as the preliminary design had not sufficiently taken into account the original approach slab in the transitional area between the sections outside and inside the tunnel.
A helicopter was used to place the catenary support poles outside the tunnel on their foundations, as at the time of installation there were no tracks available for the work crew to erect the supports from rail-mounted vehicles.
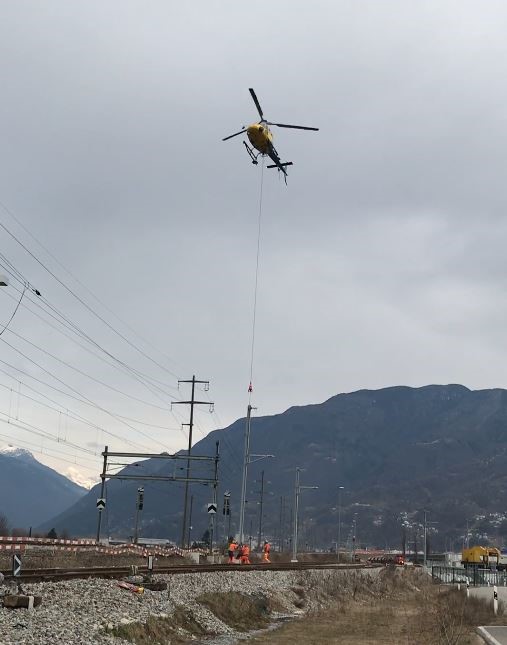
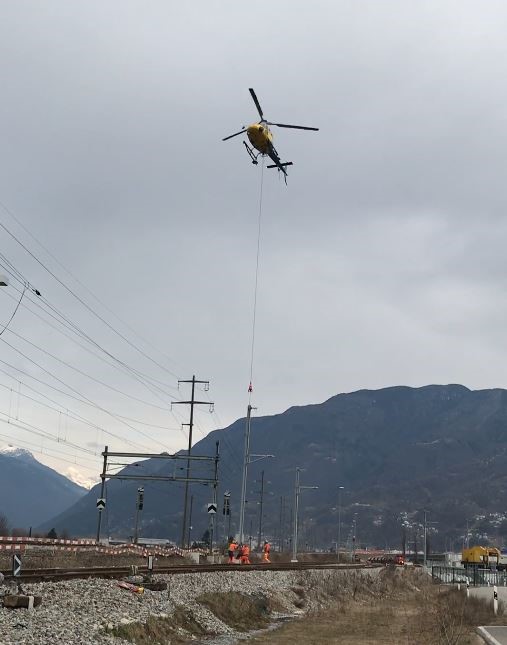
Trial operations at speeds of up to 275km/h
After the entire overhead line and railway infrastructure had been completed, we were able to start the trial phase as scheduled on 1 March 2020 under the management of AlpTransit Gotthard AG. This involved testing the complex interplay of all the systems in the Ceneri Base Tunnel. The test phase includes checks on all system components that are in operation, including the connection of the overhead line and the necessary high-speed runs at up to 275km/h for the purpose of providing documentation to the FOT.
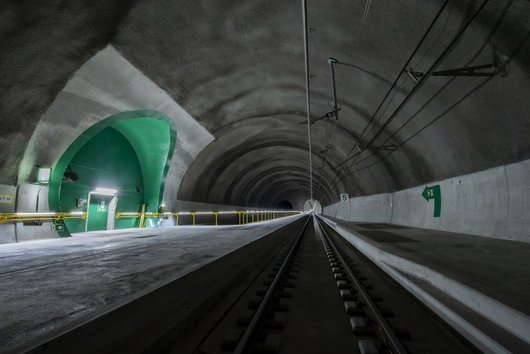
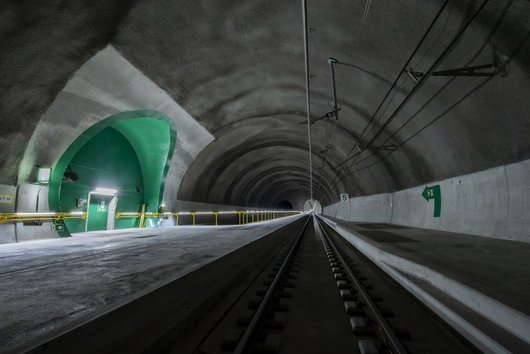
Outlook
Not only must long-distance transalpine transport be possible in December 2020, when the new timetable is introduced, the entire light rail system in Ticino must also be available. The Ceneri Base Tunnel plays a key role for future regional transport services in the Bellinzona-Locarno-Lugano triangle. Travel times from Locarno to Lugano will be cut in half, from 58 to 30 minutes, and passengers will no longer have to change trains. Travel times between Bellinzona and Lugano will be reduced to just 12 minutes. Commercial operations of 50-80 passenger trains and 220-260 freight trains per day have been provided for. The tunnel is designed for a maximum speed of 250km/h for passenger trains and 160km/h for freight trains.
Technical data
-
Tunnel length15.4km
-
Total length of the entire tunnel and passage system39.8km
-
Maximum gradient inside tunnel12.5‰
-
Cross passages48
-
Maximum rock overlay1,040m
-
Overhead line inside the tunnel2 x 15km
-
Overhead line outside the tunnel3 x 1km
-
Number of tunnel supportsapprox. 4,200
-
Fibre-optic cables10,500km