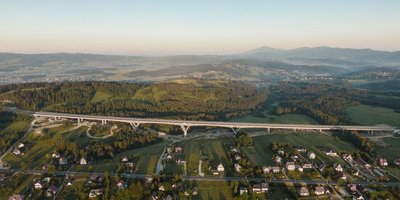
The S7 expressway Kraków-Rabka Zdrój
At temperatures approaching minus 35 degrees, PORR built an almost one kilometre long prestressed concrete bridge along the new Zakopianka expressway in Poland.
The highly complex project was governed by a great many variable geometries and extremely difficult working conditions, which meant that PORR had to develop new technologies and processes for constructing the bridge.
-
EmployerSalini Impregilo
-
ContractorPORR S.A.
-
ArchitectVössing GmbH
-
Project typeInfrastructure construction . Bridge construction
-
Project scopeConstruction of Structure no. 21 on section Skomielna Biała-Chabówka of the S7 expressway Kraków-Rabka Zdrój
-
Order volume20 million euros
-
Construction start09/2016
-
Construction end07/2019
Overview
More than 100km long, the "Zakopianka" connects Krakow with the winter sports resort Zakopane and is widely regarded as one of the Polish transport network's major trouble spots. The route, constructed in the 1930s and full of twists and turns, is primarily associated with traffic jams several kilometres long, especially in the winter months. To improve the situation and to alleviate traffic congestion on what is popularly known as the "Highway of Tears", construction of an expressway was started in 2016.
PORR was awarded the contract for the construction of Structure no. 21, the highest and longest bridge on the route. The mountainous environment and unpredictable weather conditions with temperatures dropping to minus 35 degrees Celsius made this project a real challenge.
A unique bridge
The nearly one kilometre long bridge was planned as a frame and girder construction with twelve individual spans. The Y-shaped piers that were necessary to support the longest bridge spans were rigidly secured to the girder structure. The other bridge piers were mounted on bearings.
The loads are transferred into the ground via solid foundations and large-diameter piles. The variable geometry, which meant that almost every single component is one-of-a-kind, forced the PORR team of experts to develop new technologies, without which it would not have possible to construct the bridge at all.
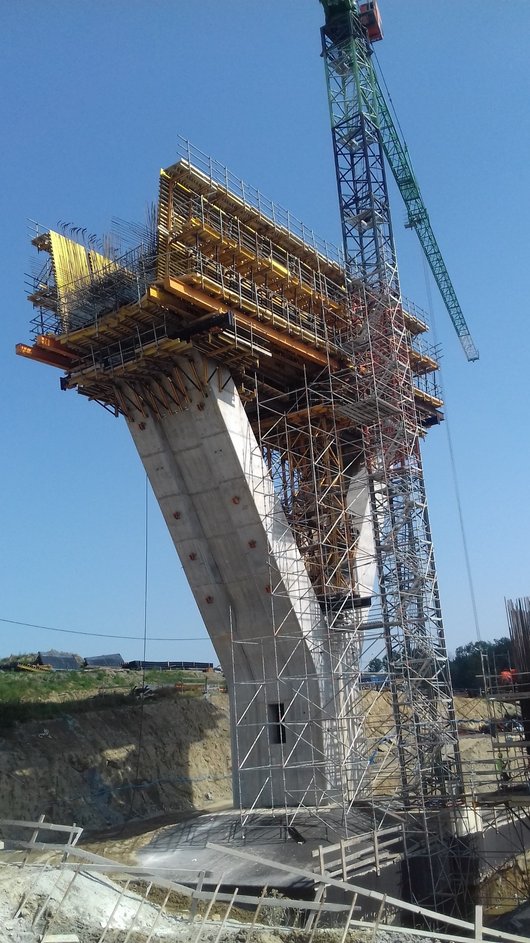
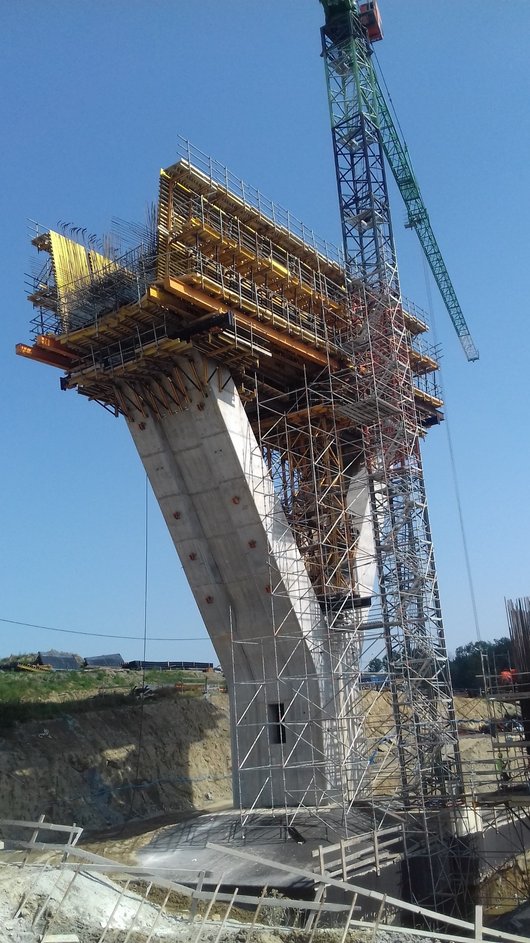
Three Y-shaped bridge piers stand on solid 26.2m x 15.8m x 4.0m foundations, each of which con-sists of 226t of reinforcing steel and 1,200m³ of concrete.
Foundations and piers
The three Y-shaped bridge piers stand on solid 26.2m x 15.8m x 4.0m foundations, each of which consists of 226t of reinforcing steel and 1,200m³ of concrete. The loads are transmitted into the ground via 36 piles, each with a diameter of 1.5m and a length of 22m. Due to the huge dimensions, the temperature development inside the components was monitored for 24 hours after the concrete works had been completed in order to prevent excessive differences in temperature between the inner and outer surfaces.
For construction purposes, the Y-shaped piers were divided into the three sections "pier shaft", "head" and "arms". The pier shafts were concreted in 5m-high segments by hanging movable formwork on the previously concreted section, after which the head and arms were concreted. The arms were divided into seven segments, each 2.20 m high, and were erected using a slipform. Once one segment of the arms had been concreted and the concrete had reached the required load-bearing capacity, hydraulic cylinders were used to move the formwork to the next segment, where it was anchored to the previous segment.
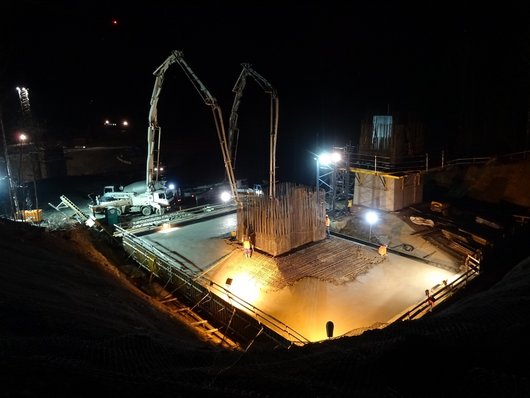
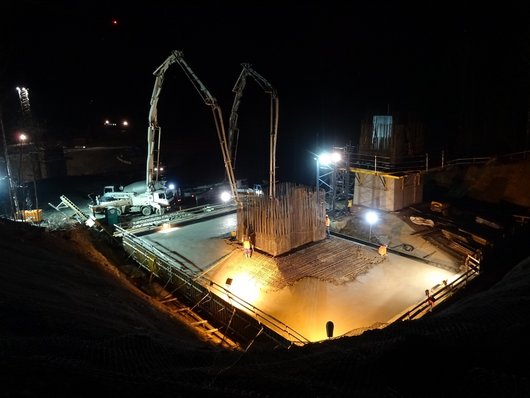
Load-bearing structure of pendulum access parts
The individual bridge spans (access parts for pendulums) were constructed in two sections, each of them 70m long, heading towards the centre of the structure. The formwork required for this consisted of floor slab formwork, brackets, webs and sleeve formwork. The structure was based on a framework consisting of ten trusses connected by a bracing system. Each span consisted of three independent truss spans, which were freely supported by temporary girders. The temporary columns were tubular tubes mounted on temporary foundations.
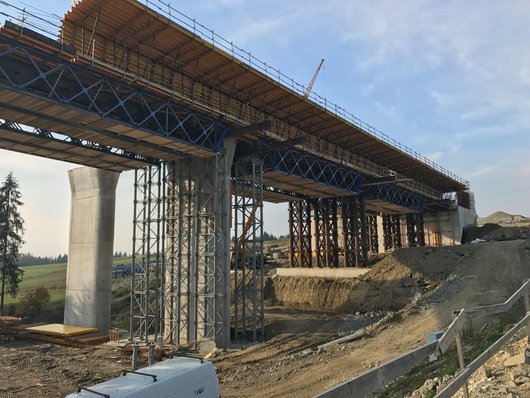
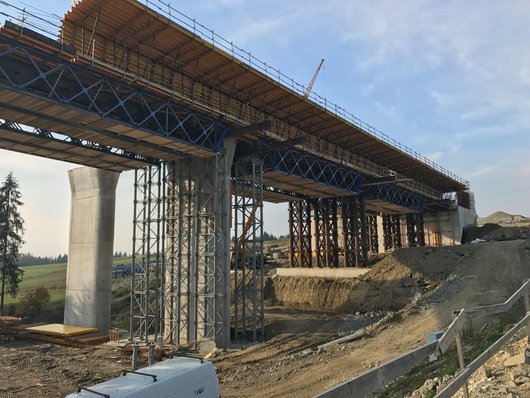
Approximately 700m³ of concrete were used for each starting segment.
Girder system for the cantilever
Once the arms of the Y-shaped bridge piers had been erected, work began on constructing the starting segments for the cantilevered section. The segments connecting the supporting arms were concreted in three segments - the floor, the walls and the cross beams, plus the suspension plate. In the middle, the formwork structure was supported by a tower mounted on top of a Y-shaped pier. Approximately 700m³ of concrete were used for each starting segment.
After the starting segment was completed, the so-called "travellers" were assembled. These are sliding devices used to erect the next segments of the cantilever system.
The order of concreting was determined by the pre-stressing cable lashings, introducing a horizontal force into pendulum, thus ensuring the global stability of the structure.This method required constant geodetic monitoring and continuous analysis, which was undertaken by the planner, who compared the actual distortions with the projected ones on an ongoing basis and updated the plans as necessary.
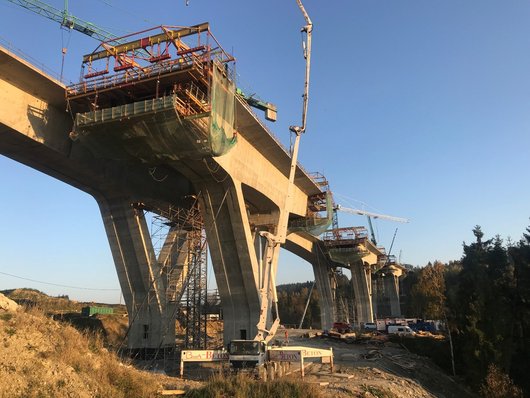
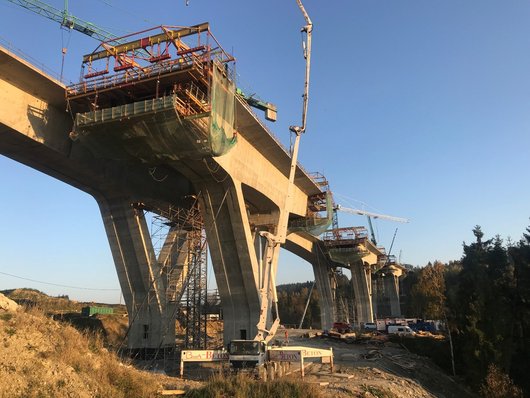
The final stage in the construction of the girder structure involved concreting the keystones connecting the individual bridge sections. The columns and approaches were also stabilised with a steel structure to prevent horizontal and vertical displacement of the concrete components caused by temperature fluctuations. Temperature fluctuations to +20 degrees Celsius were offset by introducing friction forces by the pretensioning rods.
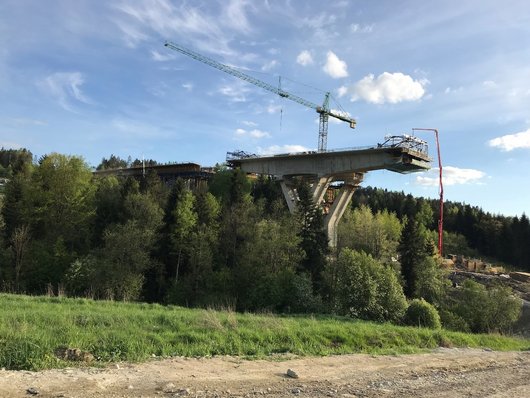
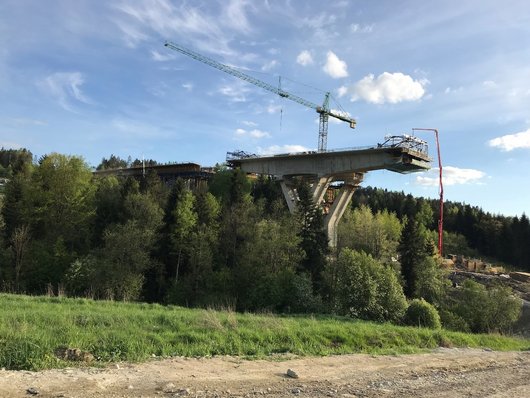
Finishing works
Once the girder construction was completed, the extensive finishing works were carried out. Pavement covers were created, along with bridge barriers and anti-glare screens. The road surfaces including the drainage facilities were also constructed and the final dynamic and static load tests were carried out.
Despite the high degree of complexity, difficult terrain and erratic weather conditions, PORR brought the project to a successful conclusion in July 2019. This success would not have been possible without the experience, knowledge and enormous commitment of everyone involved.
Technical data
-
Length of the bridge992m
-
Width of the bridge15.40m + 14.60m
-
Type of bridgePrestressed twelve-span bridge
-
Length of the longest span140m
-
Number of spans12
-
Highest bridge pier43m
-
Height of the structure50m
-
Incorporated steel13,000t