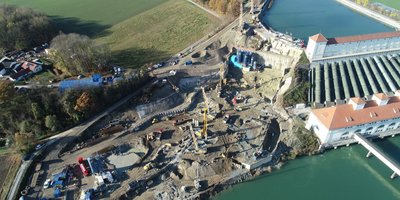
Töging-Jettenbach power station replacement
A new power station has been built in Töging to take over from the old power station. PORR was responsible for eight of the nine construction sections.
While still in the planning stage, PORR developed an alternative execution variant for the main construction pit in the centre – and this variant ultimately won PORR the contract. The scheme was tested for feasibility in advance during a large-scale test.
-
EmployerVerbund Innkraftwerke GmbH
-
ContractorPORR GmbH und Co. KGaA
-
ArchitectTractebel Hydroprojekt GmbH
-
Order typeBaumeisterarbeiten
-
Project typeSpecialist civil engineering
-
Project scopeCreating the construction pit for the new power station
-
Order volumeapprox. 28 million euros
-
Construction start10/2018
-
Construction end04/2020
Background
Generating electricity with hydropower has a long tradition in Töging: the Töging-Jettenbach power station was commissioned back in 1924. Ever since, water from the River Inn has been directed into the Inn Canal from the weir in Jettenbach. The water flows down the 20km channel to reach the Töging powerhouse, where electricity is generated by 14 generating units.
The “Töging-Jettenbach Power Station Renovation” project was launched in autumn 2018, with the objective of increasing performance by around 25 per cent. The electricity generated covers the annual power consumption of around 200,000 households.
The project isn’t limited to the new power station investment: the weir in Jettenbach is also being replaced with a new, more efficient model. In order to be able to divert more water into the Inn channel, the maximum water level is being raised by 70cm. The Fraham and Jettenbach dams are being upgraded to withstand a 1000-year flood. In total, the consortium is investing 250 million euros in the scheme.
The project was carved up into nine construction sections, covering the improvements to the Fraham retention area, the Jettenbach weir, the channel enhancement and the new power station in Töging. Eight of these, representing a total order volume of 150 million euros, were awarded to PORR, including the specialist civil engineering work for the construction pit. Execution in Jettenbach and Töging was carried out as an internal joint venture between a number of departments: Specialist civil engineering, Vienna Civil engineering Vienna, Salzburg Civil engineering and Linz Civil engineering. All departments participated equally.
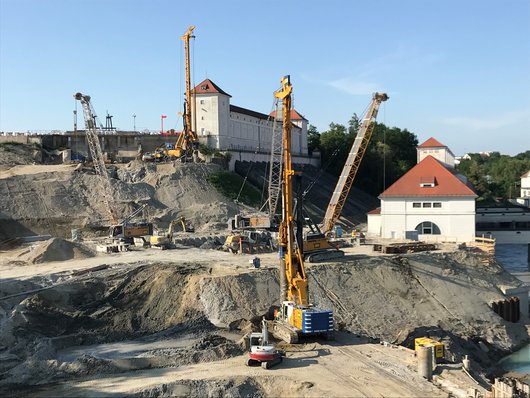
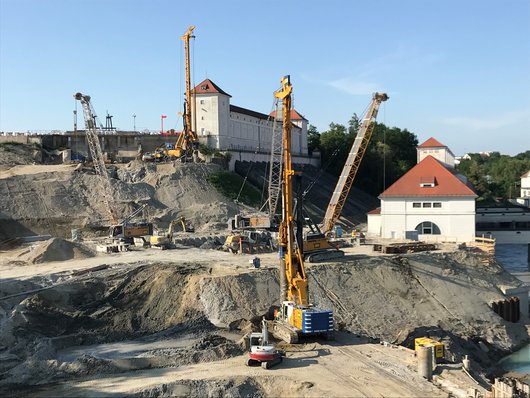
Geological complications
The central element of the specialist civil engineering work was the main construction pit for the new powerhouse. Creating the pit involved almost every type of work in the specialist civil engineering department. The construction pit had a length of 200m and extended 50m into the air. During the excavation, conditions on the construction site were constantly changing. The work had to be constantly adapted to new situations.
There were five pressurised aquifers that the construction pit work needed to take into account, with the pressure increasing with each aquifer. The fifth aquifer was under artesian pressure by comparison with the original ground, meaning that the pressure level extended beyond the site.
This put so much pressure on the raised construction pit bed that without additional measures, the pit bed would have been unstable and broken up. The entire construction pit therefore had to be given a watertight seal where it passed through the fifth aquifer. It was then possible to lower the pressure with the aid of dewatering wells up to 56m deep, and safely excavate the construction pit.
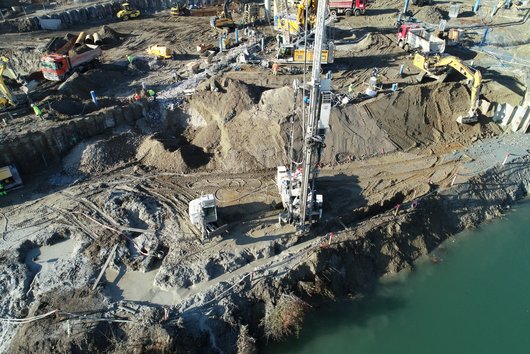
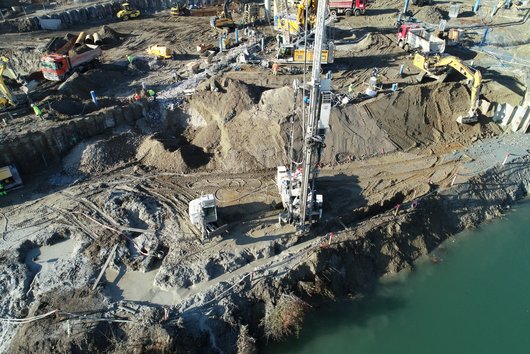
PORR came up with an alternative execution variant while still in the tendering phase; it was this variant that won over the employer and was a major factor in PORR being awarded the contract.
Successful variant
PORR came up with an alternative execution variant while still in the tendering phase; it was this variant that won over the employer and was a major factor in PORR being awarded the contract. In the original plans, the construction pit was to have been sealed with a two-phase diaphragm wall. Excavation work would have been protected by a bentonite suspension, which would later be replaced by concrete.
However, in order to counteract the pressure of the fifth aquifer, this bentonite suspension would have had to be produced at an unusually high concentration, which would have been difficult to displace when the diaphragm wall was concrete. There would have been a risk of causing unobserved faults in the sealing wall, which would have been impossible to correct subsequently.
PORR developed an alternative in which the diaphragm wall was constructed as a one-phase wall. The key difference is that the bentonite suspension was replaced by a self-setting support fluid – a mixture of bentonite, cement, slag sand and blast furnace slag. With this method, the support fluid is kept in constant motion by the activity of the diaphragm grab, preventing the cement from setting.
Once excavation is complete, the cement sets to form a watertight, hardened wall in the subsoil. Since the sealing wall cannot serve any structural function, bored piles were built inside the sealing wall to take on the bearing function. This technique had already been tested with diaphragm walls up to 40m deep and excavation periods of up to 14 hours.
However, at Töging the diaphragm wall depth was 72m and the planned excavation period 24 hours. To test the procedure for feasibility under these conditions, large-scale tests were carried out in Himberg.
Large-scale test in Himberg
The first step was to develop the material for the one-phase wall. TAL Betonchemie Handel GmbH and Bautech Labor GmbH collaborated to develop a suspension that met the requirements for processing time and final strength.
A large-scale test was then carried out in Himberg, with PORR Equipment Services GmbH, to simulate the activity of the diaphragm wall grab.
A jet grouting machine was equipped with electric controls to the suspension in motion for 24 hours. The test also simulated interruptions to the work due to unexpected equipment failures. A suitable mixture was developed – which then had to pass a groundwater tolerance test.
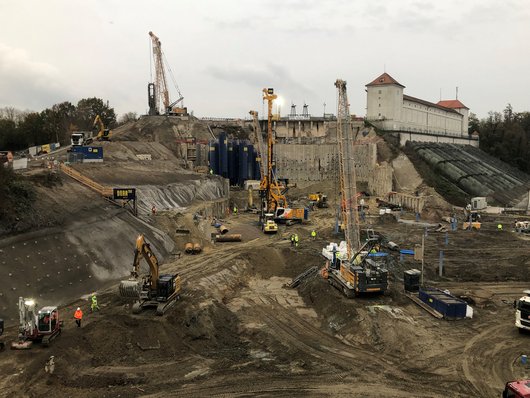
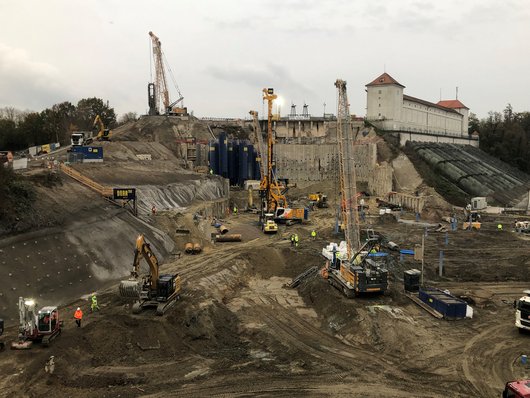
A nasty surprise
The first sealing wall element was manufactured in mid-April 2019. At an excavation depth of 60m, the team encountered conglomerate, which was very difficult to pierce with the diaphragm wall grab. After a mere 48 hours of excavation, the suspension had set so much that it was no longer possible to create the diaphragm, and excavation had to be halted.
Adjustments were made to both the equipment and the suspension, to meet the new circumstances. In order to help the diaphragm grab sink down in the diaphragm and improve loosening, it was fitted with a thirty-tonne ballast weight.
The sealing wall suspension itself was produced in two separate phases. As far as the fifth aquifer, the team used a very low density suspension of pure bentonite. Shortly before reaching the pressurised aquifer at a depth of around 35m, the suspension was mixed with a suitable concentration of hydraulic binder. With the lighter suspension, excavation down to 35m could be executed faster, leaving sufficient time to pierce the lower hard conglomerate layers before the suspension set.
To ensure the modified suspension still met the requirements once set in final state, TAL and Bautech Labor were present on the construction site to help with manufacturing the suspension.
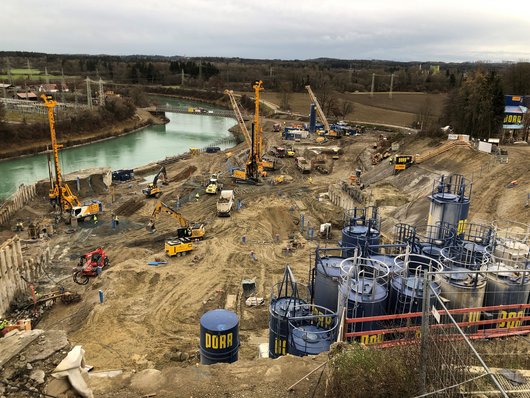
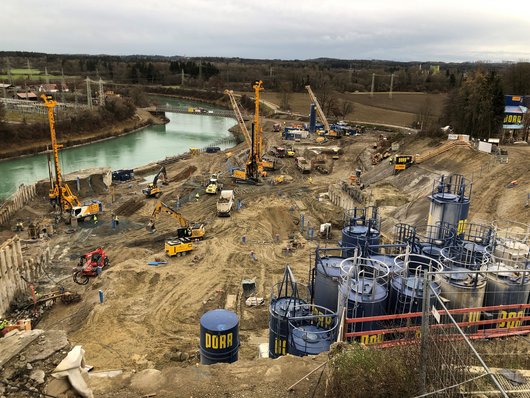
More alternatives
The fifth aquifer wasn’t just a challenge for creating the construction pit bed and diaphragm wall. The deep anchoring included in the original plans would have had to be manufactured against this extremely high water pressure. Since construction against water pressure represents a huge risk, another alternative variant was planned for this stage.
In the new scheme, the two deepest anchor positions were replaced with a circular support installed inside the pit, which served as bracing. Once the base slab had been built beneath the circular support, the loads from the temporary construction pit system were transferred to the base slab, and the circular support was demolished.
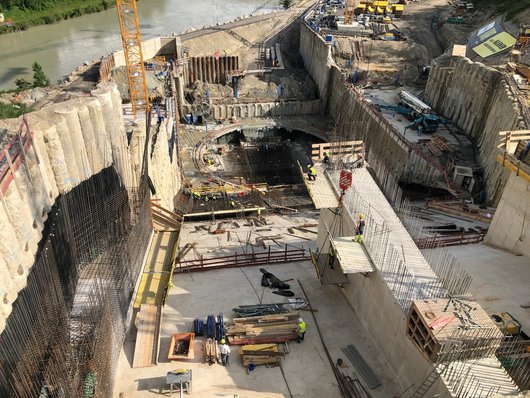
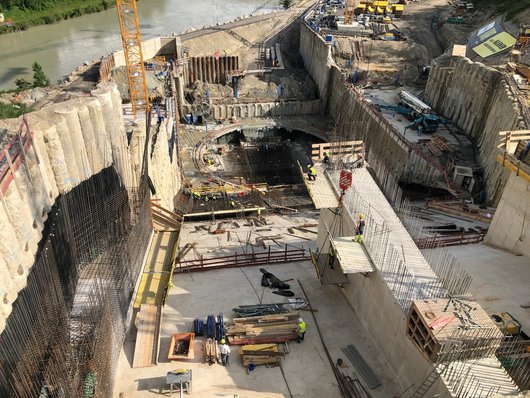
Continuous optimisation
PORR was able to introduce various additional optimisations while building the construction pit. These were developed using the value engineering method. For example, we achieved dewatering, which originally used 100 dewatering wells, with just 60 wells. Another improvement: the majority of the originally planned secant bored pile walls were replaced with spaced bored piling, secured with spandrels using the jet grouting method. This saved on both construction time and wear. An initially highly complex measurement system was also simplified thanks to PORR’s expertise.
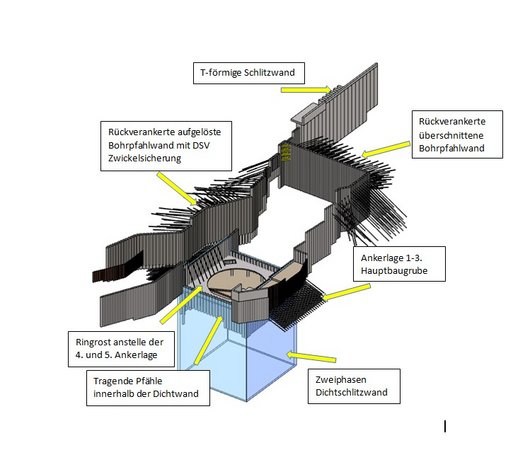
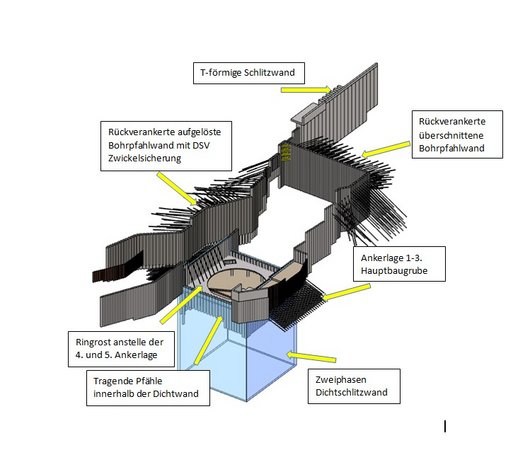
Technical data
-
One-phase diaphragm wall12,500m², depth to 72m
-
Two-phase diaphragm wall6,500m², depth to 35m
-
Bored pilesapprox. 13,500m, depths to 30m
-
Anchors500; 13,000 running metres bored
-
Jet groutingapprox. 5,500m, depths to 72m
-
Steel built inapprox. 900t
-
Concrete built in17,000m³
-
Anchor cement500t