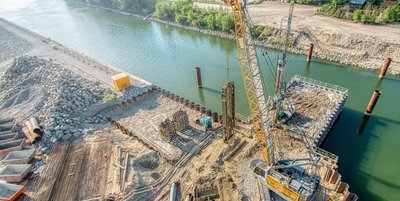
Albern Harbour Gate
PORR worked with Andritz Hydro GmbH to design and construct a gate at Albern Harbour in Vienna to protect against flooding, all during active port operation.
Planning and building a gate for Albern Harbour is a highly complex undertaking; so complex, in fact, that all of the tasks involved require functional specifications and commissioning. The meticulous design for the Hafentor Albern consortium won over the client completely.
-
EmployerHafen Wien GmbH
-
ContractorARGE Hafentor Albern - PORR Bau GmbH/ANDRITZ HYDRO GmbH
-
Order typeFunktionale Leistungsbeschreibung
-
Project typeCivil engineering, earthwork, structural engineering, plant construction
-
Project scopePlanning and construction of a harbour gate flanked by flood protection dams
-
Order volumeEUR 17.53 m
-
Construction startDezember 2019
-
Construction endFebruar 2022
Overview
Albern Harbour is located in the 11th district of Vienna and belongs to Hafen Wien GmbH. It has a total capacity of 90,000 tonnes, making it one of the most important grain transhipment points in eastern Austria. Building materials, agricultural produce and steel products are all transferred and reloaded here, too. Moreover, Albern Harbour, which is home to a heavy goods centre for transhipment of single loads of up to 450 tonnes, has repeatedly suffered from flooding. In the most recent incidents, the entire site was under more than a metre of water in 2002 and 2013. Hafen Wien GmbH decided to have a harbour gate constructed to prevent such occurrences in future, given that they cause millions of euros of damage to the harbour facilities, business premises and stored goods.
The works required to construct the gate were set out in functional specifications and tendered in a negotiation procedure. The project encompasses the planning and construction of the gate structure, including connecting it up to the existing flood defence systems, a pumping station, an operations building and all of the outdoor facilities.
The client’s decision to make the project subject to functional specifications and executed accordingly meant that PORR was able to contribute its ideas and expertise to the joint project objective as early as the planning process.
The harbour gate
The main structure consists of the gate chamber, the sill and the counter-structure. When open, the gate chamber serves as a storage site for the gate and can be used as a dry dock for maintenance purposes. The sill, with its rail built into the sill cap, guides the opening and closing movement of the gate. The counter-structure serves as the end of the sealing level when closed. Both the gate chamber and the counter-structure are connected to the existing parts of the Danube flood protection system with sealing walls and the associated embankments to form an end-to-end sealing level.
Alongside the gate chamber, a two-storey operations building and a pumping station were constructed; the latter can regulate the water level in the inner harbour in the event of flooding. The gate itself is a movable steel sliding gate approx. 30m long, 15m high and weighing around 250 tonnes.
In planning and executing the harbour gate, the biggest challenge was maintaining shipping traffic to the Albern Harbour throughout. The construction project was divided into two phases to ensure that shipping could continue unimpeded. This allowed a 15m-wide channel to be kept free for shipping traffic.
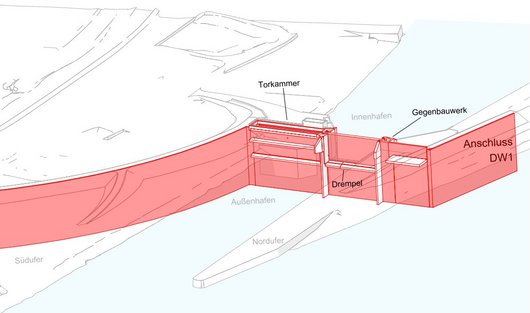
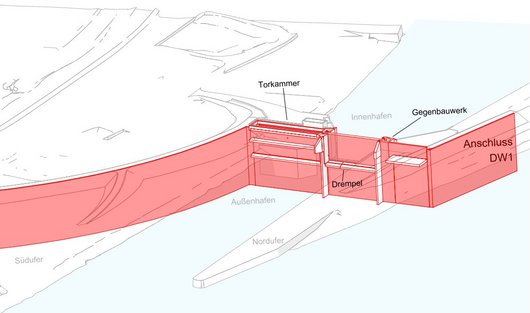
The first step comprised the construction of part of the sill on the northern side, the rising counter-structure, including its foundations, which are comprised of in-situ concrete diaphragm walls and the necessary sealing walls. The second part of the sill, the gate chamber (also founded on in-situ concrete diaphragm walls) and the necessary sealing walls that connect to the existing dam, were then built on the south side.
Constructing the sill and the gate rail affixed to it meant erecting a substantial structural element below the existing harbour floor in two separate phases of construction. A special construction pit solution was devised, planned and implemented by PORR Bau GmbH’s civil engineering department, which allowed the sill to be constructed in a dry construction pit roughly 10m deep. Not only did this make it possible to install the harbour gate in dry conditions, but it also proved crucial to the seamless construction of the second sill section. This required sheet-pile structures that were reinforced under their respective load cases using deadman anchors and mobile bracing elements.
Construction phase 1
First, the scour protection on the north side was removed and excess material was banked up to build the quay walls, using a sheet piling structure reinforced by deadman anchors. After the work on dry land was complete, a three-sided sheet piling enclosure was erected as a peninsula arising from the water to maintain the designated shipping channel. This required a pontoon ship with the necessary stability and length to carry the sheet pile driver, while maintaining good manoeuvrability within the harbour basin. These conflicting requirements were met by creating a special process scheme for installing the sheet piling. Once again, PORR was able to demonstrate its many years of expertise in specialist civil engineering on water and complete the work on schedule, despite the difficult conditions.
Once the finished sheet piling enclosure had been braced with mobile reinforcing frames, it was filled with compactable material and the guide walls for the connecting in-situ concrete diaphragm walls were installed. The construction of the diaphragm walls proved particularly challenging due to the highly restricted space on the sheet-piled peninsula and the conversion work on the bracing structure as part of the process.
The diaphragm walls were built to a depth of around 25m. These had to serve as a deep foundation for the sill and the counter-structure, while also meeting the necessary requirements for a sealing wall. One area of particular focus was integrating the diaphragm wall into the existing dam so as to ensure the tightness requirements for flood protection. Once the diaphragm wall elements on the sheet-piled peninsula were complete, the jet-grouted sealing base had to be created at the same time as the construction of the diaphragm wall, due to the tight and complicated schedule. The jet-grouted sealing base is a key element of the complex construction pit solution, as the construction pit had to withstand water pressure of around 10m when excavated, and the lower edge of the sheet piling wall rested on the extremely permeable Danube gravel.
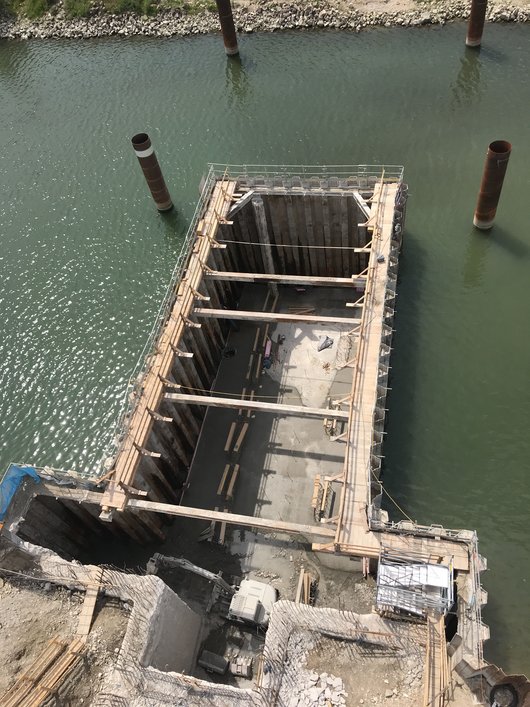
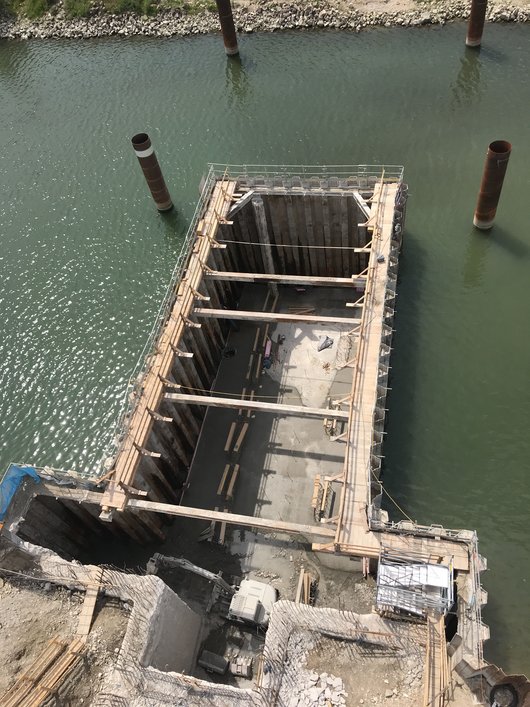
The civil engineering work came after the excavation of the construction pit. In order to mount the built-in elements – gate rail, lateral reinforcement and ice prevention – in the correct position, they were cast in second-stage concrete and affixed to the built-in parts.
To create the connection with the completed sill section in construction phase 2, which involved erecting the gate chamber and sill on the southern side, a special transverse bulkhead structure was designed to serve as a new end face for the sheet piling enclosure to the south. The creation of a horizontal joint seal between the lower edge of the transverse bulkhead and the upper edge of the sill, including the gate rail, was the subject of particular attention, as the transverse bulkhead could only be positioned on the sill, not structurally connected to it.
The sheet piling enclosure was ready for flooding after the completion of the phase 1 concrete construction work. That signalled the start of construction phase 2 on the southern side of the harbour basin.
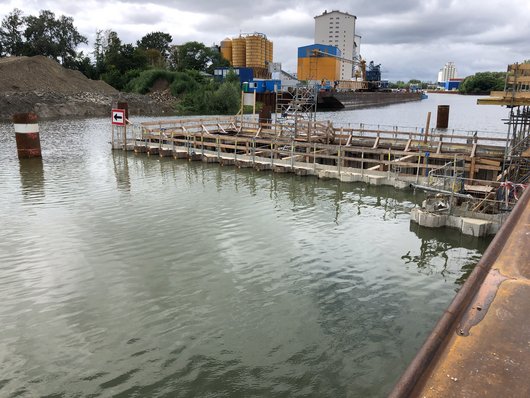
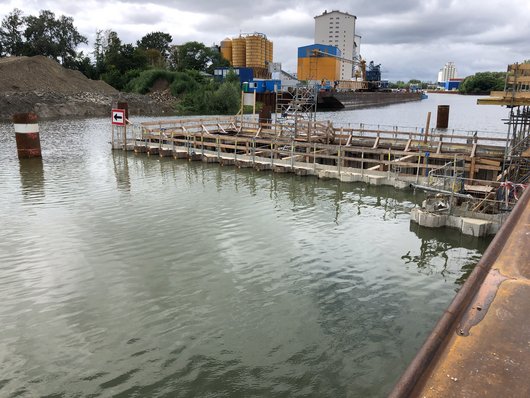
The foundations of the gate chamber rested on the diaphragm walls and were anchored back to the sheet piling for the quay wall using deadman anchors. This allowed the construction pit to be excavated between the diaphragm walls while the walls themselves were being completed.
Construction phase 2
The sheet piling from construction phase 1 was first removed and then reinstalled to create a peninsula on the southern side of the harbour for construction phase 2. After the work on the water, deadman-anchored sheet piling was erected on land and the necessary anchors installed. The preparatory work for the diaphragm wall, the construction of the diaphragm wall itself and the jet-grouted sealing base were all executed in the same way as on the northern side. After that, a sealing wall was built between the gate chamber, the main Albern dam, and the dam enclosing Albern Harbour.
The foundations of the gate chamber rested on the diaphragm walls and were anchored back to the sheet piling for the quay wall using deadman anchors. This allowed the construction pit to be excavated between the diaphragm walls while the walls themselves were being completed. Besides the gate rail in the sill, the horizontal and vertical gate guide rails, drive motors, slewing crane, ice prevention systems and lateral reinforcements all had to be cast in first-stage concrete. The operations building and pumping station were built at the same time as the construction in the gate chamber.
Following completion of the concrete construction work, the temporary construction pit was successfully flooded and the sheet piling enclosure could be dismantled on schedule. In early September 2021, the harbour gate, weighing some 250 tonnes, was lifted into place in two parts.
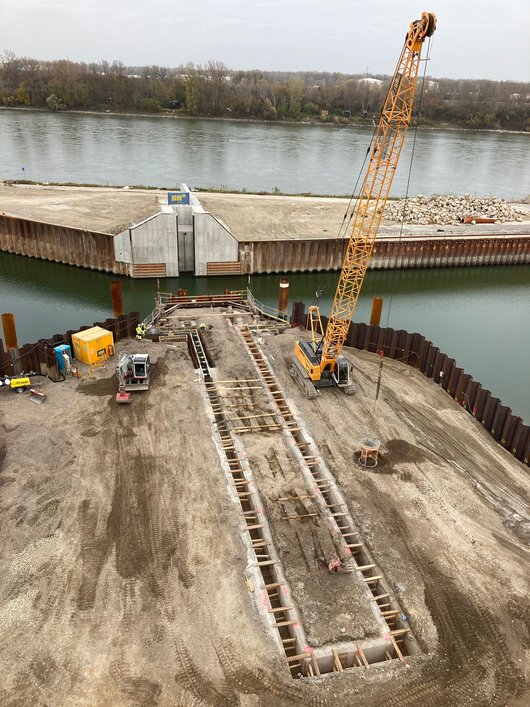
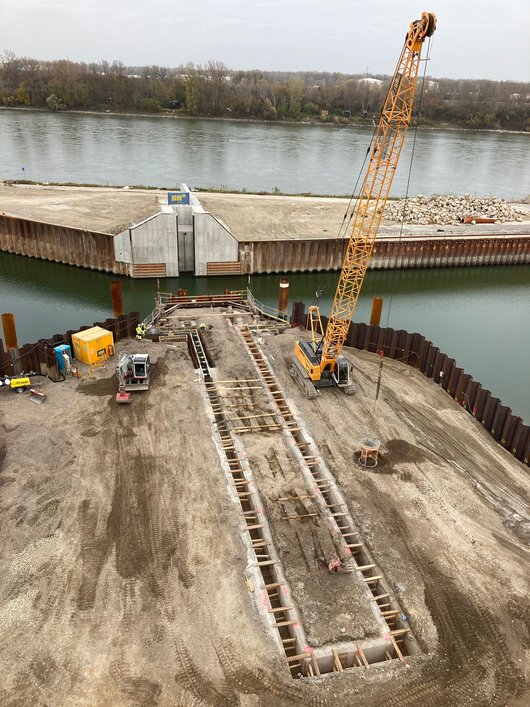
In planning and executing the harbour gate, the biggest challenge was maintaining shipping traffic to the Albern Harbour throughout.
Conclusion
The client’s decision to make the project subject to functional specifications and executed accordingly meant that PORR was able to contribute its ideas and expertise to the joint project objective as early as the planning process. Any risks were identified at a very early stage of the project as a result; the necessary overall conditions were created and the construction work was carried out as smoothly as possible.
Superb, interface-free cooperation within PORR was a key factor in the joint achievement of the project goal. Reliability, working shoulder-to-shoulder, appreciation, passion and pioneering spirit all played a vital part in the success. In construction phase 1, in particular, when the construction pit was completely flooded twice by high water, the specific conditions and imponderables of a project in a functioning port in the River Danube became more than apparent. It was possible to react flexibly and collectively to such events, so as to keep downtimes to a minimum.
The PORR team is proud to have made a significant contribution to the success of the overall construction project, with impressive, sustainable flood protection that will last for generations. It looks forward to taking on similar challenges in future.
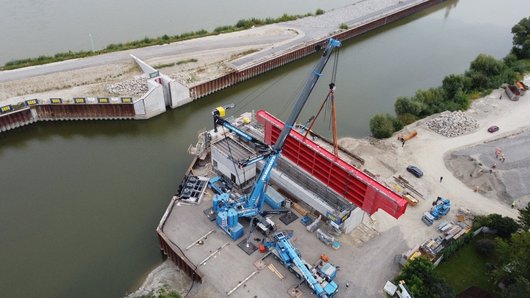
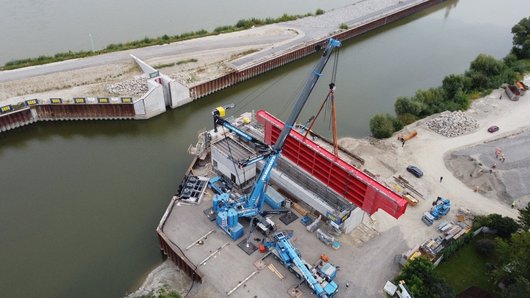
Technical data
-
Baugrubentiefe10m below the existing water level
-
Aushub46,000m³
-
Reinforced concrete diaphragm wall:4,000m²
-
Sealing diaphragm walls5,000m²
-
Jet-grouted base610m²
-
Jet-grouted slatted wall3,800m²
-
Sheet-pile walls6,500m²
-
Built-in reinforcing steel535t
-
Verbauter Beton7,300m³