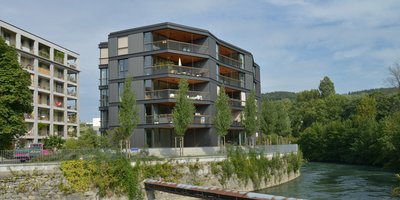
FEINSPINNEREI freehold flats
in the Swiss municipality
In just 22 months, PORR has constructed the Feinspinnerei residential building on former industrial wasteland in Windisch.
PORR relied on unconventional solutions for the implementation in order to master the logistical and constructional challenges: from the site facilities being located in a residential area to the tight dimensional tolerances between subsections.
-
EmployerHIAG Immobilien Schweiz AG
-
ContractorPORR SUISSE AG
-
Order typeTotalunternehmer
-
Project typeBuilding construction residential building
-
Project scopeConstruction of a five-storey residential building with 29 freehold flats
-
Order volume12 million Swiss francs (10.5 million euros)
-
Construction start08/2016
-
Construction end05/2018
General
The client, HIAG Immobilien Schweiz AG, specialises in the reutilisation of brownfield sites. This includes the former fine-spinning mill in Windisch’s Kunzareal, which was one of the largest spinning mills in Switzerland in the 19th century. Numerous listed buildings still bear witness to this eventful past and exude a historical industrial atmosphere. Now an area for residential and commercial use was to be created on the site of the old spinning mill, meeting all modern requirements while preserving the historical heritage. To achieve this, existing buildings were converted, and additional new buildings constructed. Situated right next to protected alluvial forests and the River Reuss, it offers residents a retreat in Switzerland’s picturesque Wasserschloss region.
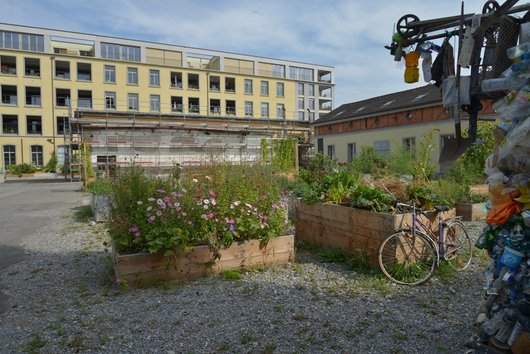
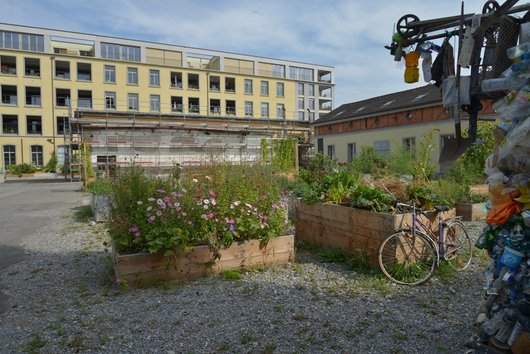
Call for tenders
The original architectural competition provided solely for the conversion of the old spinning mill building. In a second competition, it was decided to add a new building with a contemporary appearance, as an optical counterpoint to the industrial character of the existing buildings.
A group of planners developed the project further and prepared a call for tenders for a full-service general contractor, which PORR won. The site team was faced with a number of technical challenges, all of which were solved with ingenuity and skill.
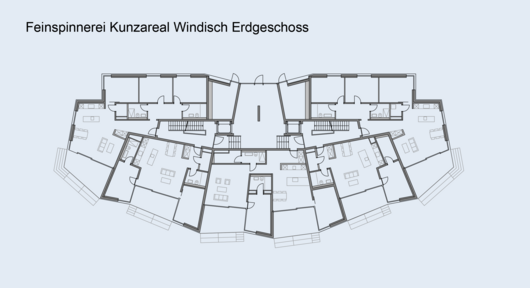
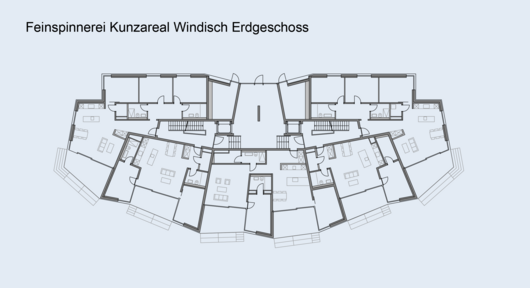
Site facilities
As the site is located on the edge of a residential district, PORR attached great importance to the interests of the local residents, starting with the installation of the site facilities. The access routes to the construction site were therefore chosen in close consultation with local residents, and the number of construction site vehicles was reduced to the minimum necessary. This kept the production of noise and dust as low as possible.
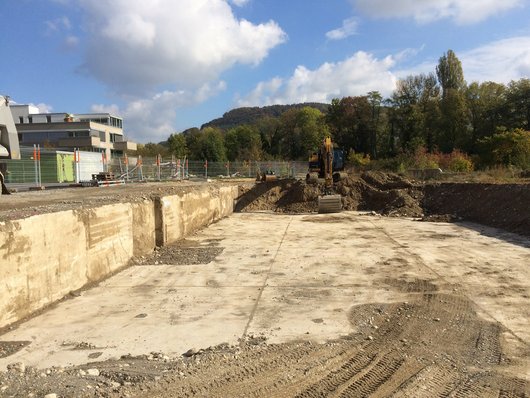
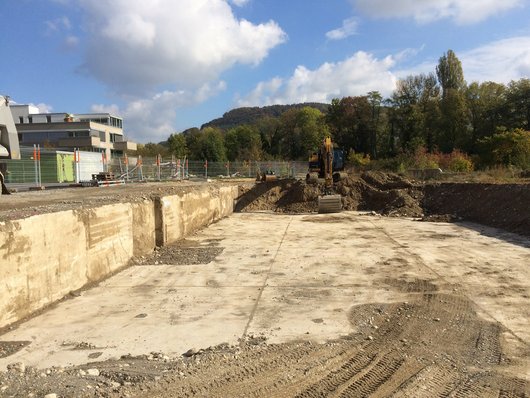
Construction in groundwater protection zones
The former Windisch fine-spinning mill is located in the heart of a groundwater protection zone. Pumping and underwater construction were forbidden. Nor was it permitted to use engineering methods to ensure that the groundwater level was kept below the bottom of the construction pit until the lift shaft recesses and floor slab had been concreted. In order to be able to detect any unexpected rises in the water table with sufficient warning time, PORR therefore had to constantly monitor the water level by means of probes. A sudden rise in groundwater levels could have delayed the project indefinitely. Thanks to the well-scheduled time window, and a little luck, the entire basement could be constructed in one dry construction pit and expertly caulked to the white tank.
Engineering solutions were not allowed, nor was it permitted to pump out water. The water level was monitored constantly.
Exposed concrete
The specifications set by the planners for the entrance hall posed a further challenge. The ceiling over the basement is connected to the entrance hall about halfway up the rear wall. A reverse bending connection was used to avoid a visible concreting section where the basement ceiling joins the entrance hall’s rear wall, and thus to connect the ceiling to the wall invisibly. In order to produce exposed concrete surfaces without horizontal joints, extra-long formwork units of 3.70 m were procured and the rear wall was concreted floor-to-ceiling in a single section.
Concrete column in the entrance hall
Due to the oversized dimensions, PORR fabricated the plate-like concrete column in the entrance hall directly on site. The columns’ unusual shape meant that they could not be formed without visible joints. In order to achieve the visual result desired by the architects, the execution of the joints, types of formwork and exposed concrete classes had to correspond exactly to the specifications. The combination of a transparent resin-coated travertine floor, the bright exposed concrete walls and columns, and the drop ceiling with wall washers created a spacious entrance area.
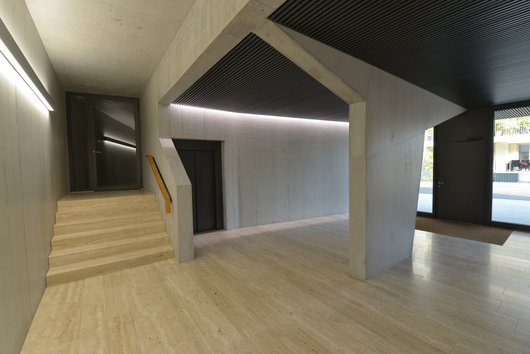
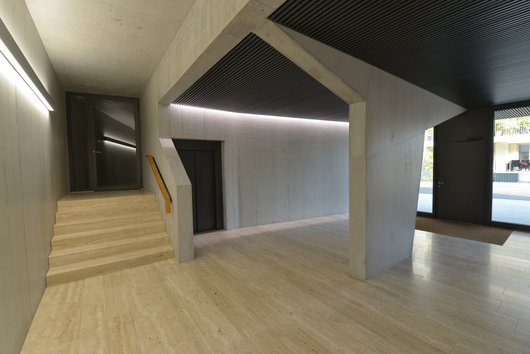
Sensitive dimensional tolerance compensation
Dimensional tolerance compensation between various subsections creates problems on many construction sites. Thorough planning was also necessary in the present case. The zigzag-shaped sheet metal building envelope, which also includes all window frames and projections and recesses for loggias, was designed on a 50mm grid. The complicated geometry and dimensional tolerances of the carcass made it difficult to
precisely align the sheet metal cladding in all three axes. In a few places, despite the utmost care, additional measures were necessary to accommodate any tolerances that had arisen during assembly. The architects’ scaled-back design meant that the ceilings sagged noticeably at large spans (5m). This problem was solved in consultation with the planners by installing a curtain board along the glass facade.
Ventilated metal facade
The ventilated metal facade gives the building a robust, durable and low-maintenance shell that functions perfectly in terms of the building physics. Here, PORR has broken new ground by not using the originally-intended standard product and instead manufacturing all the sheets individually. This made it easier to handle some of the complex corner details and allowed for tolerance compensation.
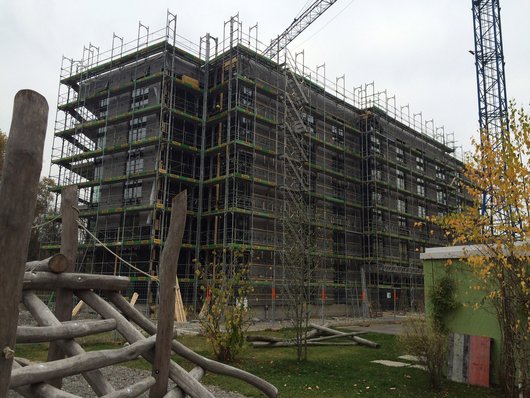
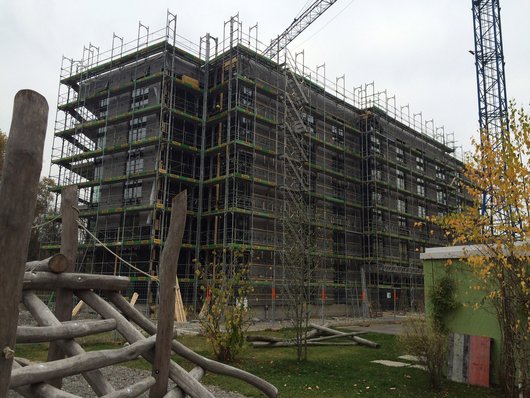
Sophisticated building technology
The heating and direct hot water supply for the whole of the Kunzareal area are provided by centralised district heating. All inlets and outlets can be found in the northwest corner of the building, where they enter the white tank system through Doyma seals. Thus even here, one hundred percent impermeability of the building is guaranteed. The flats are ventilated by monoblock units. The building is certified according to the Swiss Minergie standard for sustainable construction.
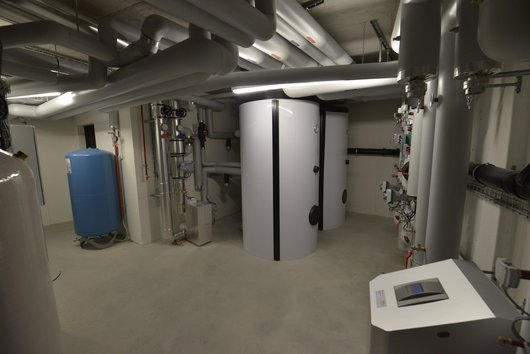
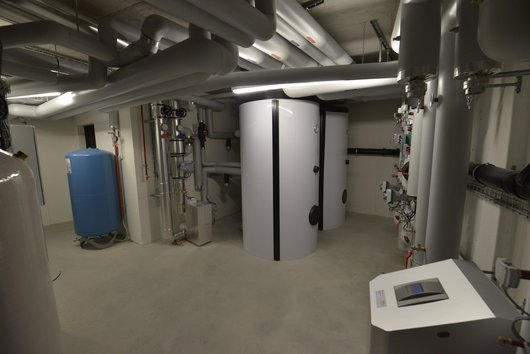
Technical data
-
Gross surface area4.618m²
-
Type of construction ISolid construction in concrete and brick
-
Type of construction IÍceilings in type 4 exposed
-
ConcreteC25/30, XC2, w/z = 0,55, Dmax. 32, C3
-
Reinforcing260.000kg
-
ConstructionFlat foundation; white tank system
-
Excavation4.200m³
-
Construction pitpartly in S3 groundwater protection zone
-
Building envelope IVentilated metal facade
-
Building envelope IIExtensive flat garden roof
-
EnergyDistrict heating
-
CertificationMinergie