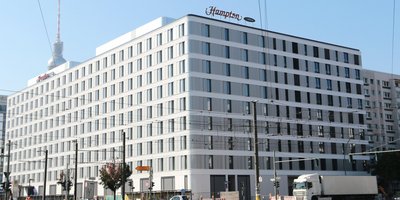
the Hilton Group's largest home
OBM Hampton by Hilton
In summer 2015, PORR Deutschland was awarded with a lump sum contract for the turnkey construction of a 10-floor hotel and residential building in Berlin-Mitte.
The largest Hampton by Hilton hotel in the world stands just a few minutes on foot from Alexanderplatz. The central location has many benefits for the guests, but not necessarily for the construction team.
-
EmployerLambert Wohnbau GmbH, Regensburg
-
ContractorPORR Deutschland GmbH, ZNL Berlin
-
Project typeBuilding construction, Hotel, Residential construction
-
Project scopeTurnkey construction of a hotel and residential building
-
Order volumeEUR 27.5 million
-
Construction start09/2015
-
Construction end08/2017
General & Initial situation
In spring 2015, construction started on the new Hampton by Hilton hotel in the heart of the German capital. With 344 rooms, a block with 40 rental apartments and a gross floor area of 19,000m², it was to be the largest of the brand’s hotels worldwide. The L-shaped building extends right up to the perimeter of the construction site and creates a half-open inner courtyard with green space and play areas. The execution planning was provided by the employer, Lambert Wohnbau GmbH. The complex consists of a basement (part of which is used for underground parking), a ground floor, and eight upper floors. It opened in May 2017.
For decades, the 4,200m² site stood undeveloped. Before the war, there was a main road and a few residentialbuildings. In the post-war years, it was left empty and used only as a car park, not least because of soil contamination. Due to the former road layout, various utilities cross the construction site, which had to be considered during planning and construction. These include a mixed water channel of 2.8m in diameter, an 80cm diameter fresh water pipe, as well as various gas, telecommunications, traffic signal and broadband lines. Furthermore, an additional strip of the construction site was to be kept free for a possible extension of metro line 3.
Thanks to our excellent cooperation, we were able to implement special solutions in the cramped construction field.
The project
Bridge construction of the apartment block
Because of the utilities criss-crossing the construction site, and the need for them to remain accessible for maintenance, parts of the construction site could not be built on.
It was also necessary to execute a part of the building as a bridge construction, since it was also impossible to build on this area. Due to the large open proportion of the outer walls, a single load transfer in the area of the first floor was not possible. In order to retain the slim profile of the supporting construction, and thus the same ceiling height as the adjacent hotel, approximately 200t of steel composite beams were used for load transfer in the floors above the passageway. Thus, each floor has reinforced concrete composite beams along the four main axes of the building. All inner and outer walls in the area overhanging the passage were constructed as non-load-bearing. This means that each floor is theoretically self-supporting as it spans the passageway. Despite the delicate design of non-load-bearing walls for noise protection, all sound insulation requirements could be met and exceeded.
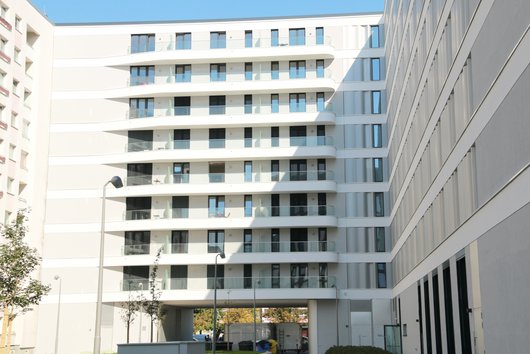
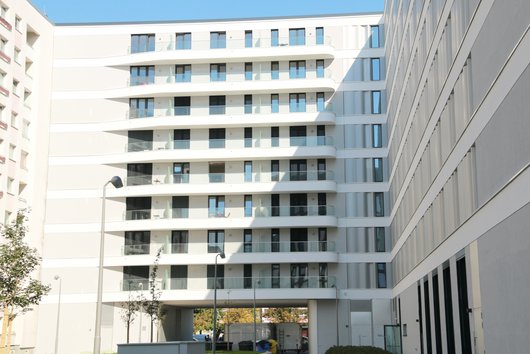
A further challenge posed by the bridge construction was the relatively small footprint on one side. Here, PORR’s specialists were faced with two problems: on the one hand, underpinning of the gable walls of the neighbouring buildings by high pressure injection, as is normally used in such cases, was not allowed by the owners, so instead of using a temporary construction pit system, a secant bored pile retaining wall with a two-level steel reinforcement was used; on the other hand, the footprint of the 10-floor high rise in this area was not enough for a raft foundation.
Therefore, extra foundation piles were constructed with diameters of 75, 88, 119 and 150cm. The borehole diameter of 1.5m and the pile length of 30m necessitated the use of BG 28 large drilling rigs. Because of the large number of bores required, and the short construction period, up to four large drilling rigs were in operation on the construction site at one time.
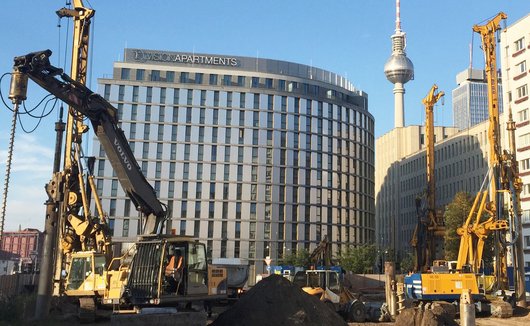
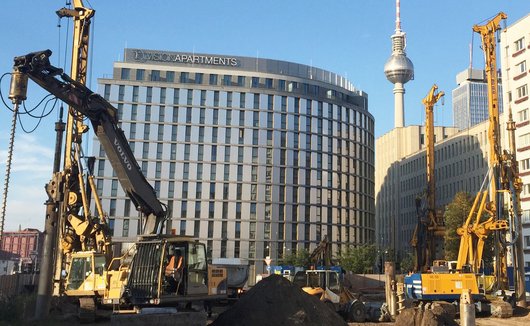
Vibration damping of the hotel building
When main traffic arteries and the public transport network meet, vibration and noise cannot be avoided. Precautions had to be taken to protect guests and residents. An analysis of structure-borne and secondary air-borne noise had already been carried out during the planning stage. As a result, an elastic building foundation was recommended, so that vibration from trams would not be transmitted through the soil to the building structure. Decoupling mats were laid underneath the floor slab along the course of the road, and completely in the area of the outer walls of the basement, to prevent the transmission of unwanted vibrations to the building.
Another challenge of this construction project was the ground water above the floor slab. Based on the existing parameters such as soil pressure, vibration frequency, groundwater level and compatibility with the fresh concrete composite foil installed in addition to the water-tight tank, a closed-cell elastomer vibration protection material called Slylodyn was chosen and dimensioned accordingly. The effectiveness of these measures was confirmed both by vibration measurements and in the positive feedback from hotel guests.
The wave effect facade
The facade is arranged in horizontally continuous balustrades with a fine plaster structure and an intermediate anodised aluminium perforated plate facade. The wave effect is intended to symbolise a raised curtain. The facade spans one leaf of each almost floor-to-ceiling double leaf window. The curved form is not only affected by perpendicular wind forces, but also those parallel to the facade. In order to ensure the correct force was applied to the plastic windows used in the upper floors, an aluminium extruded section was specially developed for the construction scheme, which surrounds the centre post of the window on the outside, and thus ensures the necessary rigidity of the overall construction. In this way, with a great deal of expertise, it was possible to implement the wave shape imagined by the architect.
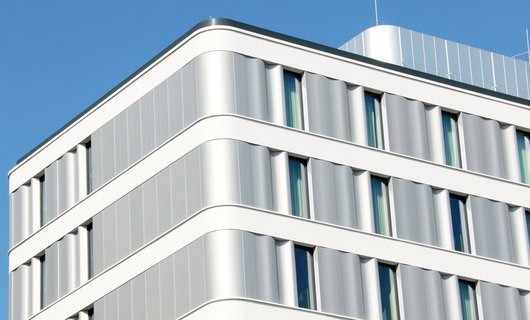
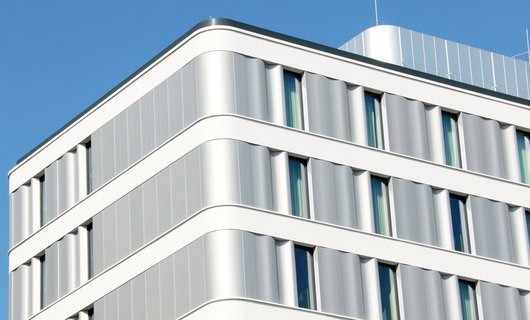
Reinforced concrete prefabricated bathroom pods
With the exception of the barrier-free bathrooms, all hotel rooms were equipped with prefabricated reinforced concrete bathroom pods. In contrast to a lightweight construction bathroom pod, it was possible to install the reinforced concrete pods in their final positions during the shell construction phase. In addition, it was possible to make the bath pod walls fire resistant and fire proof. Since the pods are less vulnerable to the effects of the weather than a lightweight construction bath pod, this is a decisive advantage for the speed of construction. In this way, connecting the bath pods to the riser only slightly delayed the shell construction progress, significantly improving the time needed for fitting out.
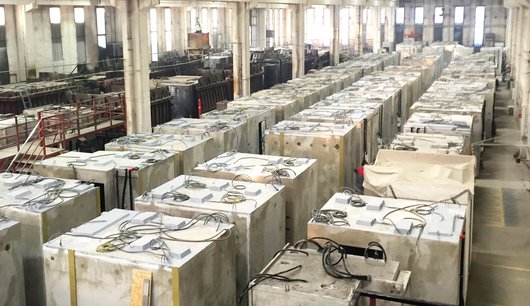
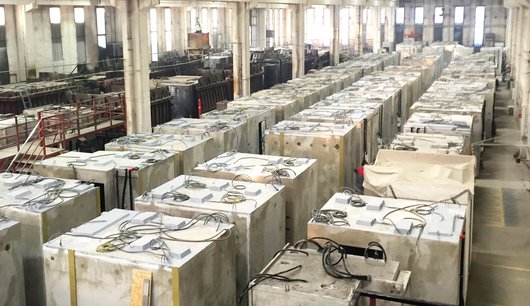
Technical data
-
Building units344 hotel rooms, 40 apartments
-
Excavated soil9.000m³
-
Equipment2 rotating tower cranes; 4 drilling rigs
-
Special featuresVibration-isolated building suspension
Summary
On a very challenging construction site, PORR has built a distinctive building which blends in well with the surrounding architecture. The construction requirements and time pressures were handled perfectly thanks to the great teamwork of the construction team.