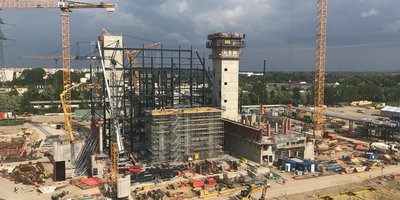
Marzahn CHP
Under contract to Siemens AG, PORR is constructing a foundation for one of the most modern combined heat and power stations in Europe.
The Marzahn CHP will provide district heating and electricity for 150,000 households, resulting in a significant reduction in CO2 emissions. PORR’s contribution to the project consists of main construction works plus the turnkey completion of four buildings.
-
EmployerSiemens Aktiengesellschaft Power & Gas
-
ContractorPORR GmbH & Co. KGaA
-
Order typeGeneralunternehmer
-
Project typeCivil engineering . Power station construction/Building construction/Civil engineering . Road construction
-
Project scopePlanning and complete turnkey construction of four buildings and execution of main construction works for the power station
-
Order volumeApprox. 30 million euros
-
Construction start09/2017
-
Construction end03/2020
Overview
The Berlin-Lichtenberg combined heat and power station, originally built in the 70s, was decommissioned in 2010. The project was opened for tender by Vattenfall Wärme Berlin AG in 2014, and Siemens AG was successful in securing the contract for the construction of one of the most modern combined heat and power stations in Europe. Most of the necessary plant components were sourced from the region around the German capital city.
The SGT5-2000E gas turbine was manufactured in the Siemens factory in Berlin-Moabit, while the SST-800 steam turbine came from Görlitz, around 200km away. Transformers, generators and switchgear were sourced from Dresden, Leipzig and Erfurt.
The role of main construction works for the power station and the complete turnkey construction of four supply buildings was assigned to PORR’s Infrastructure and Civil Engineering branch in Munich. Main construction works for the project include earthworks, numerous supply lines, foundations for the “power block”, two 45m-high stairwells, two turbine platforms, a switching station building, several auxiliary buildings and the necessary road construction.
The total value of these works amounts to around 23 million euros. The role also includes planning and turnkey execution of a block control room building, an administrative building, a social, storage and workshop building and a garage to the value of 7 million euros.
In deference to the tight schedule, very rapid-setting concrete was used. The stairwells were also heated and coated in frost protection mats over the weekend.
Logistical feat
The central element of the entire plant is the power block. This structure contains the two powerhouses for the turbines (UMA and UMB), two transformer buildings (UBC and UBF), the boiler house (UHA), the feed water pump room (ULA) and the switching station building (UBA). The project represented a major logistical challenge right from the start owing to the ambitious timetable, need for concurrent planning and the numerous subcontractors at work simultaneously.
The limited space of the site has had to accommodate a great deal of activity with the construction of a foundation plate for the structural steelwork, the turbine foundation, a vibration-damped turbine platform on columns, two staircases up to 45m high and the geometrically demanding switching station building. Constant coordination of the various lifting devices in use by the individual work teams, often operating in close proximity, was necessary to ensure safe working conditions. In spite of time pressure, workplace safety was a key issue on the construction site. Collaborative effort ensured that PORR’s construction site team put into practice the “seven golden rules” of PORR’s VISION ZERO for the reduction of workplace accidents and managed to satisfy the high safety requirements specified by end client Vattenfall for a power plant project.
Constant coordination of the various lifting devices in use by the individual work teams, often operating in close proximity, was necessary to ensure safe working conditions.
Complex turbine platform and staircases
On top of the site logistics, the turbine platform for the steam turbine was another significant challenge to be addressed. The supporting structure for the turbine and corresponding generator rests on six vibration dampers at a height of 15m. Falsework for the concreting was erected between the column-and-beam construction. This auxiliary structure formed the basis for a total of 45t of reinforcing steel, 170 built-in elements and 280m³ of concrete. The high reinforcement requirements and 10mm installation tolerances for formwork and built-in elements necessitated a high degree of concentration when positioning reinforcement. A unique concrete formula was developed to meet the high compression strength requirements, and this formula was initially checked in test rows and then monitored with temperature sensors throughout the concreting and subsequent hydration processes.
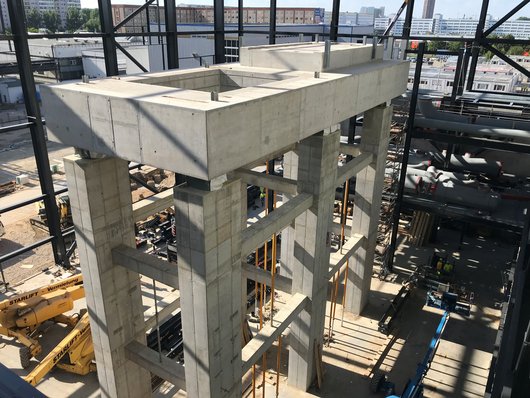
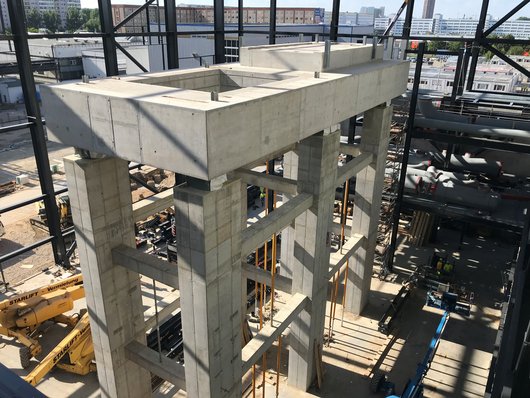
The two stairwells of the power block, which were completed with the aid of climbing formwork, also presented a genuine challenge. PORR’s team of experts outdid themselves in completing the climbing formwork, scaffolding the walls with their numerous niches and openings, and positioning the necessary reinforcement and earth. In deference to the tight schedule, very rapid-setting concrete was used. The stairwells were also heated and coated in frost protection mats over the weekends. Each Monday, the firmness of the concrete was assessed using test cubes before the next section of formwork was erected.
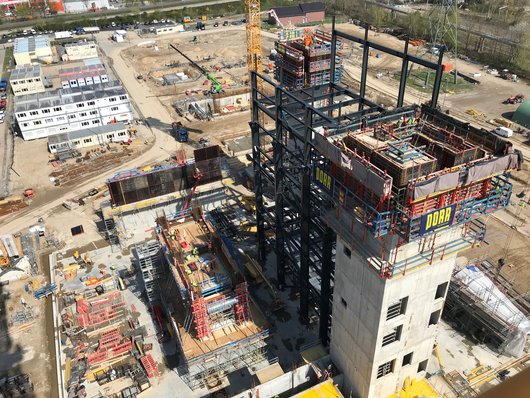
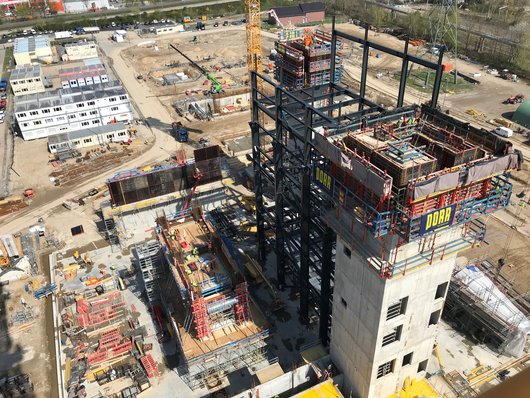
Turnkey construction
Along with works on the power station, PORR was also responsible for turnkey construction of the control room building, administration building, social, storage and workshop building and garage.
In future operation, the entire power station will be monitored and controlled from the UCA block control room building. Accordingly, the workplaces are arranged in an oval formation and connected to the adjacent server room via a double floor system.
The administrative building (UYA) contains office and training rooms, two server rooms, a first-aid room, a commercial kitchen and a cafeteria.
Replacement parts will be managed, plant components maintained and hazardous materials stored in the social, storage and workshop building (UST). A crane has been installed in the machinery room to facilitate these functions. The fourth building will serve as a garage for company vehicles (UYQ).
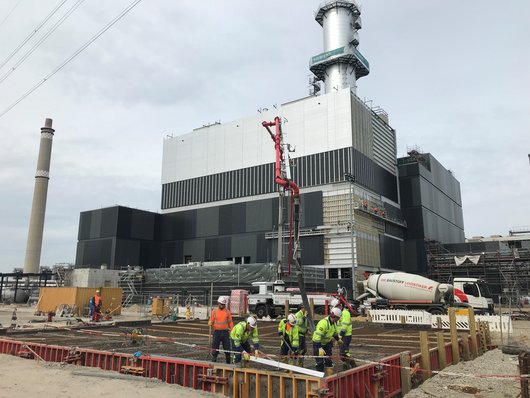
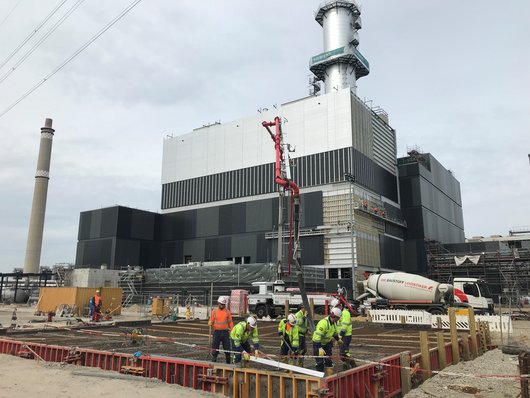
To offset the high demands in terms of formwork and reinforcement for the power station building, the auxiliary buildings were primarily constructed using double-shell walls and precast panels. In view of the span involved, the roof was made from prestressed concrete elements.
The high standards required of the technical building equipment for the building stipulated redundant systems for ventilation, climate control and lighting in all important operational areas. A battery installation in every building will ensure uninterrupted power supply in an emergency, and the batteries are designed to last until emergency generators begin operating. All the buildings also feature additional fire protection equipment. A large number of fire sections, automatic extinguishing systems, additional smoke extraction systems and fire alarms will assist employees on site as needed.
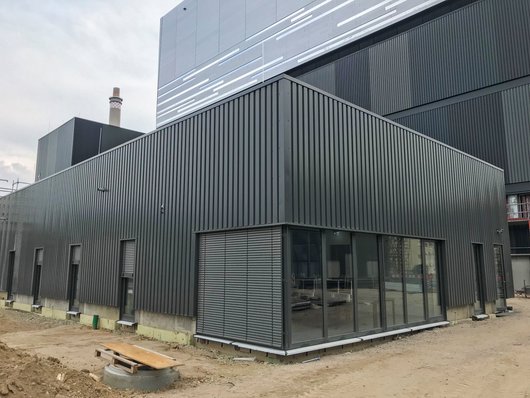
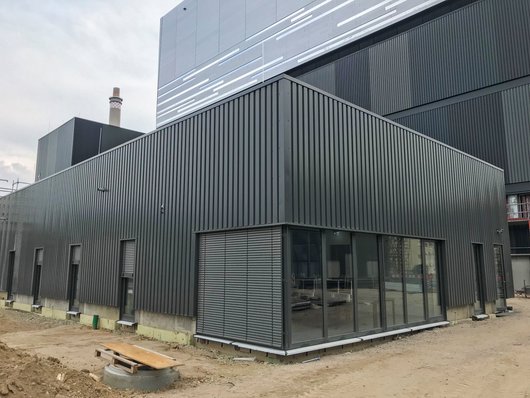
Subterranean network
Switching systems for the power block, block control room, auxiliary buildings and administration building are connected via a network of cable ducts and cable drum lines to ensure constant monitoring of all plant components of the power station. Cable drum lines form an additional element of the complex subterranean operation, alongside the gas pipeline, fire-extinguisher pipes, drinking water network, rainwater piping including rainwater retention basin and wastewater network. Cable ducts are buried at depths of up to 5.30m beneath all the buildings and peripheral plant components.
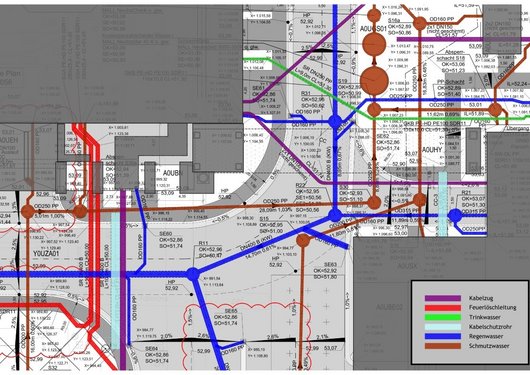
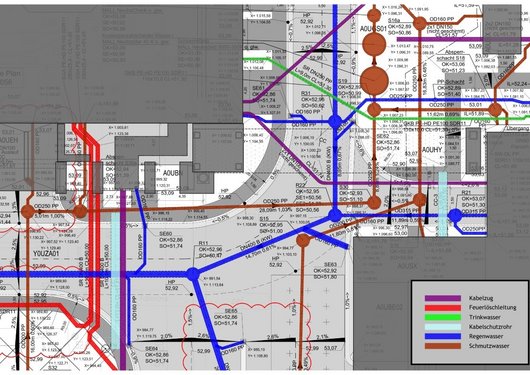
Key Figures
Since construction began in September 2017, PORR has done far more than just lay the foundations for the power station, employing around 20,000m³ of concrete, 2,000t of reinforcement steel and 15,000m of conduit in the area of the power block and auxiliary buildings. The basic shell construction was successfully completed and handed over to the employer in February 2018.
The PORR team is also responsible for outdoor facilities, finishing works, fire protection equipment and road construction. The four turnkey buildings are being constructed in cooperation with H+E Haustechnik und Elektro GmbH and will be handed over at the end of 2019, with overall completion to follow in March 2020.
Technical data
-
Excavation volume24,000m³
-
Concrete poured19,000m³
-
Reinforcing steel used2,000t
-
Earthing cable20,000m