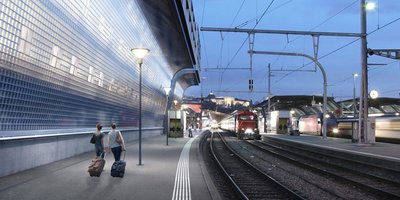
HB Nord – Glass Brick Façade Gleisarena
The Gleisarena office complex, being planned and built by PORR next to Zurich’s central station, has a curved striking glass brick façade.
The new glass brick façade, implemented by PORR in collaboration with Alu Sommer, represents a true technological milestone. The double-skin façade uses standard glass bricks, joined together with a thermal barrier to form a 212mm thick element.
-
EmployerSBB AG
-
ContractorPORR SUISSE AG
-
ArchitectMade in Sàrl, Genf
-
Order typeTotalunternehmer
-
Project typeBuilding construction . Office
-
Project scopePlanning and construction of a seven-storey head-end structure and a six-storey longitudinal building
-
Order volume40 million Swiss francs (35.9 million euros)
-
Construction start05/2017
-
Construction end02/2020
Background
Glass bricks give any project a special aesthetic appeal. However, their considerable structural drawbacks often present significant challenges for planning and implementation, particularly in the light of rising standards for heat transfer and noise insulation.
The 1500m² façade on the Gleisarena office complex in Zurich was a major undertaking in any case due to its size, but the architects at Made in Sàrl added to this complexity by incorporating numerous curves in the façade design.
The challenges this presented were more than merely technical, as the façade is also subject to specific requirements under labour law, such as providing an unobstructed view to the outside.
In spring 2017, PORR was selected as the general contractor for implementation of the project. Working with its subsidiary Alu Sommer, PORR planned and built the façade in accordance with the architects’ specifications. The innovative structure made it necessary to develop similarly innovative transport methods and assembly techniques.
The complete façade comprises a total of 24,000 cast glass bricks with a thermal barrier. The stainless steel profiles were prefabricated in the factory in stainless steel grids.
High degree of prefabrication
The complete façade comprises a total of 24,000 cast glass bricks each measuring 240 x 240mm, with a thermal barrier. The stainless-steel profiles needed to secure the structure were prefabricated in the factory as 1.50m x 3.0m stainless steel grids. The height of these elements corresponds to the height of the storeys in the building. While still in the factory, the glass bricks were pasted into these elements with glue on all sides. In addition, 100,000 specially developed plastic brackets were pressed and installed between the glass bricks and the steel framework to prevent the bricks from falling out of the framework if the glue should fail.
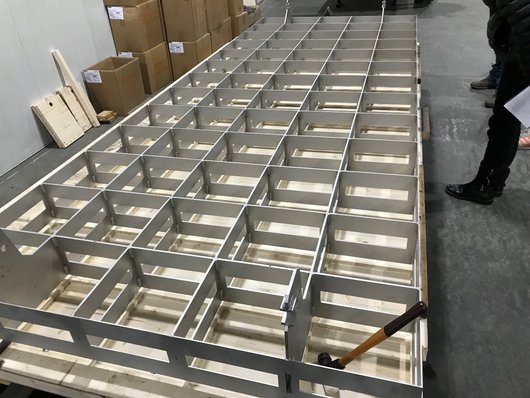
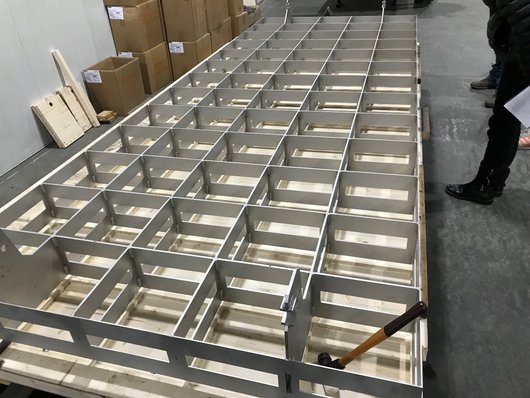
The carcass was fitted in advance with holders specially developed for the façade attached to Halfen channels installed on the front faces of the ceilings.
The façade was then mounted on the reinforced concrete building carcass. The carcass was fitted in advance with specially developed holders attached to Halfen channels installed on the front faces of the ceilings. The holders are special supports made of extrusion profiles that allowed for three-dimensional adjustment for fine-tuned positioning of individual elements. The elements were suspended on the built-in bolts using hooks on the rear side. This left assembly joints between the prefabricated elements at the heights of the ceilings, which were elastically jointed after installation.
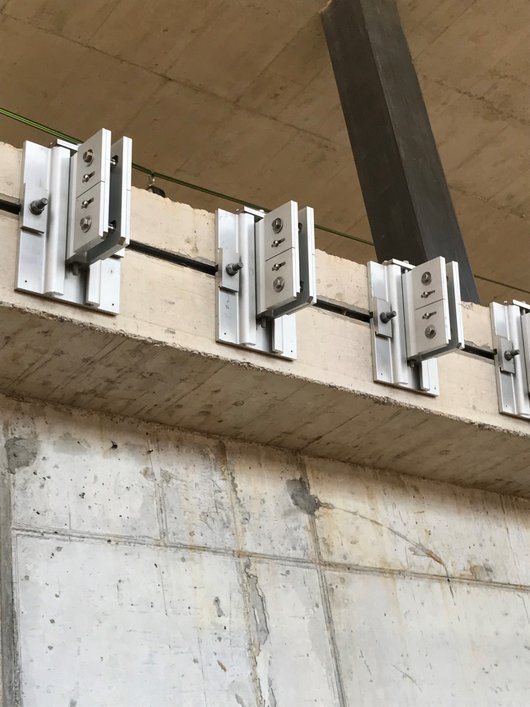
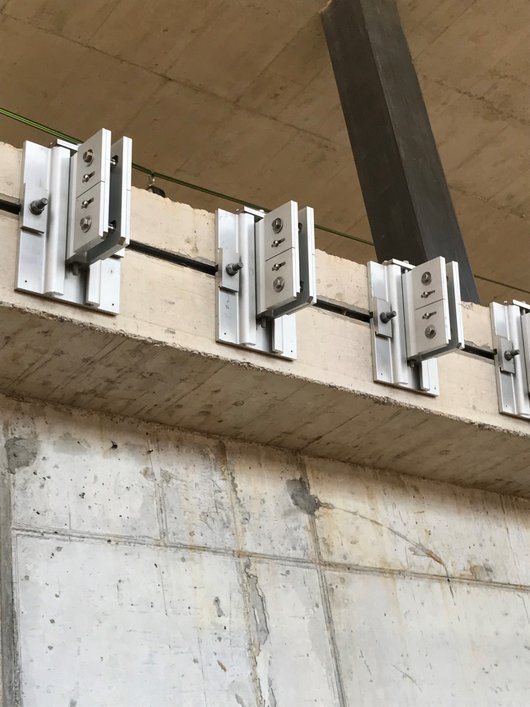
High complexity, low tolerances
With such complex geometry – an elliptical plan view, vertical inclination and a three-quarter circle formation above – tolerances were a minimal 1mm in each dimension. The support elements made it possible to reconcile this high degree of precision with the somewhat coarser carcass structure.
Alu Sommer developed a special measurement system for the façade to ensure the elements were adjusted correctly and engaged surveyors to assist with its implementation.
Since the glass brick façade extends over a number of storeys and neighbouring building elements, it was necessary to laminate wall and ceiling faces that would meet the inside of the façade.
This was achieved with reflective elements, which were also installed in the steeply arched overhanging sections of the façade. The reflective effect comes from the inner surface of the outer glass bricks.
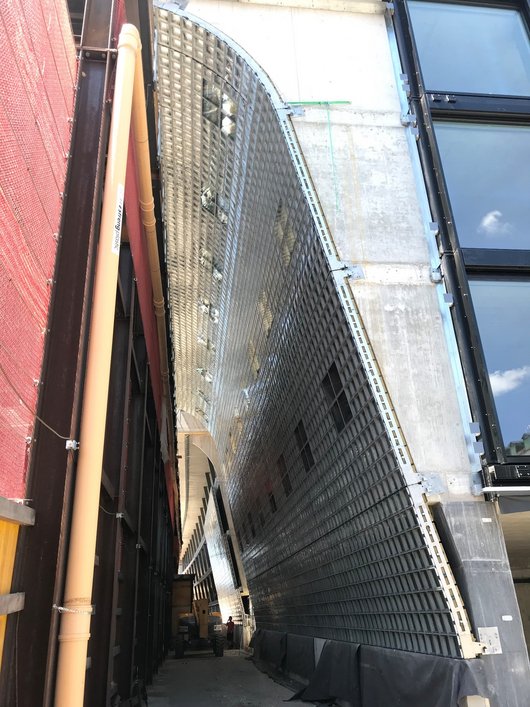
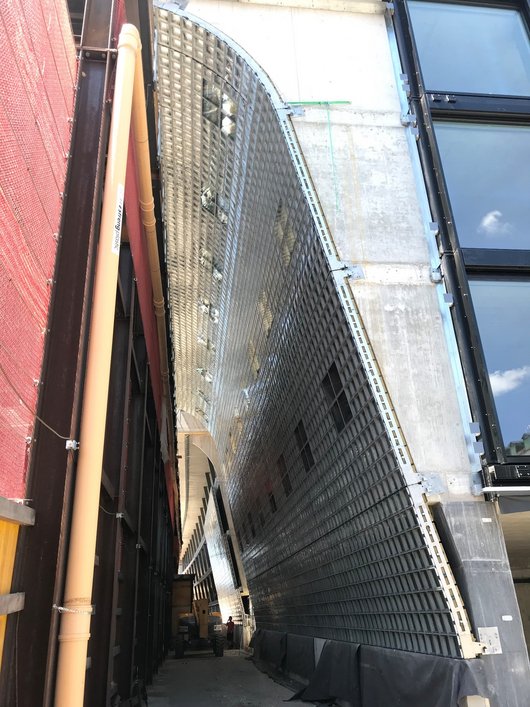
Technical data
-
Glass brick elements240 x 240 x 212mm
-
Horizontal mortar joints12–18mm
-
Vertical mortar joints15mm
-
Heat transfer coefficientUg= 0.8–0.95 [W/m2K]
-
Overall energy transmission factorg-value: 0.20
-
Light transmission factorLT ≥ 0.25
Construction and structural design
Structurally, the glass brick façade is equivalent to a traditional hanging façade, suspended from the ceiling faces on each storey. The vertical load transfer for the dead weight takes place through the mounting elements in the reinforced concrete ceilings. Loads from wind pressure and wind suction are similarly transferred from the stainless steel grid to the ceilings, via the suspension points.
Elaborate construction process
The complex geometric form and cramped conditions made installation of the glass brick façade particularly challenging. Elements were delivered to the site and then hoisted into their final position from a telescopic ladder inside the building, using special lifting frames. Various installation aids had to be developed to ensure the elements were positioned correctly during the lifting process.
All the elements are integrated into the building earthing through their suspension points; these form part of the concreted Halfen channels, which in turn have a metallic connection to the reinforcement. This makes it possible to discharge electric potential in the façade structure and provides lightning protection. This design also reduces the electrosmog resulting from the proximity to the train lines and their overhead wires, which generate powerful electric fields.
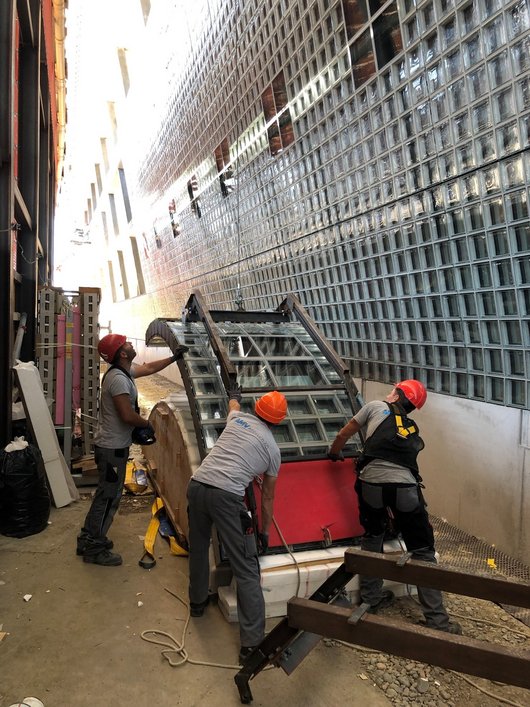
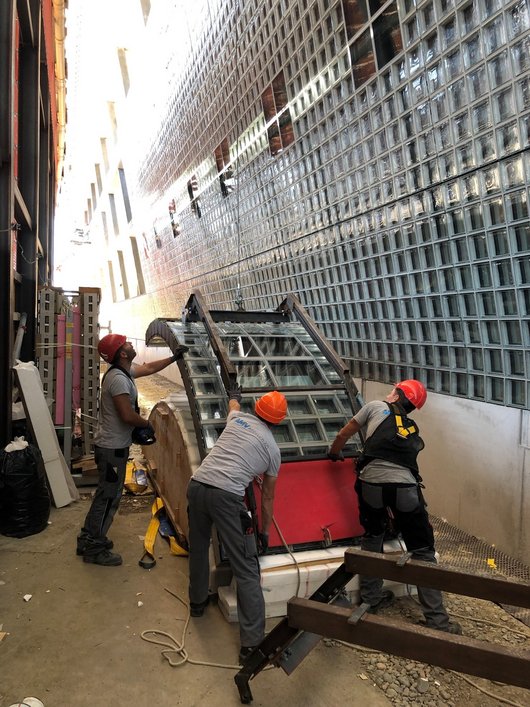
Summary
Glass bricks have a special aesthetic charm that comes to the fore in large-scale designs. However, their poor structural characteristics in comparison with other façade types have typically counted against them. The new façade developed by PORR for the Gleisarena office complex in Zurich represents a milestone in the use of the glass bricks for façade construction. As well as meeting the latest technical standards, the façade boasts a highly complex geometry. PORR is delighted to have had the opportunity to implement this façade structure, and the PORR employees have every right to be proud of the high-quality result.